Yaskawa: How to Design High-Power Electrical Enclosures, Seven Climate-Control Factors
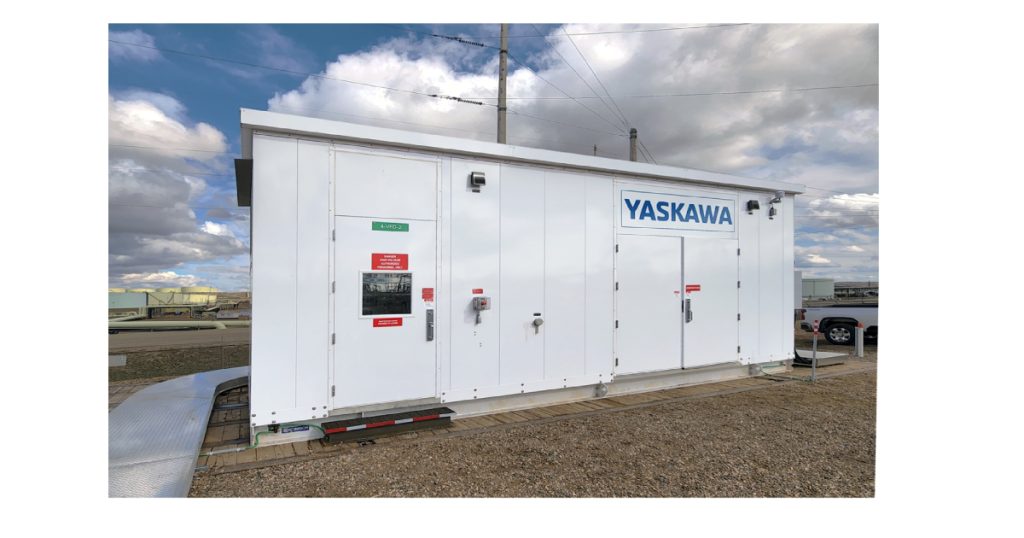
February 14, 2025
Yaskawa: How to Design High-Power Electrical Enclosures, Seven Climate-Control Factors
By: Lucas Paruch, Sr. Development Engineering Manager for Medium Voltage Drives at Yaskawa.
Benefits of dynamic air mixing for temperature and humidity control help with the environmental and other key considerations when designing and installing electrical enclosure for high-voltage electrical equipment.
Learning Objectives
- Understand how environmental and electrical characteristics and air mixing are important for hybrid electrical enclosure design and temperature regulation.
- Explore diagrams explaining how air mixing in electrical enclosures helps with humidity regulation, controls and maintenance.
- Learn about cost and reliability of outdoor electrical and control enclosures design.
Electrical Enclosure Climate-Control Insights
- Environmental and electrical characteristics and air mixing are important for hybrid electrical enclosure design and temperature regulation. Consider temperature, humidity, dust, ice, heat dissipation, sensitivity to high/low temperatures and humidity.
- Diagrams explain how air mixing in electrical enclosures helps with humidity regulation, controls and maintenance.
- Lifecycle costs, reliability and maintenance are key considerations with outdoor electrical and control enclosures designs.
The installation of electrical and controls equipment in outdoor environments requires careful consideration of the environmental extremes (temperature, humidity, dust, ice) and the characteristics of the installed equipment (heat dissipation, sensitivity to high/low temperatures and humidity). Understanding these seven attributes helps with high-powered electrical enclosure designs and specifications for electrical and control enclosures.
Environmentally sealed enclosures, such as the National Electrical Manufacturers Association (NEMA) 4X standard, are attractive for equipment with minimal heat dissipation. For small power conversion equipment and other heat-producing electronics, installation of stirring fans can help dissipate heat within the enclosure and may increase the rate of thermal radiation from the enclosure walls. For high-power equipment, the rate of heat transfer by passive radiation is often insufficient to maintain acceptable internal operating temperatures.
For many mid-size applications, an air-to-air heat exchanger or air conditioning system may be considered to provide active cooling. Both solutions reject heat and maintain a clean and dry operating environment inside the enclosure. Disadvantages of active cooling include initial cost, physical size, weight, operation costs and maintenance costs. For a small kilowatt scale application, the benefits of active cooling likely outweigh the disadvantages. For megawatt scale applications, the lifetime cost and size of active cooling solutions may quickly become impractical.
