5 Ways MES Software Can Help You Meet Metals Production Challenges
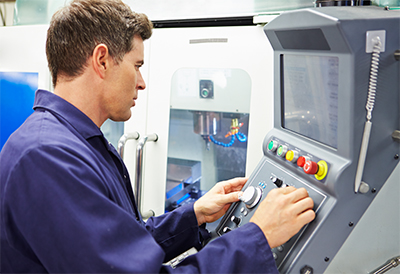
April 18, 2019
Meeting customer demands for better, lighter and stronger metal products can be a lot to tackle without the right tools.
Today more than ever, you need technology that can give you real-time, actionable information about your operations. You can try creating a home-grown solution. But often, they can be difficult to support due to limited knowledge and technology turning obsolete.
That’s why many metal producers turn to manufacturing execution system (MES) software. It integrates, tracks and manages your intricate manufacturing systems. And, it can help ensure effective execution of activities within your manufacturing process.
For example, one American steel pipe producer implemented MES to give workers better operational visibility. The result? Workers improved cut optimization and increased yield by 2 percent, and the company is saving millions of dollars per year.
Utilizing MES can help you determine how best to deliver the right product, at the right time, created from the most cost-effective and appropriate raw materials. Here are five ways MES software can help you address your specific metal production challenges:
1. Better Production Intelligence. MES brings together your business, energy, production and logistics data by connecting equipment, control systems, applications and databases. In doing so, you can identify production issues like bottlenecks and quality issues through mobile dashboards and production trend reporting using real-time performance information.
MES also connects the mill floor to your ERP systems. This allows production reports to be delivered directly to the ERP, which is then populated with the corresponding material consumption, quality and process information.
2. Improve Performance. MES delivers productivity metrics like overall equipment effectiveness and downtime analysis in context: by shift, by area and by production site. Production information can also be cross-referenced with other data, like energy consumption. This allows you to pinpoint productivity issues and identify where costs can be reduced.
3. Greater Recipe and Order Management. You may still be developing and entering recipes manually – and managing workflows using physical documents. This is time-consuming work that is prone to error. MES allows you to create and store recipes, standardize operating procedures, and synchronize order management directly with the ERP system.
And when a new order comes in, MES can interface with the ERP to manage production schedules, including quality and operational settings. MES also generates the most appropriate work orders – selecting the optimal sequence and executing those orders down to the plant floor. This means the right recipe set-points are delivered straight to the control layer for automated and accurate recipe execution.
4. Enhanced Quality. Pre-designed workflows and instructions are delivered by MES. This can help operators stay within specified quality parameters. MES can also collect data from quality checkpoints and send hold codes, or production alerts, if products don’t match the desired quality to prevent the release of bad product.
Scrap tracking can also help users understand why products were scrapped to minimize recurring issues.
5. Complete Track and Trace / Genealogy. Visibility throughout your production process is of the utmost importance. MES gives you visibility from your raw material all the way through to your finished product. It can track lot- and piece-level inventory, work-in-progress inventory, materials on hold, and finished goods waiting to be shipped.
Product traceability provides historical information, including manufacturing origin for each piece of metal. This information can be stored within MES and then linked back to your ERP systems for material resource planning, sequencing of orders and shipment scheduling.
Create More Competitive Operations
MES puts real-time information at your fingertips, helping you meet today’s changing customer demands and better compete long-term.
For example, like many other industries, the metals industry is in the midst of a large-scale workforce transition. Older workers are retiring and taking their knowledge with them. Storing instructions and procedures within MES allows for simpler, safer and less disruptive new employee onboarding.