Boost Your Material Handling ROI via Reliable Wireless Communications
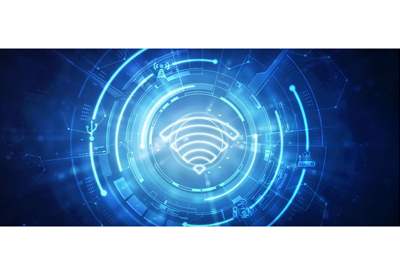
September 24, 2018
By Keith Blodorn, ProSoft Technology
In many manufacturing facilities, material handling functions from parts delivery to weighing to inventory have been automated in an effort to cut labor costs and optimize resources.
These improvements carry the promise of cost and time savings but require significant investments upfront – the average cost for a frequently used solution, an automated guided vehicle (AGV) system, can reach $1 million USD.
Given the expense involved, it’s imperative to plan for a reliable wireless communications network in an environment where accurate, real-time connections can influence whether product is where it needs to be. The right wireless solutions can help you achieve the return on your material handling investment at your facility, opening the door for future improvements.
Keeping Up With Your Cargo
There can be any number of moving equipment transporting parts or product in a material handling application – AGVs, stacker-reclaimers, automated storage and retrieval systems and automotive skillet lines abound all count on reliable communications and signals. Even the smallest hiccups can lead to downtime, which negates the benefits of your automated material handling equipment.
With seamless communications, you can release greater pick and pack accuracy; more streamlined conveyance of product from assembly to the trucks outside; and instant notification of any issues requiring your prompt attention.
One solution that can be used throughout your facility – including on your AGVs – are scalable wireless radios that support very fast access point switchover times, ideally 10 ms or faster. This capability helps ensure that moving parts stay on track – sometimes literally.
Opting for radios that can link back to your central control system can help you stay up-to-date about the health of your equipment – by sending diagnostics directly to personnel who can act upon the information, you can minimize unscheduled downtime.
If you’re in a facility whose environment supports antennas, they can be used in conjunction with wireless radios and moving equipment (as a vehicle manufacturer in England found). Antenna selection and installation can be a little tricky – you will need to determine which ones should be used, and how and where they should be installed.
If you need assistance determining the best antennas for your application, it’s a good idea to talk with a trusted expert to see what they would recommend before implementing your wireless network.
Flexible Cable
Of course, there are many facilities that may be too busy signal-wise for a traditional antenna. In a plant filled with communicating devices, avoiding clashed connections is crucial. Radiating cable is an ideal solution for this type of facility.
The cable’s design features slots that radiate RF signals, and its flexible design means it can be used in tight spots. This can help isolate the signal, minimizing the impact of nearby interference.
In addition to providing a flexible avenue for communication, radiating cable can be used in place of traditional components of material handling systems that have proven problematic for some companies:
- It can be used in place of a conductor rail or buss bar in applications involving an automotive skillet line or electrified monorail system. A conductor rail can be unreliable and hinder production.
- Slip rings on rotating machinery can also suffer from unreliability – and expensive maintenance. Radiating cable can be used as a more robust alternative, boosting performance and reducing downtime necessitated by repairs.
Designing and implementing a reliable wireless communications network can take time, but its ability to improve upon and boost your automated material handling systems’ return on investment cannot be overstated.
For more information https://www.rockwellautomation.com/en_NA/overview.page?