Ventilated enclosures (the NEMA 3R standard) provide a solution to cooling large equipment with minimal cost and size constraints. Depending on power requirements, ventilated enclosures may be passive (convection) or forced (fan-cooled). However, introducing ambient outdoor air to the enclosure is not without risk.
Dust ingress may be addressed by adding intake filters. Like air conditioning solutions, the cost and logistics of filter maintenance and monitoring must be considered. Applications installed in extreme cold climates must consider the temperature of the intake air, and its effect on installed electronics. Moisture must also be carefully considered, including potential condensation or frost that may result from natural daily thermal cycles.
Air Mixing, Hybrid Electrical Enclosure Design
An effective solution for high power applications is to implement a hybrid climate system that combines the beneficial characteristics of sealed enclosures (protecting against extreme cold and controlling moisture) and ventilated enclosures (allowing greater heat dissipation), while minimizing their respective disadvantages.
As an example, consider a 5 MW (approximately 5000 HP) medium voltage variable frequency drive application. If the equipment is 98% efficient, the system must dissipate 100 kW of heat.
Using a sealed 4X enclosure and relying on thermal radiation is not practical (a large enough enclosure would fill a quarter of a football field). An appropriately sized 6000 W/°K cross flow heat exchanger may be an option, but would approach the physical size of a shipping container. A 30-ton air conditioning unit may be smaller than a heat exchanger, but comes with a higher initial cost and higher operation and maintenance costs.
Incorporating active air dampers into the design of climate systems for large outdoor equipment enclosures enables the flexibility to dynamically control how much (if any) ambient outside air is drawn in to the enclosure for optimal temperature and humidity control.
Air Mixing: Temperature Regulation
During periods of light load (and corresponding low heat dissipation), extreme cold outdoor ambient temperatures (such as -40°C/-40°F or below), or extreme high outdoor ambient humidity, a dynamic cooling system may be designed to respond to temperature and humidity inputs by opening and closing mechanical air dampers. By closing the intake and exhaust dampers and opening a recirculating damper (as shown in Figure 1), the internal circulation of warm, dry air can be maintained through the VFD (or other equipment).
By providing proportional fan speed control, the system can optimize the circulating airflow for the load and environmental conditions, increasing fan life, reducing filter maintenance and reducing fan energy consumption. Enclosure space heaters may be incorporated as a supplemental heat source during extreme cold or when the equipment is idle and minimum equipment operating temperature must be maintained.
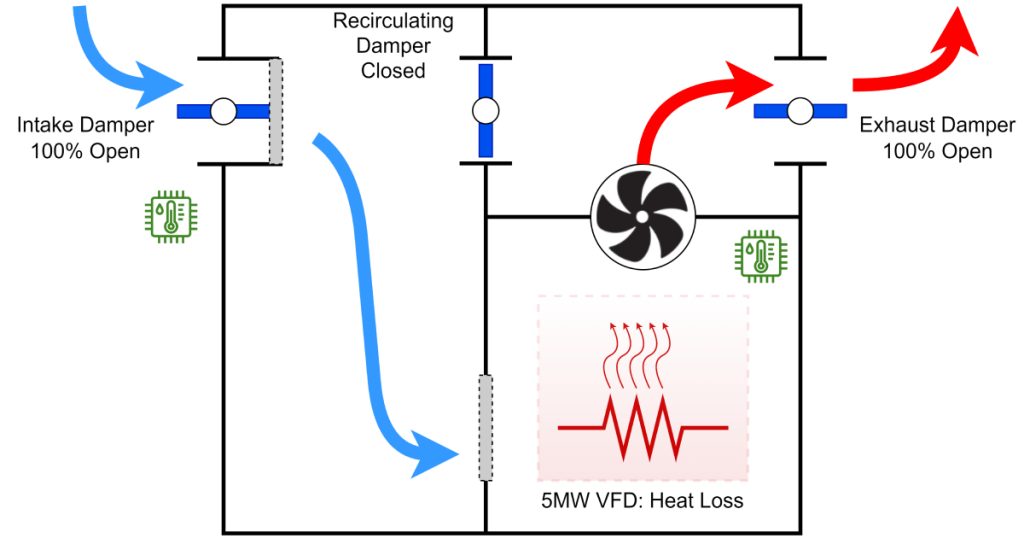
As outdoor ambient temperature increases and/or load increases, the climate system may dynamically adjust intake and exhaust dampers to maintain optimal operating conditions and avoid VFD over-temperature. Allowing the warm, dry air inside the enclosure to blend with cooler, potentially moist ambient air (see Figure 2), lowers the temperature of the circulating cooling air while maintaining acceptable humidity levels. Since fresh air intake is minimized in this state, dust ingress is also minimized, prolonging the maintenance interval required for filter cleaning.
