Productivity Master points the way to Digitalisation
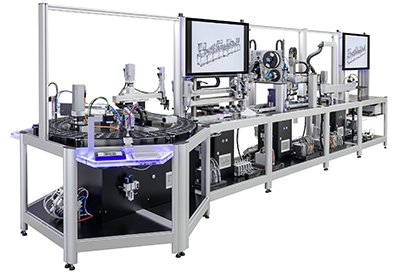
April 4, 2019
The Productivity Master, a modular demonstration system for personalised USB memory sticks from Festo, is showing how automation technology will evolve along the value chain when combined with digitalisation. Thanks to software, everything fits perfectly, from the mechanical and electric systems to the intelligence. The Festo automation platform provides an integrated and practical system to link all Festo engineering tools, components and solutions in hardware and software.
The demonstration system Productivity Master personalises USB memory sticks in four steps. The electric products, the mechanical systems for the axes, the electrics and the software are organised into a complete automation platform with seamless connectivity. This saves users an enormous amount of time, from planning to commissioning, and they gain maximum process reliability since everything fits together. With Industry 4.0 as standard.
Four fully connected stations
Visitors to the stand create the production order at the first station by registering with their name and perhaps a picture. A QR code identifies the visitors at the machine. A vision sensor SBSI from Festo registers the visitors and starts the production order. This is followed by stock management. This mechatronic complete solution, made up among other things of a planar surface gantry EXCM in size 40 for fast picking and placing of the USB memory stick, offers all the options from stock management and workpiece handling to the cloud.
The USB memory stick is then transported, printed, turned over and then passed on. The work steps at the second station involved are holding, moving, handling, rotating and positioning and identifying the workpiece position as well as identifying, separating, gripping and applying labels. Fast transfer to a label printer is carried out at station 3 by a highly dynamic linear gantry EXCT with dynamic servo motors EMMT-AS and servo drives CMMT-AS. The rotation functions are carried out by electric rotary drives ERMH.
The process is completed in station 4 where files are uploaded to the USB memory stick. This involves holding the workpiece, turning and carefully positioning the cap and press-fitting delicate parts. This is done using the attractively priced electric cylinders EPCO and rotary drives ERMO. The personalised USB memory sticks are then handed out to the visitors.
Seamless connectivity and engineering tools
The machine was planned in record time. The state-of-the-art and standardised Festo engineering environment proved useful here. Projects, Festo’s first lifecycle management platform, simplifies project planning and the management of digital twins. This enables design engineers and developers worldwide to work collaboratively. With the Festo Handling Guide Online (HGO), users can select and size 1D, 2D and 3D gantries in just three steps, including planar surface and linear kinematics.
With the Festo Automation Suite, design engineers can program and configure in one environment and commission the complete drive system quickly and easily. The Festo dashboards and AI algorithms (artificial intelligence) from Resolto, our partner company, are available if users want to visualise their data from the cloud and use big data analytics.
Go HERE for more information