Connectors Outperform Hardwiring for Manufacturers and their Customers
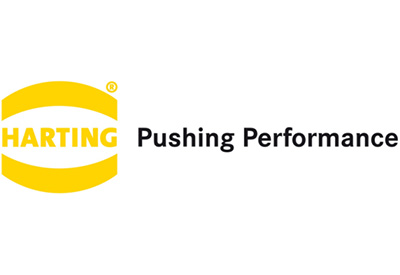
October 28, 2018
Industrial connectors or hardwiring? More and more machine builders comparing the cost of using both wiring approaches in their operations find connectors more economical and practical.
Benefits of connectors compel many to switch
Many thousands of equipment manufacturers have switched from point-to-point (hard) wiring to connector-based cable assemblies in factory and process automation and control systems. Adopting progressive connectivity solutions has improved their unit costs and productivity. It allows them to turn around orders and complete installations much faster. With margins under increasing pressure, many OEMs have come to regard these benefits as a must-have. For many of their customers, the principal argument for connector-based wiring over hardwiring – a lower total cost of ownership over the service life of the machine – is equally compelling.
Today’s connector lineup includes more user-friendly and application-specific choices that can
further options. Most rectangular connectors are modular and user-configurable. Using different inserts, each can be configured for different voltages for example, signal and power, enhance reliability and convenience. Connectors offer excellent mechanical stability and are available with high ingress, temperature and vibration resistance, harsh weather durability and multiple termination or combinations of different transmission media: power, signal, fiber optic, coax, D-Sub and pneumatic. Recent innovations like quick-lock termination, click-and-mate assembly and twist-top locking make installation and maintenance faster and simpler than ever
Most industrial equipment, for indoor or outdoor use, contains extensive electrical wiring between its components and subsystems. When the equipment is manufactured, the machine builder (OEM) typically assembles and tests it at the plant, disassembles it for shipping and reassembles it at the customer’s location. With hardwiring, this means each connection – often there are hundreds – has to be individually unmade for shipping and then remade when setting up at the customer. That’s labor intensive. If wiring errors are made during this final setup, and it happens frequently, they can cause equipment damage upon startup or, at a minimum, further delays and considerable additional expense to diagnose and correct.
Using connectors makes the wiring for the same machine a pre-engineered job that can be designed, assembled and tested as a harness and then quickly integrated into a machine or system as it takes shape. Some time is invested in assembling the harness, but then installation only takes a fraction of the time hardwiring requires. The risk of wiring errors is virtually eliminated. That’s why hardwiring has a dwindling appeal, increasingly limited to production where substantially all connections are made just once, at the factory, with little or no field assembly required.
Connectorization means flexibility, cost savings
Even in those circumstances, connectors make a strong business case. Connector-based wiring provides advantages over hardwiring at every stage of the product life cycle.
Connectorized wiring is almost perfectly complementary with the continuing shift to modular machine design. Modularization, where machines and plant systems are comprised of inter-related functional modules, offers significant efficiencies and economies over the traditional unitary design approach. Standard components such as control panels, motor assemblies and power distribution boxes can be pre-built, pre-tested then plugged together in final assembly with connectors. This example demonstrates how modular design and connectors combine to make a product better for both the OEM and the user: A French builder of large industrial ink-jet printing machines increased its market share while lowering production costs by adopting a modular design employing connectors in place of hardwiring. Each machine has a print head and control unit. Previously, fiber-optic cables, pneumatic hoses and electrical cabling were run through sheathing and hardwired to the print head and other processes like the ink dispenser. However, disengaging the print head always was a major undertaking. By integrating all these feeds in a modular connector, the print head now can be detached and reattached quickly for faster assembly and maintenance. A custom, ready-to-use cable harness is supplied by HARTING, the connector manufacturer, for assembly between the print head and the control unit. The same advantages apply to a connectorized plant layout. Most plant engineers are well-versed about using a communication bus with drops coming off a main trunk cable. Power and control signals for motors can be distributed the same
way using connectors like HARTING’s Han-Power® T. Installing or replacing a motor becomes a plug-and-play operation, with little downtime or risk of wiring errors.
Savings on the production floor and beyond
Pre-making connectorized wiring assemblies allows for precise, repeatable measurement of cable lengths. Connector-based wiring harnesses can be assembled by lower paid staff or a contractor rather than by an electrician for additional cost savings. With installation, they require little if any of the rigid or semi-rigid conduits that protect point-to-point wiring from damage that would require extensive re-wiring. Since power and signal needs often vary within a machine, a single connector can be configured to accommodate different DC voltages or both AC and DC power. The alternatives, like mounting multiple terminal blocks inside a control cabinet, require additional labor and materials and take up more space.
Another example of a labor-saving possibilities: HARTING’s Han-Yellock® connector only requires male crimp contacts. The electrical feed per wire can supply up to five contacts by using a multiplier insert inside the connector. This enables the connector to perform the multiplier function previously done by terminal blocks inside the machine. The Han-Yellock® housing can be populated from either side, so the entire connector interface – hood and housing – can be mounted from the outside once the machine is fully built, again, a job for an installer rather than an electrician. (Han-Yellock® boasts a vibration-resistant, latched locking mechanism – the yellow press button that gives it its name – that engages and disengages with a twist of that button.)
With modular design and connector-based wiring, the machine can be shipped to the customer in smaller pieces, reducing transportation costs and the risk of damage. Faster field assembly with much less risk of wiring errors translates into major cost savings for the OEM. Troubleshooting and maintenance are similarly accelerated. During the warranty period, that’s a cost benefit to the OEM and a benefit to the end user in the form of reduced downtime during scheduled and unscheduled maintenance. After the warranty period, the entire benefit accrues to the end user, the major reason why connectors assure a lower total cost of ownership than hardwiring. Many progressive machine builders see that lower lifetime cost as a unique selling point to differentiate themselves from competitors and maintain customer satisfaction (and loyalty) over the years.
