Modernizing a Network Infrastructure to Achieve Better Visibility and Improved Device Management
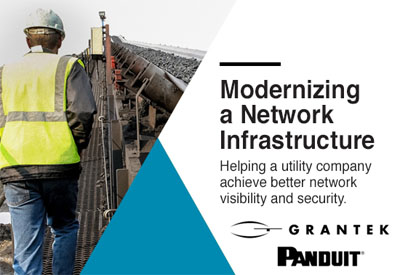
Modernizing a Network Infrastructure to Achieve Better Visibility and Improved Device Management
Panduit’s ecosystem helps a utility company achieve better network visibility and security for its material handling buildings
CHALLENGES
The massive coal generation power plant at a major utility company spans across approximately 20 acres. Located along a large river, the plant receives the coal and limestone by boat and transports it to storage and then to generation on a complex material handling conveyor system.
The material handling conveyor system covers over 5000 feet between the ship unloader and the generation station through over five transfer buildings and multiple storage and material handling buildings. Distributed I/O along this network of conveyors offload, store, and deliver this fuel to the burning units where power is produced.
The material handling process also brings the ash generated by the burning process to four massive silos where the ash is removed and transported by rail for recycling.
Relying on 20-year old Allen-Bradley PLC-5 controllers, the legacy system was technologically outdated. The ControlNet™ network, and coaxial cable limited the customer’s ability to scale, manage the network, and integrate new automation equipment. As a result, the customer determined that its existing network infrastructure proved inadequate for PLC migrations and other upgrades planned for the following fiscal year. It decided to modernize its network infrastructure in parallel with the PLC system to provide a purpose-built, robust, scalable solution.
In addition, the limited performance of its existing conventional copper networks forced controls engineers to continuously add new network segments and network equipment to provide connectivity across the site, which led to unmanaged network sprawl and bottle necks. To ease this problem the customer wanted to design a fiber optic network, which would provide the capability to scale and manage active hardware, increase visibility, and provide more security. Moreover, the customer wanted to reduce mean time to resolution throughout its material handling buildings.
With Rockwell Automation urging its PLC-5 clients to upgrade their systems because they were phasing out their support of that platform, the customer set project completion to occur during the same fiscal year as the PLC migration. Furthermore, the customer required a 25-year network infrastructure warranty to ensure durable system performance.
The revamp would include a modernized control network and an Ethernet-based infrastructure with copper and fiber optic connectivity. The network infrastructure needed to be highly manageable to reduce mean time to resolution of issues and for better problem identification as challenges occur. Finally, the customer needed a solutions provider that could identify and recommend project management best practices to maintain a competitive edge through proven expertise.
PANDUIT & GRANTEK SOLUTION
Panduit Professional Services assessed the customer’s physical network and engaged Grantek Systems Integration to partner on the opportunity. Grantek, a Panduit OneSM Gold Partner, performed a logical assessment and provided logical network design, access layer mapping, and project management services. Grantek also coordinated with the PLC upgrade team to schedule and execute migrations. In addition, Grantek provided training services to onsite staff and guided the team on best practices for laying out the control integration and managing and scaling the network. Panduit OneSM Certified Partner Oreair Electric installed the new singlemode fiber optic backbone according to TIA standards and Panduit’s recommended installation guidelines and best practices.
Design
Panduit Professional Services provided the customer with a Construction Documents (CD) package and Construction Administration (CA) Services. The CD has the complete design plans and a set of written installation specifications for all cabling, connectivity, and cabinets/enclosures.
The CD also contains AutoCAD drawings to ensure proper installation. Panduit Professional Services completed this service under contract to its distribution partner, Englewood Electric Supply Company, (EESCO) Distribution, Inc.
Grantek provided the customer with logical network and cybersecurity services to design the ICS network. The design documentation detailed the network architecture, IP/VLAN details, firewall rules, switch bill of material, and access layer map. Grantek also performed in-house configuration and testing of the network switches prior to delivery to ensure a rapid deployment during commissioning.
Implementation
The complete Panduit solution upgraded the physical network from Layer 1 to Layer 3 and comprises the Pre-Configured Industrial Distribution Frame (IDF), Integrated Network Zone System, fiber and copper connectivity, and fiber distribution enclosures.
