Capital Asset Optimization: Harnessing IoT Data & Predictive Maintenance
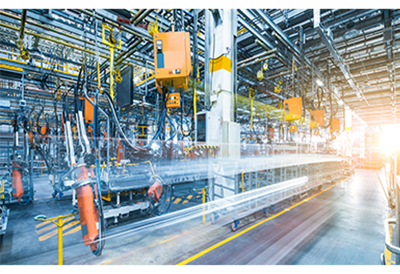
January 21, 2019
By Ron McKay
For any business dealing with capital-intensive assets, maintaining machines and equipment is a continuous battle.
From damaged equipment and undetected malfunctions to total machine failure that leads to unexpected (and costly) downtime, knowing how to future-proof your assets is a challenge. If your strategy is to only fix when something breaks, you’re in a reactive mode, which often costs more and leads to extended, unplanned downtime, ultimately impacting your bottom line.
Instead, what if you could know ahead of time when an asset will fail, and you could monitor your assets’ health over time to determine the ideal frequency for maintenance?
It’s possible – with predictive maintenance.
Predictive Maintenance – Your Greatest Asset
Predictive maintenance has emerged as a game-changing solution for asset management. According to a report by TechSci Research, the global predictive maintenance market is projected to grow at a compound annual growth rate of 31% between 2017 and 20221. Today, we see companies across various industries, such as energy and utilities, manufacturing, transportation and healthcare, adopt predictive maintenance solutions.
This solution involves using data to identify warning signs, predict maintenance requirements on equipment and preemptively service that equipment at optimal times before problems occur.
By connecting your assets with IoT sensors and analyzing the real-time data with advanced analytics, such as machine learning, the insights give you a full picture of asset health, and help you anticipate maintenance so as to avoid unplanned downtime.
In many ways, a company’s greatest asset could be the advanced technology that keeps their capital-intensive machines and equipment running at an optimal level.
Here’s why:
A Deloitte study2 found that predictive maintenance solutions can:
• Increase equipment uptime by 10 to 20%
• Increase productivity by 25%
• Reduce breakdowns by 70%
• Reduce maintenance costs by 5 to 10%
• Reduce maintenance planning time by 20 to 50%
Implementing predictive capabilities will represent a significant competitive advantage for organizations with capital-intensive assets – and put you at the leading edge of where technology is headed.
IoT-Enabled Predictive Maintenance for Wind Farms
Today, we’re starting to see the increased adoption and exponential growth of IoT that was forecasted. However, unlocking the potential IoT has to offer for predictive maintenance doesn’t have to be difficult. It starts by building on the infrastructure you have in place today and incorporating the right technology so that you can use your data, deliver better insights and take action.
Take a wind farm as an example. If the wind farm has 50+ wind turbines and hundreds of sensors firing, getting to the data that matters to make informed decisions is essential to improving the environment. Any unplanned maintenance or downtime will be both costly and inefficient. In fact, the ability to identify underperforming wind turbines is critical to managing turbine operating costs and enabling comprehensive and targeted blade inspections.
With an IoT-enabled predictive maintenance solution, a wind farm can proactively schedule turbine service and avoid potential failures, while optimizing performance and efficiencies across the entire farm.
It starts by:
1. Ingesting and organizing data from a variety of systems and sensors, such as wind turbine telemetry and local weather stations.
2. Analyzing the data for issues and anomalies using predictive models. This includes training the predictive model with historical data to identify what normal turbine behaviour looks like to get a performance baseline, then comparing each individual turbine’s performance to it.
3. Visualizing key data and findings for further analysis and decision-making on a dashboard. This includes real-time insight into what turbines require maintenance, why and when.
The result? Implementing predictive capabilities into a wind farm’s operating model means the business can focus their technicians on the observations that really matter, understand root causes of problems better, and dedicate their time to the blades that require the most maintenance.
Microsoft Azure is making predictive solutions and machine learning more attainable for businesses. The solution described above is built on the Microsoft Azure platform to create a predictive maintenance engine that uses Azure Data Factory to coordinate data, Azure Databricks for predictive modelling, Azure Data Lake Store as the central data repository, and Power BI for data visualization, to name a few of the Microsoft technologies deployed.
How To Get Started on Your Predictive Maintenance Project
You can get started quickly on successfully deploying a predictive maintenance solution to achieve high asset utilization and increase ROI for your capital-intensive assets.
1. Understand the business opportunity and the outcome you’d like to achieve through predictive maintenance.
2. Start with a discovery phase to assess the data you have available and prioritize requirements to ensure that the solution meets the unique needs of your business.
3. Get the right stakeholders engaged to drive alignment and agree upon the set of measures and KPIs needed.
T4G has assisted a variety of companies with the planning and implementation of custom predictive maintenance solutions. And for wind farm operators, we have a proven solution framework ready to be configured, that will deliver the results you need in a fraction of the time.