How to Build a Real-Time IIoT Application with Moxa’s ThingsPro and Cirrus Link’s Sparkplug
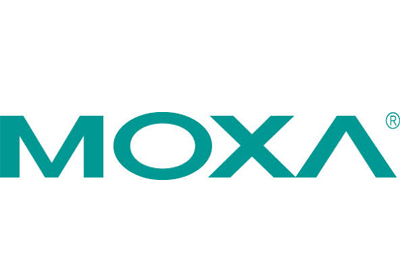
According to data from the BC Construction Association (BCCA), the total contribution of the construction industry to society in the region now exceeds $134 billion, with more than 215,000 workers employed in this sector.
Justin Harris is a Programmer/Electrician for COREngineering, a New Brunswick based mechanical engineering firm that specializes in the design of custom equipment.
A local food producer required large volumes of water to clean and sanitize equipment. Once used, the water would be stored in an on-site lagoon before being processed, treated, and released back into the water supply. The producer’s water usage was increasing as the facility expanded and new equipment was implemented that needed to be cleaned.
If a product is scratched by a robot but nobody was there to see it, how do you know what exactly happened? Intermittent problems in manufacturing lines (such as die casting) can cause millions of lost $$$ when repair workers are forced to troubleshoot without any idea of what may have caused the problem or when the problem will occur again.
In the fast-paced world of manufacturing, unplanned downtime is a significant drain on resources and operational performance, leading to substantial production losses. Obsolescence risk is inevitable and occurs in new and old equipment. Your operation is at high risk for downtime when an original equipment manufacturer (OEM) decides to no longer produce a critical part required to run your production line and there is no available inventory of that part or plan to replace it. Proactive maintenance practices such as planned preventive maintenance (PPM) can go a long way toward reducing the occurrence of unplanned downtime events. However, when these events involve obsolete parts that are difficult to source or replace, the disruption is often prolonged. This is why a strong inventory management program and budget is imperative to manage obsolescence risk. Otherwise, the financial impact of downtime events can be catastrophic.
Control panels present a major opportunity for manufacturers to improve operational efficiency, boost flexibility, reduce engineering costs and save valuable floor space. With this in mind, Omron has developed a unique set of guidelines, known as “Value Design for Panels,” that can help manufacturers create better control panels.
According to data from the BC Construction Association (BCCA), the total contribution of the construction industry to society in the region now exceeds $134 billion, with more than 215,000 workers employed in this sector.
Justin Harris is a Programmer/Electrician for COREngineering, a New Brunswick based mechanical engineering firm that specializes in the design of custom equipment.
A local food producer required large volumes of water to clean and sanitize equipment. Once used, the water would be stored in an on-site lagoon before being processed, treated, and released back into the water supply. The producer’s water usage was increasing as the facility expanded and new equipment was implemented that needed to be cleaned.
If a product is scratched by a robot but nobody was there to see it, how do you know what exactly happened? Intermittent problems in manufacturing lines (such as die casting) can cause millions of lost $$$ when repair workers are forced to troubleshoot without any idea of what may have caused the problem or when the problem will occur again.
In the fast-paced world of manufacturing, unplanned downtime is a significant drain on resources and operational performance, leading to substantial production losses. Obsolescence risk is inevitable and occurs in new and old equipment. Your operation is at high risk for downtime when an original equipment manufacturer (OEM) decides to no longer produce a critical part required to run your production line and there is no available inventory of that part or plan to replace it. Proactive maintenance practices such as planned preventive maintenance (PPM) can go a long way toward reducing the occurrence of unplanned downtime events. However, when these events involve obsolete parts that are difficult to source or replace, the disruption is often prolonged. This is why a strong inventory management program and budget is imperative to manage obsolescence risk. Otherwise, the financial impact of downtime events can be catastrophic.
Control panels present a major opportunity for manufacturers to improve operational efficiency, boost flexibility, reduce engineering costs and save valuable floor space. With this in mind, Omron has developed a unique set of guidelines, known as “Value Design for Panels,” that can help manufacturers create better control panels.
According to data from the BC Construction Association (BCCA), the total contribution of the construction industry to society in the region now exceeds $134 billion, with more than 215,000 workers employed in this sector.
Justin Harris is a Programmer/Electrician for COREngineering, a New Brunswick based mechanical engineering firm that specializes in the design of custom equipment.
A local food producer required large volumes of water to clean and sanitize equipment. Once used, the water would be stored in an on-site lagoon before being processed, treated, and released back into the water supply. The producer’s water usage was increasing as the facility expanded and new equipment was implemented that needed to be cleaned.
If a product is scratched by a robot but nobody was there to see it, how do you know what exactly happened? Intermittent problems in manufacturing lines (such as die casting) can cause millions of lost $$$ when repair workers are forced to troubleshoot without any idea of what may have caused the problem or when the problem will occur again.
