Rockwell Automation: Extending Your Reach to Robotics
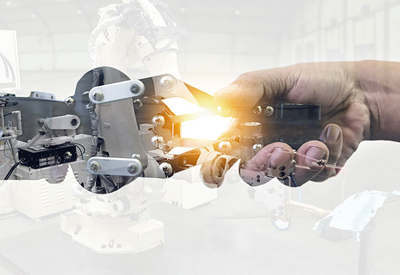
January 2, 2019
By Mike Wagner, Rockwell Automation
For today’s manufacturers, a flexible plant floor is a business imperative. As product SKUs continue to increase, manufacturing equipment simply must be more agile to accommodate more product variations – faster than ever before.
To meet the needs of flexible “high mix, low volume” production environments, more OEMs are moving away from fixed mechanical systems and developing innovative ways to incorporate robotic technology. This trend is particularly prevalent in material handling, pick-and-place and assembly applications.
Why? Traditional systems operate on a single horizontal plane and are based on fixed variables associated with handling a large volume of the same or similar product. On the other hand, robotic technology, which tends to mimic human motion, enables movement within the entire 3D work envelope.
This ability to break the plane and operate fully in three dimensions is a game changer. “Pick” and “place” options can be infinitely variable – and can include horizontal and vertical elevations. The robot determines the appropriate path. No complex mechanical rerouting is required.
And thanks to customizable and interchangeable end effectors, the same robot can handle a wide range of product shapes and sizes.
Conventional Challenges
Machine builders certainly recognize the advantages of robotics and the manufacturing demand for it. But until recently, incorporating robotic technology cost-effectively has been difficult.
Historically, OEMs relied on third-party robot suppliers, who provided equipment that ran on custom high-end processors distinct from the control platform running the remainder of the machine. Programming the robot often required a skill set that was outside the purview of the OEM staff. And since two control platforms were involved, integrating the robotic application with upstream and downstream processes was cumbersome.
Simpler, Better Programming
The latest robotic technology has changed the equation for OEMs. The truth is, contemporary robots are oftentimes simpler to program than traditional mechanical systems, thanks to machine learning technologies.
For example, “imitation learning,” enables a robot to replicate a task it is shown. I was recently involved in a case packaging application that used this technique to full extent. To teach the robot to pick, lift and place the product in the case, we simply moved the robotic arm to the three appropriate locations.
The robot controller interpolates the information and generates its own path or plan for movement. In other words, the path plan – and about 80 percent of the robotic programming required – is automatically generated.
Depending on the complexity and variability of the application, vision-guided or collaborate robots can be deployed and programmed using similar machine learning techniques.
While machine learning has simplified robotic programming, the latest programmable automation controller (PAC) technology represents a transformational turning point for OEMs. Thanks to enhanced processor speed and performance, robotic applications can now run on the standard PACs that control the rest of the machine.
For example, this PAC features a processor that can provide up to 45 percent more capacity than previous generations to meet the high-speed communications and motion control demands of robotics.
Equally important, OEMs can achieve the advanced safety functionality required for robotic applications within the PAC platform – and standardize their approach to safety across the entire machine.
Of course, using a single, unified platform for both robotic and machine control speeds OEM equipment development, integration and deployment. In addition, OEMs can more easily extend innovation across their complete portfolio and take more control over all aspects of their machinery.
Each year, we are seeing more machine builders take advantage of a unified control platform to develop flexible robotic equipment – and optimize lifecycle management. Take a look at this example.
And learn more about how machine builders are using the latest technology to develop innovative machines.