Flexible, Compatible, Rugged Plastic Plug-In Connector HEAVYCON EVO
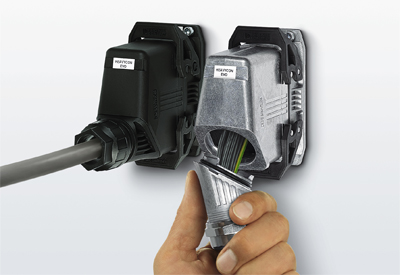
{videobox}https://youtu.be/0FCPDY1VXTo {/videobox}
Read the full brochure here
The development of plastic plug-in connector housings has created an effective alternative to standard aluminum housings. The new heavy-duty Heavycon Eco connectors from Phoenix Contact are not only more cost-effective than the metal version they are modeled after, but they also offer additional advantages thanks to their plastic construction.
“If you have a choice between plastic and steel, choose steel.” For years, this saying reflected the conventional wisdom. However, modern plastics have long been a viable substitute for metal, as evidenced by today’s power drill housings, garden furniture, sports equipment, or Tupperware. This is because plastic is lightweight, easily molded, and does not rust. Modern industrial plastics are also extremely rugged and durable.
Angled bayonet connection
Industrial plug connectors made of die-cast aluminum are another example: For decades, hardly anybody dared to doubt their material properties. But here, too, new possibilities have emerged thanks to new high-performance plastics and computer-aided design.
For example, the fully compatible Heavycon Evo range of housings includes a variety of cable glands with an angled bayonet connection. With a simple 45° turn, the cable glands can be easily installed by hand, either horizontally or vertically, on the sleeve housing. In this way, the cable outlet guides on the plug can also be adjusted on site to meet specific installation requirements. Since all housings in sizes HC-B 6 to HC-B 24 use the same bayonet connection, M20 to M40 screws can now be freely combined with sleeve and coupling housings. This adds flexibility and minimizes the number of product versions required.
The large opening in the housing with the bayonet connection offers yet another advantage for the user. Thick and rigid cables are easier to insert because the cable gland is simply installed horizontally or vertically at the very end of the assembly process. As a result, instead of having to bend the entire cable during assembly, only the conductors in the plug-in connector housing have to be bent.
Fully compatible
The inside of the plastic housings feature patented metal inlays that ensure that the standard fixed and module contact inserts are securely fastened. In this way, requirements for the leading PE contact, which are also prescribed by industry standards, are also met, and the plastic housings can be freely combined with counterparts made out of die-cast aluminum. The panel mounting and base housings also fit standard panel dimensions and wall cutouts. They also prevent the ingress of dust and liquids in accordance with the requirements of protection rating IP65/66.
Stability of aluminum housings
In extensive laboratory tests, the industrial plug-in connectors often far exceeded the requirements defined in standards. In the field, industrial plug-in connectors are often exposed to extremely harsh operating conditions and environments. They can also be damaged, for example, if the connector and the cable fall from a great height, if they are exposed to heavy knocks during relocation or shipment, or if the cable is snagged when they are plugged in. Sometimes, plug-in connectors are even repurposed and used as steps for accessing hard-to-reach areas.
Heavy temperature fluctuations, aggressive substances, dust and water, vibrations, and UV rays are other factors that can have a negative impact. All of these environmental influences were simulated in extensive laboratory tests. These tests showed that modern plastics, with all their impact strength, match up to their die-cast aluminum predecessors in every way.
However, even plastic housings reach their limits in certain situations, such as EMC applications in which they have to provide electromagnetic shielding for cables and housings, or in applications where temperatures fall below -40 °C or exceed 100 °C. In these scenarios, metal plug-in connector housings are still an excellent choice. Nevertheless, for the great majority of applications, nothing stands in the way of using plastic plug-in connectors. This includes outdoor applications, where black plastics, which absorb UV rays more easily, have proven reliable for years. Side-view mirrors, bumpers, or hub caps are good examples from the automotive industry. The well-known red and blue CEE connectors, which perform reliably for many years even under extremely tough conditions, are also made of plastic.
70 percent fewer varieties
Thanks to the slanted bayonet cable inlet, the need for different product varieties can be eliminated. For example, with a sleeve housing, which is available with two straight and two lateral cable outlets and four screw sizes of M20, M25, M32, and M40, one housing can replace eight varieties. One Heavycon Evo coupling housing replaces four aluminum housings. With base housings, 50 percent fewer versions are required, as the need for models with two cable inlets is eliminated. The second cable inlet can be created by simply prying out a cap during installation. Furthermore, all brackets and protective covers can be mounted in just a few simple steps, making overall installation even easier. Panel mounting bases are the only type that cannot be substituted as they do not have cable inlets. Still, when these savings are added up, 70 percent fewer versions are required if the entire range of housings is used. The philosophy of ‘less is more’ applies here. This starts with less engineering work, then less data maintenance, fewer systems involved in the production process, less ordering for the Purchasing department because large quantities of the same parts are ordered, less capital tied up in the manufacturer’s warehouse, as well as less capital commitment for the retailer and the end user. And the fewer components a system has, the less it costs to make it available worldwide.
New milestone in the evolution of plug-in connectors
Plastic plug-in connectors are an effective alternative to metal plugs in many situations. However, it is essential to select the right types of plastic and ensure that components are sized to meet specific application requirements. In addition, full compatibility of all system components will make it easier to use existing solutions. It also goes without saying that all safety requirements must be met. Phoenix Contact’s Heavycon Evo plastic plug connectors are not only more cost-effective than aluminum housings, they also offer logistical advantages and, thanks to their adjustable cable outlet guides, greater flexibility at the installation site.
Read the full brochure here
For more information on the product Phoenix Contact’s heavy Duty Connectors visit their website