The Role of Smart Building Technologies in Facility Management
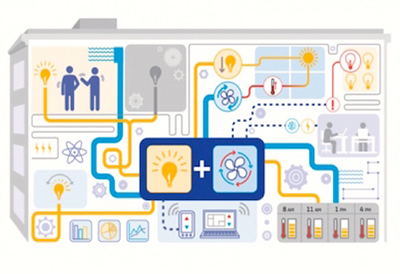
February 26, 2019
By Caryl Anne Crowne
Digital smart technology is changing almost every aspect of how we live, and the buildings we live in are no exception. Increasingly, instead of humans deciding how a building is heated, lit, etc., smart technology is gathering data, analyzing it and reacting accordingly while whoever is inside the building goes about their normal activities. Smart technology in buildings not only makes life more convenient for their inhabitants, it is more efficient and therefore saves on energy bills and reduces the negative impact of the environment.
Smart technology will make life easier for visitors to public facilities. For example, someone attending a meeting at a given building can have their identification badge read automatically and then get a text message informing them what room their meeting is in and how to get there. Once in the room, the temperature will already be adjusted to a comfortable level.
Here are two leading technology changes and their impact.
Li-Fi
Li-Fi uses information transferred from the light of LEDS to make decisions; it is similar to Wi-Fi, but it uses light instead of radio waves. As Li-Fi evolves, it is expected to be even faster than Wi-Fi, and Li-Fi systems will likely have many impacts on facility management as it gradually replaces Wi-Fi.
For starters, faster signals mean that a smart building can accommodate more digital devices and, consequently, more of the people using them. Basements and other Wi-Fi “dead zones” will be available for use, and security will be improved because Li-Fi signals cannot be picked up outside of the building. Additionally, Li-Fi can be used around equipment that is sensitive to electromagnetic interference, and this is an enormous benefit in hospitals full of medical devices.
BIM Three
Building Information Management (BIM) Level Three for sharing electronic data, as defined by the British government, will be a game-changer for facility management. At Level Three, more people will have access to information about a given building. Moreover, these data will be held in a single repository rather than spread out in different places, as is often the case currently.
Role of the facility manager
One big effect that smart technology will have is that facility managers will no longer have to spend as much time gathering and monitoring information because computers will be doing these tasks. This is a positive development because it will free up facility managers from dealing with the building to focusing on the well-being of the people within the building.
When it comes to meetings and events, sensors will detect when attendees have arrived and when they have left and adjust heating and cooling systems accordingly so that no energy is wasted. Furthermore, sensors can be aligned with the booking system for events so that planners have real-time feedback.
Traditionally, facility managers have spent much of their time behaving in a reactive manner. For example, something breaks in the mechanical room, and there is a frantic scramble to get it fixed. With the automation that comes with smart technology, it will be easier to predict failures before they happen, and the role of the building manager will change to someone who is planning ahead rather than putting out fires.
The new roles of facility managers will also depend on the type of building being managed. A facility manager working in a hotel, for instance, is going to focus on gathering information on noise in the night with the goal of lowering it because loud sound is what prevents guests from falling asleep. In an office building, on the other hand, the workers are gone at night and a little extra noise in the day may help them stay alert and productive.
In data centres, gathering information about temperature will be critical because computers operate best in a certain environment. Hospitals present another set of challenges with an emphasis on monitoring all variables related to the power and back-up power systems that keep medical equipment running.
Conclusion
Across the globe, the demand for buildings that are eco-friendly and cost-efficient is creating a need for a new type of facility manager who understands how to work with smart technology. The facility managers of the future will be skilled at reading data, which is largely a new skill set in the profession. As with many other jobs in the current age of rapidly evolving smart technology, the time to start learning and adapting is now.
Caryl Anne Crowne is a contributing writer and media specialist for Mr. Electric. She often produces content for a variety of electrical industry blogs.