HELUKABEL: Q & A With HELU – Cable Solutions for Glass Manufacturing
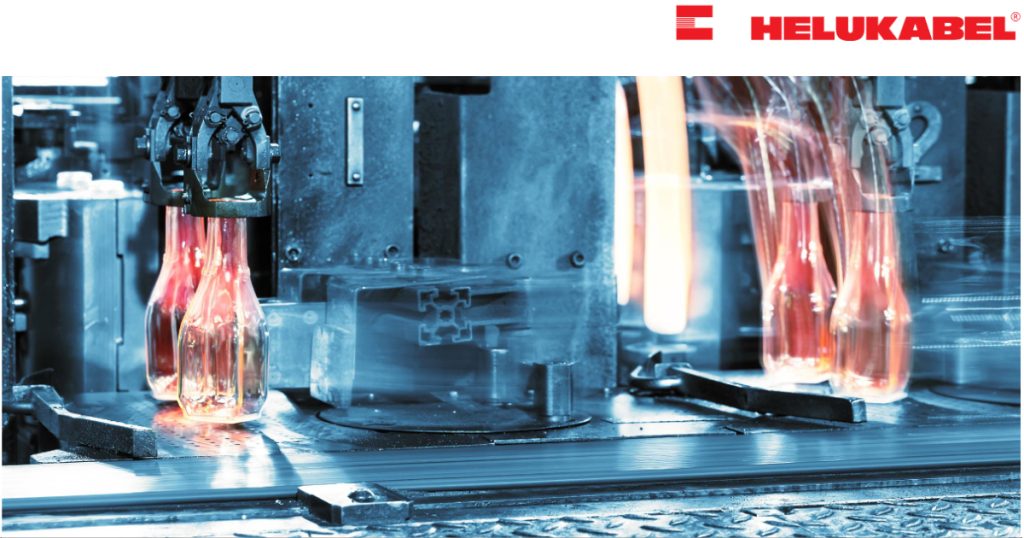
February 21, 2025
HELUKABEL Provides Insights Regarding Cable Solutions in Glass Manufacturing
In the glass manufacturing industry, various types of cables play essential roles in powering equipment, monitoring temperatures, and ensuring safe, efficient operations. Due to the high temperatures, heavy machinery, and automation involved in glass production, specialized cables are required to withstand extreme conditions, transmit data reliably, and maintain overall system safety.
This Q&A explores the different types of cables used in glass manufacturing, their specific functions, and the reasons behind their application in different stages of the production process. Let’s delve into the key cable types and understand their roles in enabling the production of high-quality glass products.
Q: What Types of Cables Are Most Commonly Used in Glass Manufacturing & What Roles Do They Play?
A: In glass production, various types of cables are used, each serving a distinct purpose to ensure seamless operations in high-temperature and high stress environments. Here are some key types:
Power Cables
In glass production facilities, high-voltage power cables (e.g., XLPE and MV cables) are commonly used to supply power to large equipment, such as kilns, and furnaces involved in melting and forming glass. They must withstand high temperatures and often require extra insulation or shields to resist environmental stresses. Equipment that requires voltage ranges less than 600 volts to operate oftentimes will use service cords such as SOOW or SJOOW, which have more durable rubber jackets to withstand the tough environment of the production plant.
Control Cables
Control cables are essential for transmitting signals between automated equipment, such as conveyors, robots, and control panels. They connect various automated systems to manage tasks like temperature control, conveyor movement, and cutting machines to precisely handle and shape the glass, which helps maintain efficiency and accuracy in the manufacturing process. Control cables often come with shielding to prevent interference and may also have heat-resistant coatings if installed close to hot production areas.
Instrumentation Cables
These cables connect sensors and instrumentation devices that monitor parameters like temperature, pressure, and chemical composition. Accurate data transmission ensures precise control over the quality of the glass. Instrumentation cables with low capacitance and shielding are preferred to ensure signal integrity and protect against electromagnetic interference in the factory setting.
Fiber Optic Cables
Fiber optic cables are primarily used for communication and data transmission between different sections of a glass production facility such as control systems and remote monitoring locations. These cables offer high-speed data transfer, are resistant to electromagnetic interference, and can withstand the high temperatures typically found in glass manufacturing environments, making them ideal for monitoring systems and real-time control of the production process. Single-mode or multi-mode fiber optics are chosen depending on the distance of data transmission requirements.
