Automation Moves Regenerative Medicine From Lab To Production
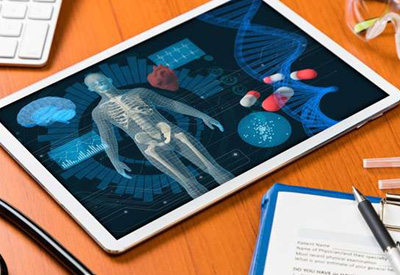
November 12, 2018
By: Dave Vasko, Director of Advanced Technology, Rockwell Automation
What will it take to move highly specialized regenerative medicine – engineering or regenerating human cells, tissues and organs – from lab to production?
Manufacturing scalability, process and partnership.
When Science Meets Manufacturing
While it’s not unusual for science and manufacturing to work together, what we’re poised to do now is unlike anything we’ve done before.
For years people have been working to bridge the chasm between research and commercial production.
Our next breakthrough: Through automation, we will help provide artificially produced tissues and even whole organs to people with serious injuries or disease.
This changes lives.
As quickly as the possibilities are unfolding, the advances largely are still in the research mode. The good news: While the recipes are incredibly specialized, the process of regenerative medicine manufacturing looks a lot like something you’d see in the making of a craft beer — automating the process and using data and analytics to monitor and improve that process to create consistent, predictable results.
Instead of making beer or bread or antihistamines, you’re controlling the growth of human cells.
Scaling, Now
The sooner we make bio manufacturing processes predictable and replicable, the sooner we can offer life-saving advancements.
The question is scale, and taking what happens in the lab and making it work in mass production.
Right now labs can produce cartilage replacements at the rate of a few hundred a year. Moving from that small, manual size to tens of thousands of replacements a year remains a major challenge.
Bringing Powerhouses Together For the Greater Good
Once you achieve scalability, you can apply it to new skin, bones and nerves, to heart patches and almost anything else you can imagine.
But those who specialize in the “bio” part of manufacturing, our PhDs, are focused on research and science, not the nuts and bolts – and the hurdles – of manufacturing. Progress requires partnership to leverage the best of the best.
I liken the future of bio manufacturing to food processing today. Imagine taking a family recipe for chicken soup, made a few dozen times a year, and scaling it up to where it can be mass produced and available in supermarkets around the world.
We need to take the beautiful creations biomedical PhDs are working on day and night, and scale the process so the miracle moves beyond the lab and into the world.
Addressing the Gaps
As far as we’ve come, there are gaps. We are working with Advanced Regenerative Manufacturing Institute (ARMI) to address those gaps to bring regenerative medicine to the masses.
From an engineering perspective, this is the future – leveraging technology and medicine for real, everyday applications that directly impact people. This is work with a high purpose.