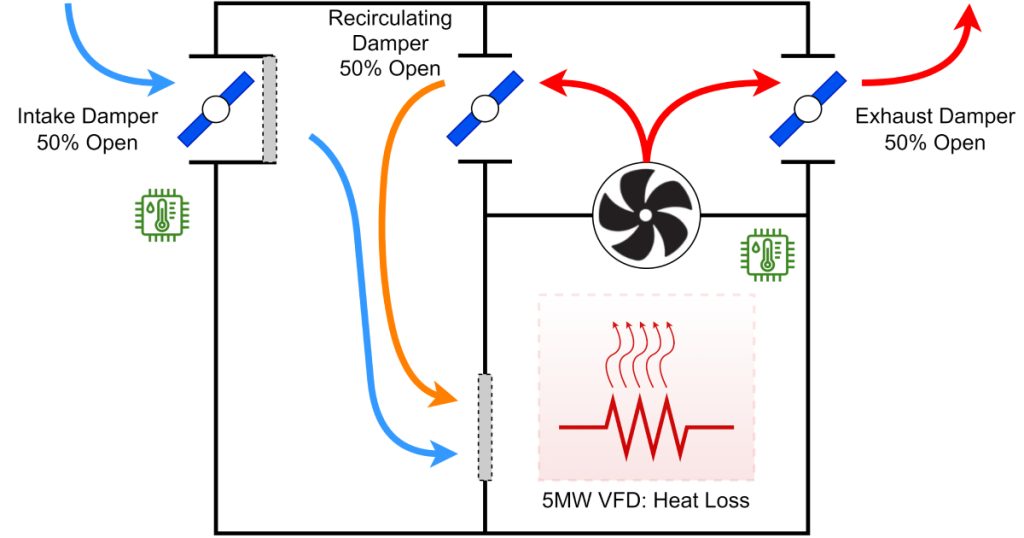
During periods of high outdoor temperature and full load operation, air mixing may not provide sufficient cooling effect. When this condition is detected, the climate system automatically transitions to full air exchange (operating as a conventional fan ventilated NEMA 3R enclosure, as shown in Figure 3).
When ambient and operating temperatures are high, relative humidity tends to be low, and the risk of condensation is minimal. Fresh air, twice filtered, is drawn directly through the equipment heat sinks, providing maximum cooling capacity. As with the conditions illustrated previously (Figures 2 and 3) the climate system provides proportional fan speed control to optimize airflow while minimizing dust ingress and power consumption.