Thermocouple Extension Cables
Thermocouple cables are used to monitor temperature in key stages of glass production, especially in the furnace, where precise temperature control is crucial for melting and forming glass. These cables are specialized to match the thermocouple type (e.g., Type K or J) and must be rated to carry signals accurately at high temperatures without degradation to enable operators to make adjustments and maintain optimal conditions.
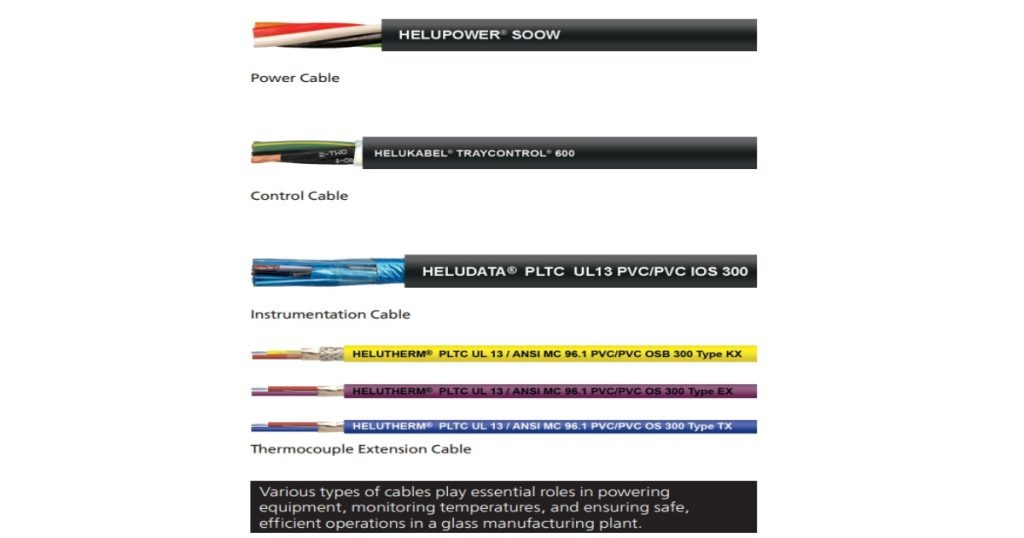
Q: Why Are Heat-Resistant Cables Important in Glass Production & What Materials Are Used to Enhance Cable Heat Resistance?
A: Cables capable of resisting high temperatures are critical in glass production due to the extreme temperatures near furnaces and ovens, which often exceed 1,000°C. Heat-resistant cables are vital to prevent melting, degradation, and potential electrical failures that could disrupt production or cause safety issues. Materials like silicone rubber, fiberglass, and mica are commonly used for insulation, as they can withstand extreme temperatures and offer durability. High-temperature alloys and stainless steel may also reinforce cables used directly in or near furnace areas.
Q: Are There Specific Industry Standards For Cables Used in Glass Manufacturing?
A: Yes, various standards apply depending on the region. Manufacturers should adhere to North American standards in the U.S. and Canada, particularly for insulation ratings (UL 83/CSA C22.2 No. 38) and fire resistance in high stress environments (UL 1685/CSA FT-4). Other standards might include UL 1277 (Electrical Power and Control Tray Cables), UL 62 (Flexible Cord and Fixture Wire), UL 1063 (Machine Tool Wires and Cables), and UL 758 (Appliance Wiring Material – AWM).
In Canada, CSA C22.2 No. 230 (Tray Cables), CSA C22.2 No. 239 (Control and Instrumentation Cables), CSA C22.2 No. 210 (Appliance Wiring Material Products), and CSA C22.2 No. 96 (Portable Power Cables) are a few standards that should be met based on the cable being used within the manufacturing plant. Globally, cables often need to meet high-temperature endurance standards such as IEC 60502 (for power cables), IEC 60228 (conductors), and others specific to high-voltage or high-heat applications.
