Discussing Nivek Automatisation with President Kevin Dufresne
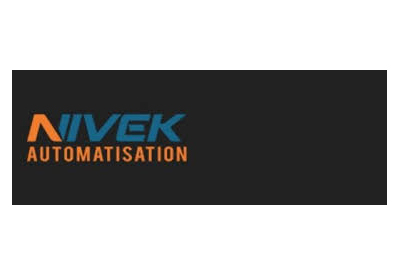
March 27, 2018
Nivek Automatisation is a forward-thinking company focused on providing advanced solutions that deliver premium performance and flexibility of use. Working across a variety of industries such as Water Management, Wood Processing, Food, Industrial Process, Manufacturing and Minerals Nivek works to provide optimal service. Located in Saint-Cesaire Quebec Nivek is a growing company that is and will continue to provide control and automation solutions in an industry that show no sign of slowing.
Panel Builder & Systems Integrator caught up with Kevin Dufresne, Founder and President of Nivek to ask him about his company and thoughts on the future of the automation and control industry.
1) Give me a little history on Nivek Automatisation?
Nivek was founded in August 2014 by current company President Kevin Dufresne. With solid knowledge in the field of automation and industry. The company has quickly become more than just a test for its owner. Nivek tries to innovate with its solutions offered and not its services.
2) How has client demand changed over the last 5 years and how does Nivek work to stay on top of those changing demands?
The customer wants the best possible service, but also requires confidence in the company that works in it’s facilities. Nivek is always looking for an innovative and advantageous solution. Being on the lookout for new products that could have real benefits in the installation of our customers is one of Nivek’s strengths. We always work in the perspective of developing long lasting business relationships.
3) I see you are involved in ensuring your employees remain up-to-date with new technology?
Training for employers is obvious to us. An employee with more knowledge allows the evolution of the company for which he or she works. We are now a certified solution partner with the Phoenix Contact, which allows us to have better knowledge the integration of their innovative products.
4) Give a little detail about yourself as the President and background?
I now have more than 18 years of experience as a project technician. From an early age I have always been interested in understanding industrial processes. Which led me to do my studies in industrial automation.
5) In the kit I have it states you have ‘a solid commitment to the Industry 4.0 concept’, could you elaborate on this?
The 4.0 concept is a new era for technology. The integration of this concept can be seen in different ways, it is very interesting to see the complete factories, but this is not the reality for our customers. We rather integrate solutions that allow us to follow the traceability of products, or to collect data to optimize the production cycle. For us the concept 4.0 is done by the simple modification to the equipment already in place. It’s for everyone to be in the age of industry 4.0
6) Could you highlight one or two of your more recent projects? What the project entailed, how it was approached and the end result.
Project: Mill Automation -optimization of the process from the receipt of raw material to the shipment of products for animal consumption.
– From relay logic to the installation of automata Phoenix Contact brands.
-Implementation of a planning and control process management software.
Project Echelener over a period of two years, since the work was to be done in full operation of milling. No stop more than 48 hours.
Some numbers:
-2300 IO input / out put
-138 entry and exit security
-213 engines
-5 production control positions
– 72 network equipment
– Now over 900 production orders per week
– Manufacture of 650 tons of molded animals per week
The challenge was to make safe and easy management of 1200 different recipes while thinking about production accounting.
Phoenix Contact brand automation products allowed us to build a reliable project. Our client is now in full control of his production. the use of the MJ system software has made it possible to offer a unique forward-thinking solution on the market. A big project has the competence of our team.
7) How has your relationship with Phoenix Contact helped to advance Nivek?
The partnership between Nivek and Phoenix Contact contributes to the value that Nivek wishes expressed. Phoenix Contact is a company that has been innovating for several decades. This is an inspiring company.
8) What do you see in the future for Nivek?
We will always be on the lookout for projects that will put forward an innovation solution. We want to build a company that will be recognized for its audacity in the integration of system, for its skills and especially want to be a flagship company in the field of automation.
9) What do you see in the future for automation in Canada?
There is no doubt that the Canadian industries will see their installations become more and more automated in order to remain competitive with other global markets. Without further converting their factories, they will have to go to the Smart Factory by modifying existing equipment. To better meet the more specific market demand