Three Smart Factory Trends that Pay Big Dividends
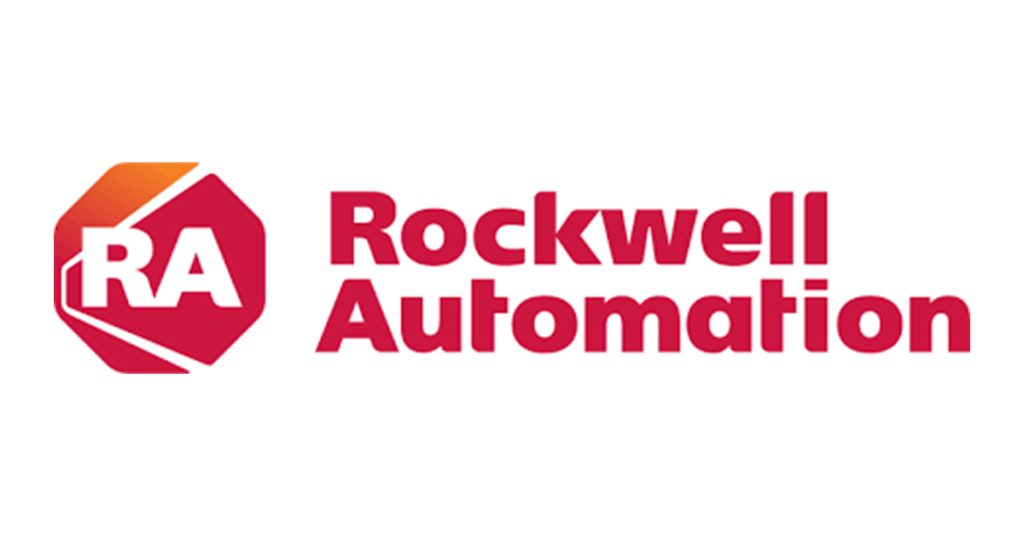
January 21, 2025
Networked Motor Control Center Technology Accelerates Productivity, Savings & Safety
By Diego Wilches, Global Product Manager, IEC LVMCC
Rockwell Automation has seen manufacturers around the globe investing billions of dollars in smart manufacturing and production plants. Industry experts project the demand for smart factories will double by 2032 to $322 billion because of the increased return on investment.
At the heart of smart factories are smart motor control centers (MCCs). These industrial control units contain networked motor control technology, power distribution and electrical switchgear to manage critical factory equipment and provide a constant flow of data from the equipment.
Rockwell Automation is a smart motor control center market share leader in North America – following NEMA standards and the company introduced the FLEXLINE 3500 low voltage MCC for customers in Europe, Asia, Middle East and South America – following IEC standards.
FLEXLINE 3500 motor control centers use networked devices to connect processes and people with real-time production data. As result, companies can increase productivity, save energy, reduce downtime and/or improve safety. FLEXLINE LV MCCs deliver value to each of these three manufacturing trends:
1. Creating a Smart Factory and Facilities
Manufacturing and commercial sectors are facing unprecedented growth opportunities by using connected technologies. Smart MCCs use EtherNet/IP to integrate technologies such as process automation software, smart motor control equipment and real-time data to increase operational efficiency and productivity. Plus, connected MCC technology can be monitored remotely 24/7 and a networked system helps reduce downtime, improve product quality and increase production capacity.
2. Integrating Artificial Intelligence (AI) and Predictive Maintenance
Artificial intelligence and advanced analytics tools are transforming manufacturing. The software and technologies inside smart motor control centers let customers collect and analyze huge amounts of real-time data to improve production.
Adaptive control technologies change to operating conditions and adjust to maintain production. Predictive maintenance alerts engineers when to replace components before they break. Artificial intelligence monitors critical production assets, such as drives, pumps and transformers. These predictive technologies can deliver up to a 40% reduction in maintenance costs and 70% decrease in downtime.
3. Increasing Safety and Sustainability
Increasing safety is fundamental to today’s motor control center design. FLEXLINE 3500 MCCs meet IEC 61439 1&2 standards, offer arc-flash-resistant technology, plus deliver remote operator visibility to monitor and diagnose the motor control equipment.
In addition, smart motor control equipment helps companies achieve their sustainability goals. The variable frequency drives can lower energy use by up to 50%.
“We survey thousands of manufacturers annually, and almost 75% identify smart manufacturing solutions as critical to their success,” says Diego Wilches, global product manager, Rockwell Automation. “Our connected FLEXLINE 3500 MCC technology delivers real-time operation data, letting manufacturers see and solve problems before they occur.”
“In manufacturing and processing operations, every production minute counts,” he continues. “With our integrated network infrastructure and smart devices, engineers can access motor control center data from anywhere. Having real-time data at your fingertips lets employees make smart production decisions. These decisions can deliver millions of dollars in savings and production improvements.”
For FLEXLINE 3500 motor control center specifications and product information, visit rok.auto/flexline.