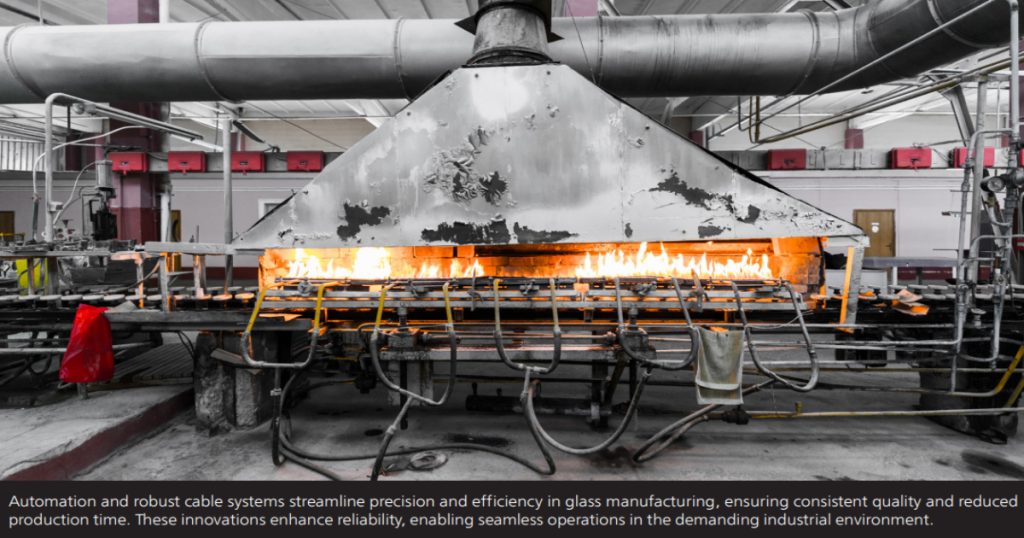
Q: What Are Some of the Challenges In Selecting Cables for Glass Production & How Are They Addressed?
A: The primary challenges include high temperature, chemical exposure, and potential mechanical damage due to vibrations or physical contact with machinery. Selecting cables with the appropriate insulation, heat-resistant materials, and durable shielding addresses these issues. Some setups might use additional protective conduits or specialized mounting to reduce wear and tear.
Q: Why Are Armored Cables Preferred For Certain Areas Within a Glass Production Facility?
A: Armored cables, which have a protective metal layer, are used where cables might be exposed to physical damage, such as from heavy machinery or moving equipment. In glass manufacturing plants, these cables ensure durability and protection from abrasions, impacts, and high temperatures, reducing the risk of cable failure and electrical hazards.
Q: Can Plastic And/or Metal Drag Chains Be Used in Glass Production Facilities?
A: Yes, metal chains are used when unsupported carrying spans exceed a certain length or a guide trough is unable to be utilized due to space restrictions. Metal chains are advantageous in high-temp environments and when fill packages are extremely heavy. Polymer (plastic) chains are a cost-effective approach for either short or long travel lengths. This is achieved by having the upper run of the cable carrier “glide” on the lower run allowing it to traverse up to 1,312 feet (400 meters). Either way metal/polymer chains are the maintenance-free solution to festoon, cable reel, and bus-bar systems.
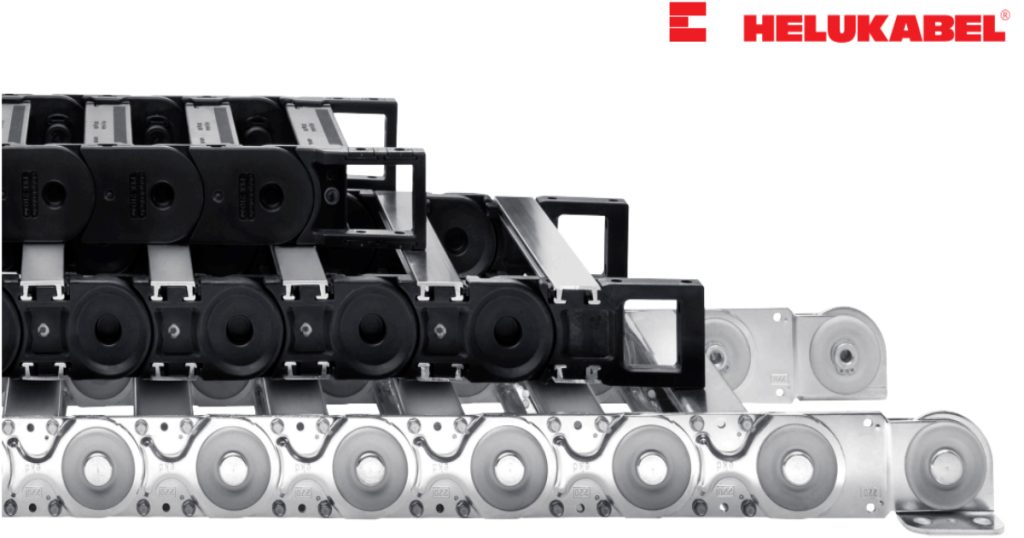