Automation at the End of the Production Line: Packaging and Palletizing
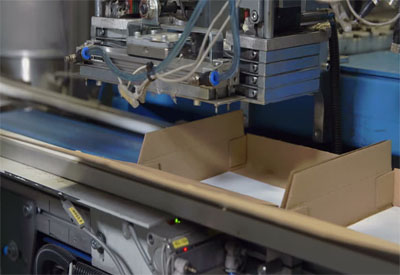
November 7, 2017
By: Owen Hurst
Packaging and palletizing has become a large part of the control and automation industry, particularly in general manufacturing and the food and beverage industry. This is not surprising as automation of packaging and palletizing can reduce labour costs and save time while increasing productivity. Further, and particular to the food and beverage industry, automation ensures safe and uncontaminated packaging and as we will see can cut costs in other areas of the production process through system integration.
Packaging can be argued to have been around for centuries. The ancient Greeks built specialized amphorae (jars) to transport oil that could be safely packed in ships for overseas voyages, and the Romans had an intricate supply network for the import and export of goods that required safe packaging for the long and often arduous journeys. However, packaging as we tend to see it today truly took off in the post-war years. It had been a frustrating fact during the war that much needed supplies often reached troops only to be found contaminated or unusable because of poor packaging. It was in these post-war years that packaging truly became “an integral part of the whole production process, being the final link in a long chain which probably started with the engineer’s drawing board.”[1]
The automation of packaging and palletizing today is diverse and present in many production and manufacturing facilities and thus here we shall look at a brief sampling of the modern applications to gain a broad view of the implications of automating at the end of the production line.
There are a number of challenges facing the automation of packaging born primarily from the wide range of shapes and sizes of packaging necessary to seal and ship merchandise. We turn first to a case study by Rockwell Automation on a canning facility that recently upgraded its automation infrastructure including system integration that tied together the various processes on the production line. The new control system even operated a heat and energy recovery system that uses the can-cooling process heat to warm city water for the soaking, blanching and cooking procedures. The new system further cut down on natural gas usage by 38.2% and recycled water within the plant has cut down on the company’s water usage by more than 100 million gallons each year.[2] The implementation of an automated system for canning goods prior to cooking, in this case for canned meat, meant a higher production rate and decrease in labour and overall costs. The canning also allowed the production line as whole to operate more efficiently, as the pre-canned goods were already individually packaged and could flow seamlessly into the final packaging stage.
The canning process in the food and beverage industry can certainly be more involved than other industries, particularly as the product package can play a role in the preparation process, as in the above-mentioned study. Or in other cases the initial packaging is more delicate, like with fruits and vegetables.
Top seal packaging has become increasingly popular, particularly with fresh produce growers and packers. A case study by Crawford Packaging demonstrates how the use of an automated top seal packaging solution improved substantially on the current packaging system that had been in use by a produce grower and packager. The implementation of the automated top-seal machine reduced packaging material consumption and was able to offer a new popular, eco-friendly package. A valuable part of the process was having a packaging specialist study the clients’ needs and consult on the best automated packaging system to meet their needs.
In another case study by Crawford Packaging the effectiveness of the first semi-automatic water-activated tape sealer that was deployed in Canada is discussed. In this instance the customer required a reinforced water-activated tape seal that would ensure packaging held in winter conditions. Again, a specialist was brought in to assess the available facilities, labour and production levels. The company also required an implementation that would not affect business (ie. Labour force, safety, operation hours). In this instance the specialist identified the solution was to implement an IPG WAT sealer. IPG is one of Canada’s leading water-activated tape manufacturers. The implementation of the new system was able to the job that had previously been accomplished by four tape sealers and resulted in a reduction of overall costs, increase productivity, reduced labour and increased throughput.
Now that we have briefly identified how effective proper utilization of automation can be for packaging we can go further and consider how automation is not only reducing costs but is finding new ways to solve standard packing issues. When it comes to the final packing stage the primary problem is sizing the right boxes to fit the content being shipped in order to reduce shipping air or void fill such as paper or bubble wrap.