In the fast-paced world of manufacturing, unplanned downtime is a significant drain on resources and operational performance, leading to substantial production losses. Obsolescence risk is inevitable and occurs in new and old equipment. Your operation is at high risk for downtime when an original equipment manufacturer (OEM) decides to no longer produce a critical part required to run your production line and there is no available inventory of that part or plan to replace it. Proactive maintenance practices such as planned preventive maintenance (PPM) can go a long way toward reducing the occurrence of unplanned downtime events. However, when these events involve obsolete parts that are difficult to source or replace, the disruption is often prolonged. This is why a strong inventory management program and budget is imperative to manage obsolescence risk. Otherwise, the financial impact of downtime events can be catastrophic.
Control panels present a major opportunity for manufacturers to improve operational efficiency, boost flexibility, reduce engineering costs and save valuable floor space. With this in mind, Omron has developed a unique set of guidelines, known as “Value Design for Panels,” that can help manufacturers create better control panels.
Hubbell is thrilled to announce the promotion of Frank Magisano to the position of Vice President & General Manager of Hubbell Canada. Frank joined the Hubbell team in 2001 and has since demonstrated exceptional leadership and expertise across various departments, including engineering, operations, and business development. His comprehensive understanding of the industry and dedication to… Read More…
Gescan is pleased to announce a new distribution partnership with ABB Motion, renowned for its pioneering solutions in automation and electrification. Gescan will now offer ABB’s high-quality drive solutions in Manitoba and Saskatchewan, making energy-efficient motor control technology more accessible to businesses in the region. “ABB Motion has a long-standing reputation for technological excellence, and… Read More…
The way to the Industrial IoT does not have to be complicated. Whether access to valuable data is required or new, data-driven services are to be generated, Weidmuller enables its customers to go from data to value the easy way. Weidmuller’s comprehensive and cutting-edge IIoT portfolio applies to greenfield and brownfield applications. Weidmuller offers components and solutions from data acquisition, data pre-processing, data communication and data analysis.
Visit Weidmuller’s Industrial IoT Portfolio.
Advanced Motion Controls is proud to announce the addition of six new CANopen servo drives with Extended Environment capabilities to their FlexPro line. These new drives join AMC’s existing EtherCAT Extended Environment FlexPro drives, making the FlexPro line the go-to solution for motion control applications in harsh environments.
Many motion control applications take place in conditions that are less than ideal, such as extreme temperatures, high and low pressures, shocks and vibrations, and contamination. Electronics, including servo drives, can malfunction or sustain permanent damage in these conditions.
Bruce Kesler and Mark Gatewood have been given new titles and responsibilities for Service Wire Co.
Bruce Kesler has assumed the role of Senior Director – Business Development. Bruce will be responsible for Service Wire’s largest strategic accounts and our growing Strategic Accounts Team.
Mark Gatewood has been promoted to the role of Vice President – Sales & Marketing. In this role, Gatewood will lead the efforts of Service Wire Company’s entire sales and marketing organization in all market verticals.
Recently, Tri-Mach Inc. was thrilled to announce the addition of a new 45,000 sq ft. facility. Located at 285 Union St., Elmira, ON, this facility expands Tri-Mach’s capabilities, allowing them to better serve the growing needs of their customers.
Positioning for growth, this additional facility will allow Tri-Mach to continue taking on large-scale projects, enhance product performance testing, and provide equipment storage for their customers. The building will also be the new home to their Skilled Trades Centre of Excellence.
Convergix Automation Solutions has completed the acquisition of AGR Automation (“AGR”), a UK-based provider of custom, high-performance automation design and systems integration primarily to the life sciences industry.
Following Convergix’s acquisitions of JMP Solutions in August 2021 and Classic Design in February 2022, AGR marks the third investment in Crestview’s strategy to build Convergix into a diversified automation solutions provider targeting the global $500+ billion market, with a particular focus on the $70 billion global systems integration and connectivity segments. Financial terms of the transaction were not disclosed.
Innovation, customer focus and active cost management: SICK, an international provider of sensor-based automation solutions headquartered in Germany, set these focus points and achieved a solid result in the challenging business year 2024. Sales and EBIT decreased, while investments in research and development remained high. In a difficult market environment, SICK performed robustly and was… Read More…
Your products will come out on top, of course, but the machinery and equipment that ensure their production and quality are likely to be a close second. Conducting a criticality analysis is largely about prioritizing and focusing time and effort on the capital equipment assets you’ve determined to be the most important in your operation.… Read More…
This project is funded [in part] by the Government of Canada.
Ce projet est financé [en partie] par le gouvernement du Canada.