Omron: What’s Driving Automotive Traceability Today?
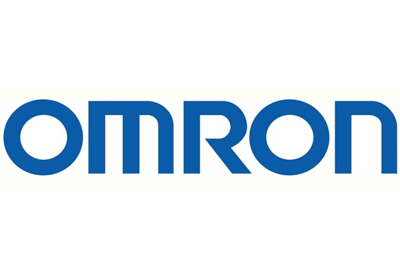
A need for comprehensive documentation
There is a parent-child relationship between the components and assemblies that go into a given vehicle, and manufacturers need to maintain thorough records on the parts comprising a new car for several reasons. From a quality standpoint, keeping track of this relationship with barcodes helps ensure that the correct parts get bundled together for a given vehicle model. Even more important, however, is the ability to trace every automotive part back to its original supplier. In the event of a recall or the discovery of a flawed part, it pays to have a comprehensive, easily accessible record of where each part came from, the lot number, date of manufacture, and other critical information to identify which vehicles are affected by a faulty part. Recommendations and standards from AIAG, VDA, ANSI and ISO lay out the details.
Traceability data includes any information that identifies a work-in-progress (WIP) part or assembly and its origin. To ensure that each part carries this data wherever it goes, the data is encapsulated into a barcode that is affixed to the part. In most cases, this barcode will actually be a direct part mark (DPM) – a marking that is etched or printed directly onto the part This is necessary for ensuring that the markings are permanent and inseparable from the part bearing them. In other instances, automotive manufacturers use labels to facilitate traceability.
Omron offers several key technologies for implementing what is known as “cradle-to-grave traceability”– the process of applying DPMs to parts so that these markings will last for as long as the part remains in service. One of these technologies is the MX-Z fiber laser marker series, a set of machines that can apply exceptionally high-resolution and highly durable markings on a variety of materials. The MX-Z series offers great marking flexibility thanks to its thorough connectivity and ability to integrate easily with other systems and controls. Easy integration is a major advantage when thousands or even tens of thousands of parts need to be marked for every new vehicle.
An automated solution for improving process control
Keeping thorough tabs on the origin of automotive parts – particularly mission-critical ones – on a cradle-to-grave basis is essential for ensuring that recalls are handled in a way that is both thorough and cost-effective. If part origin is incompletely documented, manufacturers need to recall a much wider set of vehicles than is necessary when they can precisely pinpoint the vehicles containing the faulty part. Recalls are expensive in general, but smartly implemented recalls can save companies thousands or even millions when compared with those that are sweeping and indiscriminate.
Traceability also helps eliminate – or at least mitigate
– another thorny issue plaguing the automotive industry: part counterfeiting. Counterfeit parts not only cost the industry billions of dollars a year, but also put drivers and other users of roads and highways at risk. Automotive parts suppliers are facing increased demands for product verification to combat the trafficking of fake vehicle parts.
Although preventing the incorporation of faulty or counterfeit parts into finished vehicles is perhaps the most mission-critical goal of automotive traceability, the omnipresent direct part markings, labels and sometimes RFID tags serve another important purpose: streamlining the manufacturing process itself. Real-time traceability systems convey process information from zone to zone, making it possible to optimize the supply chain and reduce lead times. They monitor and compare lines, providing the data necessary to figure out which production steps are taking longer than expected and drill down into why that’s happening.
Whenever a code is read on the factory floor, the traceability system will transfer this data to a manufacturing execution system (MES) or enterprise resource planning (ERP) software system, helping to correctly bundle parts together and direct other elements of the production line in a thoroughly data-driven way. Traceability is used to mark powertrain components with specific dimensions to ensure that they fit together with exceptional precision.
Automating a certain amount of the low-level decision-making significantly reduces the likelihood of errors. However, it introduces a new challenge due to the need for barcode readers (or RFID readers in cases where RFID tags are
used) to be incorporated into space-constrained machinery on the assembly line. Omron addresses this challenge with its MicroHAWK product line, an ultra-compact family of barcode readers specifically geared towards applications that require readers to be embedded inside complex equipment.
