How the IIoT Is Delivering on Asset Performance Management, Part 3
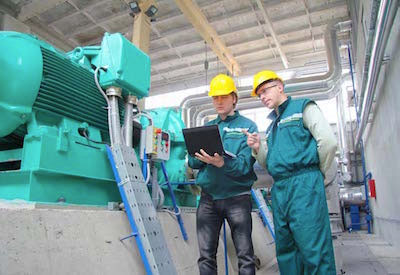
Oct 23, 2017
By John Boville
Part 1 of this 4-part series introduced ways in which increasing digitization might improve plant operations. Part 2: how IIoT can improve the productivity of reactive, preventive, predictive and proactive maintenance. Here in Part 3: five converging trends.
The following five trends are converging around IIoT to help more companies achieve maintenance benefits such as those that Ash Grove Cement Cement, of Overland Park, Kansas has enjoyed. Ash Grove Cement uses Schneider Electric’s Avantis asset management software to automate maintenance data collection at each of its nine facilities. This enabled Ash Grove to reduce its inventory costs by US$2 million in the first year of implementation, while ensuring compliance with the EPA’s Portland Cement Maximum Achievable Control Technology regulation, thereby minimizing the potential loss of US$3 thousand per hour for every hour the kiln is offline.
The five trends are:
1. advances in edge control that enable flexible deployment of control systems with the power and flexibility to handle advanced analytics and the big data needed to support them
2. expanded use of Ethernet connectivity in controls, making it easier to capture and share data and then analyze it with advanced applications
3. deeper cybersecurity protection to leverage the value of open standards that are essential to realizing the full potential of IIoT with less vulnerability to cyber attack
4. advanced object-oriented engineering environment’s simplifying, the deployment of strategic asset management models
5. the evolution of asset management models themselves
The first three trends are evident in the evolution of control technology, in which programmable logic controllers (PLCs) have evolved into more power programmable automation controllers (PACs) capable of implementing preprogrammed application libraries and open, advanced, object-oriented engineering environments. As such, these have gained some market traction, but primarily as low-end alternatives to a distributed control system and addressing multi-asset maintenance challenges. In recent years, PACs have evolved more in the direction of the requirements of the IIoT. For instance, Schneider Electric’s Modicon M580 ePAC has adds more processing capability, Ethernet communications and deeper cybersecurity protection. As an example of the fourth trend the Modicon M580 can be implemented with Schneider Electric’s PES process automation system, which is a single, object-oriented software engineering environment that simplifies configuration of architectures involving numerous field devices, control types and applications.
And the fifth trend is the evolution of asset-centric models, which IIoT is making increasingly valuable for continuous, discrete, and hybrid operations. In an assetcentric model, rather than even trying to build a model for maintaining the entire, constantly growing network of intelligent things, the maintenance engineer develops isolated strategies for individual assets, selected on the basis of their contribution to higher-level business objectives. Unlike a process-oriented model, in which asset management challenges are solved across multiple operating levels, asset-based approaches solve individually at the equipment, unit, area, plant, and enterprise levels. They may, however, exchange data as required with other assets across a common network communications bus. This approach makes it easier to balance asset availability and utilization across the equipment, units, and areas that have the most impact on the business without getting bogged down in trying to optimize maintenance for the entire enterprise.
Part 4 will explore how IIoT is already improving operational profitability. Read Part 1 and Part 2.
John Boville is a marketing manager for Schneider Electric’s marketing and innovation group, where he focuses on the Modicon controller line. He has been with Schneider Electric industrial automation for more than 25 years, including implementing market segment strategies for the automotive industry. Prior to joining Modicon, before it became part of Schneider Electric, he served for 12 years in project engineering for CEGELEC Automation as an industrial system designer, installation specialist, and project leader for large automation migration projects. He holds a B.S. in electrical engineering from the University of Bradford, U.K. Keep up with John’s latest insight in his blog: http://blog.schneider-electric.com/author/jboville/
Photo source: Schneider.