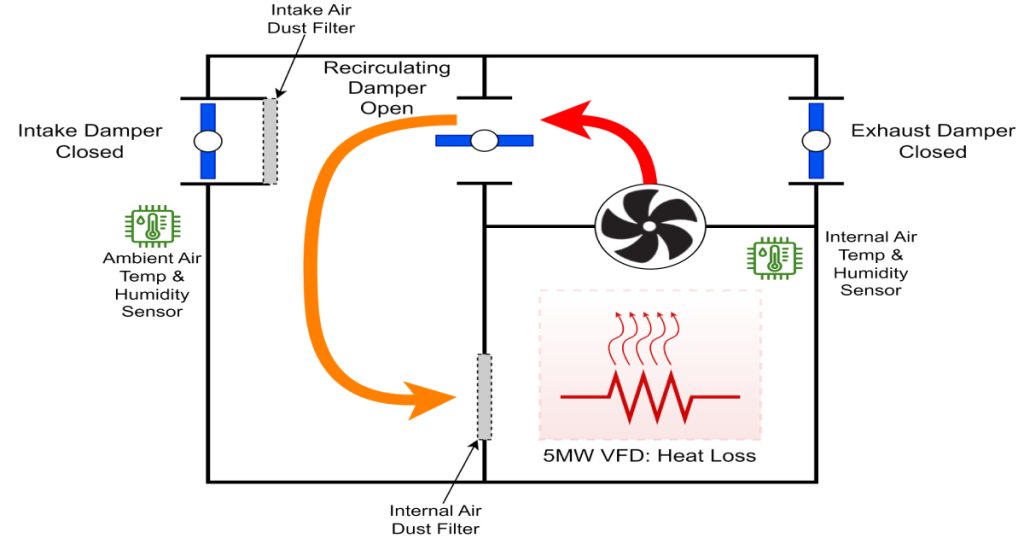
Implementing an active air mixing design combines the cold-climate heating benefits of a non-ventilated enclosure with the hot-climate cooling benefits of a fan-ventilated enclosure.
Air Mixing in Electrical Enclosures Helps With Humidity Regulation
The ability to dynamically control the blending of warm enclosure air with cooler outside ambient air is also beneficial for humidity and condensation control.
Absolute humidity is a measure of water mass in a given volume of air (typically expressed in g/m3). Absolute humidity is independent of temperature, it is simply a measure of how many grams of water vapor are present in a fixed volume of air.
Relative humidity may be expressed as the ratio of water vapor mass in a given volume of air to the water vapor mass required to saturate the same volume of air at the same temperature. Air at 100% relative humidity is saturated, meaning the air is holding as much water mass as can possibly be absorbed (for a given temperature). Likewise, air at 50% relative humidity is carrying half as much water mass as is possible to absorb (for a given temperature).
Relative humidity is a function of temperature. As the temperature of a fixed volume of air decreases, the relative humidity of that volume of air increases (because cooler air can absorb and hold less moisture). When the relative humidity reaches 100%, the air is fully saturated, and condensation occurs as water vapor is converted back to liquid water. Throughout this process, the actual mass of water (sum of vapor and liquid) remains the same.
To avoid condensation in electrical enclosures, space heaters are often provided. Heat is applied to reduce the relative humidity of the air within the enclosure. Fixed hygrostats are commonly available to control enclosure heaters and maintain relative humidity levels below 60% to 70%. Maintaining a maximum relative humidity of 60% ensures that, even in the event of sudden cooling, the relative humidity of the air in the enclosure is conservatively below the 100% saturation level at which condensation may occur.
It is important to understand that the relationship between relative humidity and temperature is not linear. At high humidity levels (condensation risk), relative humidity decreases quickly with small increases of temperature.
As an example, consider an enclosure with a volume of one cubic meter. Assume the air in this enclosure contains 5g of water vapor. At 2°C, the moisture in the air corresponds to 90% relative humidity. Following the constant 5g/m3 absolute humidity line in Figure 4, a relatively small 9°C increase in air temperature results in a reduction of relative humidity from 90% (high risk of condensation) to 50% (low risk of condensation). Because of this relationship, blending a small volume of warm recirculating air, as shown in Figure 2, can have a meaningful effect on reducing the relative humidity of cooler outside intake air.