Hardwiring: the cost myth
Given these advantages, why do some OEMs still hardwire? For some, the thought of making a significant change in their manufacturing processes is daunting. Others may not fully appreciate the cost of assembling a hardwired system in the field. They say connectors are an additional item on the Bill of Materials and their customers buy solely on the basis of the lowest sticker price.
Yet most OEMs that compare their use of hardwiring and connectors find connectors save them time and money, particularly when the full cost of making hardwired connections is recognized. Unlike connector-based wiring where most of the attributable costs are incurred once, up front, the costs associated with hardwiring are recurrent and often unpredictable because of the possibility of wiring errors. Each manufacturer has different labor and overhead costs, but a time study done by one company determined its fully allocated cost for hardwiring each pair of connection points on a complex piece of equipment was about $80 – if done in-house. Experience shows that whatever a company’s costs for hard-wiring in-house, there is about a 30% premium doing such connections in the field, for installations or for warranty service and repairs.
Many OEMs echo what these North American companies found in switching to connectors:
- A manufacturer of paper conveyors for commercial printing presses had been hardwiring over 200 wires to the control box of each unit prior to final testing. This process could take up to four work days per unit. Switching to six modular connector assemblies in a plug-and-play solution reduced that by as much as 2½ days. The connectors cost $1,400 per unit, but the savings of $3,500 in labor and time costs enabled them to increase their production rate.
- The manufacturer of large, material handling cranes takes each one apart for shipment to the customer where it is reassembled. Transitioning from hardwiring to hybrid connectors cut field installation time from weeks to a mere 3-4 hours. Through the initial setup in the field, the manufacturer calculated its all-in cost using connectors was, on average, $622 less ($12,540 for connector-based wiring, $13,162 for hardwiring). However, when hardwiring errors happened during installation, the cost doubled to $26,325, for total savings using connectors of about $13,000.
- A builder of large, automated, precision-welding machines was hardwiring over 300 contacts per unit. It took a week to build and test one, then several days to dismantle it and another week to re-assemble it at the customer’s location. Switching to pluggable connectors cut wiring time dramatically, saving extensively on labor cost. Now, each step that used to take a full week is being done in less than a day.
- A producer of conveyor systems for the food and beverage sector needed to design an IP67-compliant product that could withstand harsh conditions like immersion in wash-down situations. Adopting a connector-based assembly with Han-Yellock® modular connectors in place of hardwiring allowed them to reduce install time and maintenance downtime and increase the throughput of the conveyor by 15%, with cost savings going directly to their bottom line.
- The maker of acoustic microscopes for analyzing the integrity of semi-conductors was planning a new model requiring 120 leads of varying voltages. The goal was a machine with a small footprint, but engineers ran out of interior space for such an elaborate power distribution. By switching to two heavy duty connectors with 60 pins each, they were able to streamline interior wiring achieving the desired footprint and capturing cost savings; internal wiring bundles were eliminated and less metal paneling was required.
Similar stories are told by makers of boats, robot manufacturers wind turbines, stage equipment, casting machinery, packaging and forming equipment and many more. Any company using hardwiring in manufacturing or upgrading equipment is a candidate to save money and time, improve efficiency and customer satisfaction by adding connectors at appropriate locations on wiring and cable runs.
Right connector for each application, budget
Today’s connector portfolio offers users unrivaled flexibility. Connectors are available in different sizes, made from a range of coated and uncoated metals and plastics, with different cable entry angles and termination technologies. There are models created for specific design objectives, such as slim models to fit compact units or tight spaces. Many rectangular connectors offer simple termination options that can be performed quickly, easily and safely by installers rather than electricians, using common tools like a screw driver.
Usually, there are multiple suitable options for each job, allowing the OEM to determine the appropriate combination of capability, convenience and price – even aesthetics.
HARTING invented and popularized the rectangular connector in
the 1950s and is the leading global supplier of heavy duty industrial connectors. Rectangular and square connectors are more readily scalable, configurable and customizable than round ones.
Modularity provides great flexibility
Among its many innovations in connector design and termination technologies, HARTING introduced the concept of user-defined modularity with its Han-Modular® system that allows each customer to build a custom connector with standard catalog components. With over 40 inserts to choose from, Han-Modular® caters to the creation modular machine designs. These inserts are designed not only to carry specific power, signal or data loads and other transmission media including fiber optic, D-Sub, coax signals and pneumatics, but also to withstand challenging ambient conditions like dirt, dust, humidity, large temperature swings, sunlight, tension and vibration. Modules can integrate currents from a few milliamps to 200 A, voltages up to 5,000 V, pneumatic hosing, data lines, shielded bus signals and optical cables made of POF or glass fiber. This user-defined modularity, the essence of flexibility, is available with many HARTING hood and housing lines.
More and more connectors are being designed for special situations. These are based on standard connector products, optimized for particular demanding operating conditions or requirements, harsh weather, extreme heat or corrosive environments, high load applications or where high EMC protection is required. There are models enhanced for high mating cycles in prototyping and testing scenarios, as well as stainless steel ones for hygienic applications like food or pharmaceutical production. These and other specialty versions come in standard sizes, and can generally replace standard connectors without modifications to the design of the machine.
HARTING has based its leadership on developing new connector concepts and adapting existing ones to more precisely meet the evolving needs of its customer base. Choosing the right connector solution for the job will optimize the benefits of connectorization, improving the OEM’s margins while giving end users the lowest possible cost of ownership and greater peace of mind.
For more information http://www.harting.ca/news/white-papers/connectors-outperform-hardwiring/