Kraken Awarded $1.8M in Project Funding to Develop Mooring Chain Laser Inspection Sensor
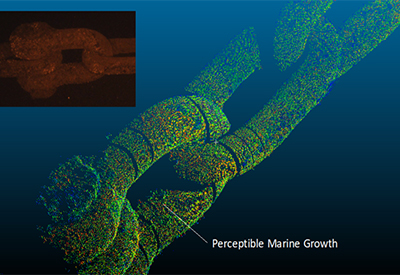
Aug 8, 2019
Kraken Robotics announced that following successful trials with Husky Energy, its wholly owned subsidiary, Kraken Robotic Systems, has been awarded funding for the development of a mooring chain laser inspection sensor, for use in offshore oil and gas applications. Under the project, a total of $1.8 million of funding is being provided in cash and in-kind services from Husky ($1.26M) and the Government of Newfoundland and Labrador, through the Innovation and Business Investment Corporation ($540,000). The project cash component received by Kraken will be $720,000.
In October 2018, Kraken and Husky collaborated to test Kraken’s SeaVision 3D underwater laser imaging system as a potential inspection tool for mooring chains at the SeaRose Floating Production, Storage and Offloading (FPSO) vessel. This demonstration showed that Kraken’s SeaVision technology can complete an inspection of a mooring chain and provide all the specifications required by the regulators. Under this new 16-month development project, Kraken will work with Husky to address remaining technology gaps identified, with a view towards future commercialization of SeaVision as a contactless inspection tool for the offshore oil and gas industry.
Mooring chains are a key component that anchor FPSO vessels to the seafloor. FPSOs are commonly used in the oil and gas industry and there are presently two in production off the Grand Banks of Newfoundland (Terra Nova and SeaRose). Today, there are over 250 FPSO vessels deployed worldwide.
A floating facility has multiple mooring legs composed of multiple links, each link is approximately one metre in length and 15 cm in bar diameter. The mooring chains are constantly in motion (up to 1 m/s) through the water column as the floating facilities are subjected to environmental conditions. Asset integrity regulations require regular inspections of the mooring chains at defined regions with millimetric accuracy to monitor for signs of wear and verify system integrity.
Current practice for mooring chain inspection requires a large support vessel, to deploy a work class remotely operated vehicle (ROV), which carries a mechanical calliper on its hydraulic manipulator. While the chain is moving in the water column, the ROV pilot must grasp a chain link to perform the required measurement. This process must be repeated several times, sampling several links in each mooring chain. The identified concerns with the current process include: i) efficiency; ii) risk; and, iii) environment.
Kraken’s laser scanning sensor solution will perform contactless mooring chain inspection from a two-metre stand-off distance and continue to provide the required accuracy. The advantages of this solution will be: i) speed: SeaVision® only requires a few seconds to measure a single link; ii) safety: contactless measurement at distances of two metres; and, iii) reduced environmental concerns: SeaVision® is an electro-optical piece of equipment.
Subject to successful trials and acceptance by certifying authorities, Kraken’s laser sensor technology will be offered to the oil and gas and offshore wind markets by Kraken as an inspection service, with applicability for all floating assets permanently moored to the seafloor.
With respect to the oil and gas market, it is estimated that the SeaVision® scanner sensor technology would reduce a mooring chain inspection campaign from approximately ten days to two days, which represents a significant improvement in efficiency and cost.
The technology is also of relevance for the upcoming market of floating wind farms. Each floating wind farm is expected to have over 50 mooring legs per farm, which is five times more than an oil and gas floating facility. Offshore wind is expected to see significant growth and floating wind farms will create new growth opportunities for this technology. According to industry analysts, there are currently 50 floating units in projects under development out to 2022, worldwide, but that number could increase to 300 floating wind turbines by 2025 and over 1,500 by 2030, a fivefold increase. The global floating wind market has enormous potential and a cost-effective mooring chain inspection tool is one of the technology gaps identified by floating wind farm operators.