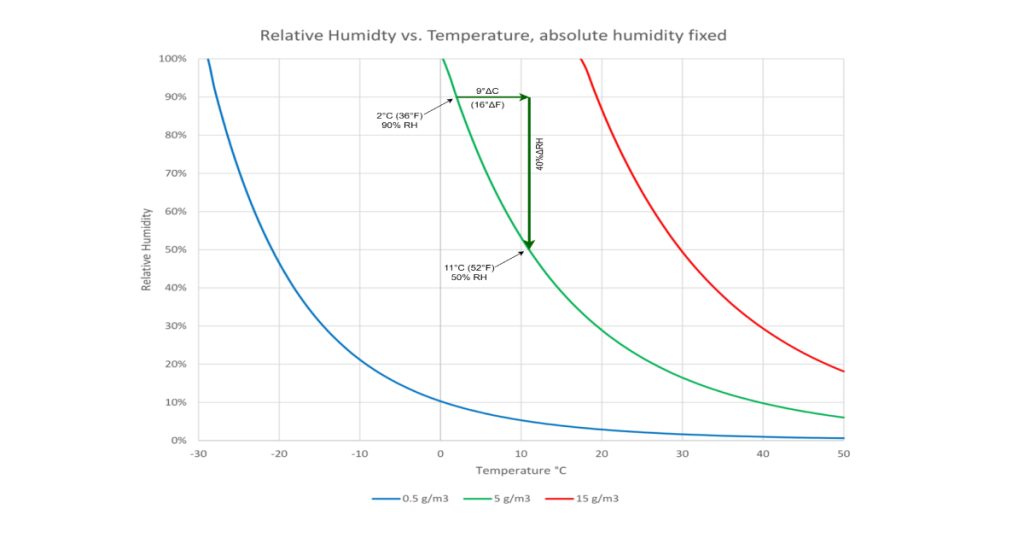
Air Mixing for Electrical Enclosure Designs: Control & Maintenance
The key components of an air mixing solution include air sensors, mechanical damper actuators, fans and heaters. To streamline maintenance and minimize downtime, it is beneficial to incorporate a system dashboard to help operators and technicians quickly visualize system operation and identify any potential concerns. Figure 5 shows an example air-mixing system overview presented on an HMI screen. In this example, each component is represented in its approximate orientation within the machine, with displayed values for each sensor input (temperature and humidity) and each device output (damper position, fan speed, space heater status).
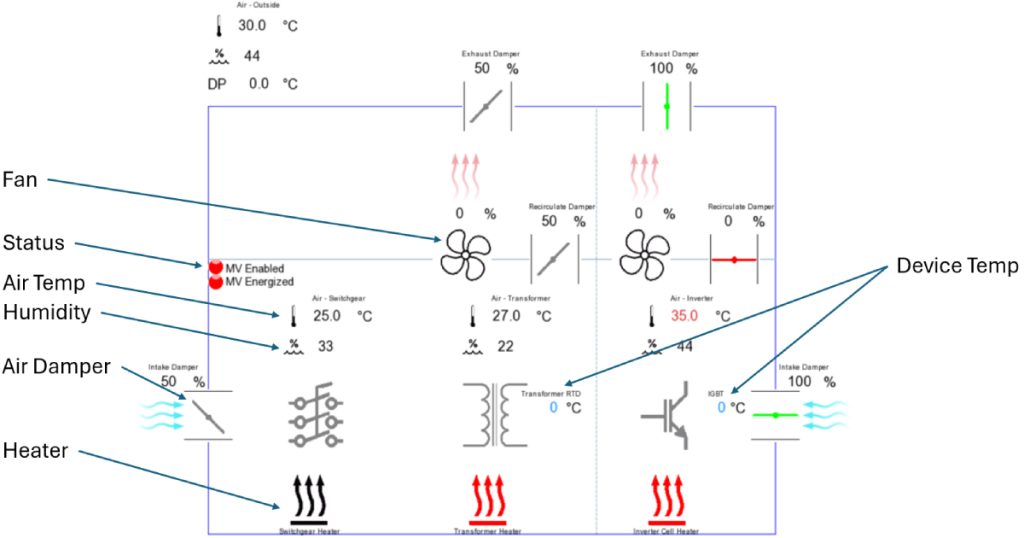
A visual interface allows a technician to quickly identify any operational abnormalities. A visual dashboard is important to understand what is happening, visualization of the control logic function blocks is beneficial to quickly determine why it is happening. Continuing the example from Figure 5, an HMI interface makes it easy for a technician or engineer to dig deeper into the logic driving each state, and visualize the operation sequence using simple logic blocks.
Outdoor Electrical Enclosures: Cost, Reliability Considerations
When specifying high power outdoor electrical equipment, it is important to consider the climate control system architecture and evaluate the cost and reliability trade-offs among different environmental control solutions. The initial cost of purchasing an outdoor drive package with an integral climate control system is often offset by reduced cost and time for field integration and the overall reduction of lifetime operational costs.