Automation can provide a solution to this issue, and we can see it already in system such as the Linkx Packaging Systems Ltd solution from Rockwell Automation’s Intelligent Box Sizer. The Box Sizer provides an innovative means for packaging product, particularly for e-commerce companies through a decrease in packaging waste, packing costs and haulage costs. It is especially interesting for companies that ship a wide variety of product types and sizes because it can adapt random box sizes to accurately represent the contents.
The system incorporates automation, motion and safety infrastructure from Rockwell Automation as well as an Allen Bradley CompactLogix programmable automation controller that communicates using EtherNet/IP with up to 17 motion axes controlled by Allen Bradley Kineticx 5500 servo drives.[3] The system is capable of measuring “the empty volume of a loaded box and then adjust itself to cut, crease and fold the box to suit the volume of the goods within.”[4]
Not only is the system ensuring goods are packed as efficiently as possible, but the system takes into consideration operator safety by implementing Allen Bradley Guardmaster safety products. The Linkx system is truly an innovative approach to packaging that has the advantage of cost saving and a decrease in material waste for the packager and distributor.
We also need to consider the final step in packaging, the palletizing of packaged product, which has traditionally been a labour intensive and time-consuming practice. A great example of the implementation of automated palletizing is seen in a case study by ABB that looks at the palletizing challenges and solution for the Great Canadian Bean Company in London, Ontario.
Before automating the palletizing process was taking a physical toll on employees that were prone to injury from lifting heavy bags of beans and was limiting the company’s ability to meet increased production requirements. Bill Maclean, Owner and President noted that “we were assigning multiple workers to palletize the bags, including one operator to fill and sew the bags and two to four operators to load the full bags onto pallets.”[5]
The company then reached out to the Automation Project Group who worked with ABB to install an IRB 640 palletizing robot that utilizes a user-friendly interface and allows the company to easily reconfigure pallet patterns. Furthermore, the system was implemented within the existing packing line to work seamlessly alongside the manual workforce.
The benefits for the Great Canadian Bean Company were immediate, with workplace injuries from heavy lifting dropping to zero and a complete reduction in damage to the product within the plant and during shipping as pallets were packed to precise configurations designed for overseas shipping.
The implementation of automated packaging and palletizing systems proved beneficial across all the above case studies, and in general has had a positive effect on industry through the decrease of labour and accompanying injury, a rise in production rates and overall company efficiency. With automation on the rise we will see continued increase in automaton within the sector and as a result the advancement of productivity rates and a skilled workforce capable of implementing the increased desire for control and automation systems at the end of the production line.
Palletizing image source: https://www.youtube.com/watch?v=p0TXgrp19mE
Packaging image source: https://www.shutterstock.com/video/clip-1943341-stock-footage-robot-works-with-iron-sheet-at-the-factory.html
Endnotes:
[1] Harrison, p.822
[2] Intelligent Ingredients, p.11
[3] Intelligent Packing Machine Set to Revolutionise eCommerce Logistics, p.2
[4] ibid
[5] Bottom Line Bossted for Beans, p.1
Sources:
Harrison V.G.W. “Techical Advacnes in Packaging,” in Journal of the Royal Society of the Arts 109 (5063) (1961), pp.821-839
Crawford Packaging, How Crawford Packaging Brought the First Packaging Automation Tray Sealer to North America, https://crawfordpackaging.com/case-studies/top-seal-packaging
Crawford Packaging, Canada’s First Semi-Automatic Water-Activated Tape Sealer, https://crawfordpackaging.com/case-studies/water-activated-tape-case-sealer
Rockwell Automation, Intelligent Packaging Machine Set to Revolutionise eCommerce Logistics, https://www.rockwellautomation.com/en_ZA/news/case-studies/detail.page?pagetitle=Intelligent-Packaging-Machine-Set-to-Revolutionise-eCommerce-Logistics-%7C-Case-Study&content_type=casestudy&docid=cb0375595da5a1c7a7c7023a963ca8ff
Rockwell Automation, Intelligent Ingredients, http://literature.rockwellautomation.com/idc/groups/literature/documents/sp/food-sp025_-en-p.pdf
ABB, Bottom Line Boosted for Beans, http://www.abb.com/References/Default.aspx?db=db/db0003/db001466.nsf&c=63953a511b5657c8c1257348002efca8
Owen Hurst is Managing Editor of Panel Builder & Systems Integrator.