The Integrated Network Zone System supports the demands of real-time control and data collection and helps ensure the industrial networks and control systems operate at a sufficient performance margin within the specified environmental conditions. It uses an Allen-Bradley® Stratix™ Industrial Ethernet switch to enable speed to deployment, which meets the customer’s requirement for a scalable, standardized solution. It also contains a battery-free, Ethernet-enabled Uninterruptible Power Supply (UPS) to reduce maintenance and ensure maximum switch uptime.
Configured prior to shipment, upon arrival each Integrated Network Zone System was mounted, and fiber and copper connectivity were installed to the new PLC end points. Panduit Professional Services designed the fiber optic network topology and specified the routes and pathways. The Integrated Network Zone Systems were deployed throughout four transfer buildings and process areas to ensure the customer’s industrial network provided adequate coverage.
Industrial Distribution Frames (IDFs) were used in two transfer buildings with the core IDF in the Main MCC building for quick deployment and protection of the customer’s Ethernet switches. These switches serve as the network distribution layer and a fiber aggregation area, which reduced the quantity of fiber optic cable needed. The IDFs also protect the Cisco switches as part of the network core. Panduit’s fusion splice tray solution was used in the IDFs and the HD Flex™ fusion splice solution was implemented in every zone enclosure.
Tested and thermally verified by Panduit Laboratories, the IDF achieves 25% faster installation than a non-pre-configured IDF installation. The additional back-end space allows for 3X the cooling capacity over typical deployments for increased reliability.
A telecommunications grounding and bonding system was implemented to TIA standards and NFPA/NEC code to reduce intermittent failures and personnel hazards. Visually verifiable connections and dedicated grounding paths help maintain the customer’s system performance and protect equipment.
Oreair Electric installed OS2 singlemode fiber optic cabling to comprise the backbone of the industrial network. Category 6A, F/UTP shielded copper cable was installed to meet current environmental requirements and future performance needs.
Grantek provided onsite testing, debugging, and start-up support. Following implementation, Grantek provided training sessions and documentation to technicians.
PARTNER ECOSYSTEM
The customer’s Industrial Automation team was short staffed and did not have the bandwidth, expertise, or time to manage the project. To accommodate the customer’s needs, Grantek held a kick-off meeting to align Panduit, EESCO, and Oreair Electric to identify and resolve gaps in the project scope. Also, Grantek, under contract to EESCO, helped guide the PLC migration team and provided training services to the customer’s preferred integrators for controller migration. The collaborative efforts ensured that the customer received what it needed during each project phase.
Initially, the customer lacked a budget for this project, so Panduit provided a Front-End Engineering and Design (FEED) study before the full design. Panduit then walked through the customer’s needs and created a high-level design for installation budgetary estimates. To provide further help, Grantek developed a proposal for project management, logical development, commissioning, and scheduling services. Showcasing its position as a thought leader in the industry, Grantek also provided expertise through programming, configuration, and documentation of network equipment.
A Panduit Professional Services solutions architect visited the site before, during, and after the installation to inspect the work. This ensured the system was installed in strict accordance with the CDs and all previously stated industry standards and best practices.
Oreair Electric handled the electrical and communication cable installation and submitted the 25-year Panduit Industrial Automation Certification PlusSM System Warranty.
Panduit, Grantek, EESCO, and Oreair Electric collectively demonstrated the strength of the partner ecosystem. From design to project management to installation, the partners came together to provide the customer with the turnkey solution it required within a tight timeframe. Each partner played a significant role that allowed the overall project to flow seamlessly and to the complete satisfaction of the customer.
BUSINESS BENEFITS
The customer now has access to all material handling controls devices on a single, secure Ethernet network. This enables better monitoring and access along with improved historical data collection and device management. In addition, the customer’s corporate physical infrastructure connectivity between operation systems and enterprise systems follows the CPwE model for industrial networking. The upgraded network infrastructure allows the customer to better identify problems when they occur, and the 25-year warranty assures the customer that the new installation meets performance expectations and future networking needs.
For more information from Panduit see: https://pages.panduit.com/CaseStudy_Coal_Open.html
For more information from Grantek see: https://grantek.com/case-study/modernizing-a-network-infrastructure/