Although they are quite small, the MicroHAWK barcode readers feature industry-leading decoding algorithms, a variety of sensor and optics configurations, Ethernet/IP and Profinet connectivity, and a powerful liquid lens autofocus technology. Thanks to these innovations, the MicroHAWKs are able to read a wide variety of codes at varying distances. They also work right out of the box with the browser-based WebLink program, meaning that no software installation is required. Their flexibility and out-of-box reading allows them to efficiently support industrial applications without requiring the applications to support them in turn.
More markings (and smaller markings) in tough environments
The powerful X-Mode decoding algorithms of the MicroHAWK barcode readers are critical because automotive factories present the sort of harsh conditions that are likely to damage barcodes over time. X-Mode is capable of reading codes with distortion, fading or other types of damage thanks to its exceptional ability to reconstruct symbols. In addition, the two-dimensional Data Matrix symbology contains enough redundancy to allow for a significant amount of symbol damage without sacrificing readability.
A key trend in today’s automotive industry is to require nearly every part to carry a mark from almost the very beginning of its service life. This is important for identifying and solving problems before they escalate into major catastrophes, but it also presents a new challenge in turn. Ensuring that every part bears a mark means that certain barcodes need to be exceedingly small. As with damaged codes, minuscule codes require high-performance barcode readers like the MicroHAWK series in order to be read with the necessary speed and accuracy.
Since more markings are applied earlier on in the manufacturing process, they’re more likely to degrade under the challenging factory conditions. Through exposure to high heat, pressure hose spray- downs and corrosive industrial chemicals, barcodes – even when applied with a durable method like laser marking – can suffer some damage. For this reason, it’s essential that barcodes start out with the highest possible degree of readability.
To ensure that barcodes are of good quality and should be expected to remain readable throughout the part lifecycle, manufacturers can set up a verification system to grade them against specific international standards such as ISO/IEC TR 29158. Omron offers several best-in-class verification systems for both in-line and off-line verification, including the LVS-9580 and LVS-9585 handheld verifiers that can verify codes as small as 2 mil (meaning that the size of an individual dark or light cell can be just two thousandths of an inch). Diagnostic tools within the LVS-95xx software provide troubleshooting information needed in order to adjust the marking equipment such that the barcode quality grade is improved.
Verifiers can be used for DPMs or labels. Some verification systems, like Omron’s LVS-7510 Print Quality Inspection System, are designed to be incorporated into printers and provide 100% label inspection as the labels are being printed. Using tools like code capture and optical character recognition (OCR), the LVS-7510 can verify that the machine-readable codes and human-readable alphanumeric sequences on the labels contain the same information. It also grades barcodes according to ISO standards and enables proactive printer maintenance by alerting operators when print quality starts to degrade .
Several giants in the automotive industry are embracing global platforms for vehicle design. These global platforms involve using a standardized architecture within a flexible manufacturing context to enable millions of vehicles to share the same basic parts. This helps manufacturers spread the costs of manufacturing equipment and product development across a wider production base, but it also means that a single faulty – or counterfeit – component can have a huge impact. In fact, counterfeit automotive parts are becoming a larger problem as the market becomes more globalized.
With the top ten global platforms expected to produce nearly 30 million vehicles in 2020 according to the consulting group IHS Automotive, automakers are finding robust traceability system to be more critical than ever. The exceedingly vast supplier system generated by the globally standardized architecture requires real-time visibility to correct problems quickly before they impact millions of new cars going to market. One of the major goals with real-time traceability is to capture and utilize as much data as possible without making the overall systems inordinately complex.
Processing all the data generated through the scanning of barcodes throughout a manufacturing facility can dramatically lengthen production cycles unless manufacturers use specialized technology designed to mitigate this issue. Omron’s NX/NJ controllers are built with this specific problem in mind. By using embedded SQL clients to directly transfer data to a SQL database, these controllers can process traceability data without hampering machine control performance. Compared to the traditional method of collecting data known as supervisory control and data acquisition (SCADA), logging via SQL has a much smaller footprint on machine cycle time and can enhance productivity by as much as ten percent.
Summary
The challenges faced by automotive manufacturers today are intense and complex, and globalization is pushing a need for more thorough documentation from the very beginning of the manufacturing process. Standardized platforms are influencing a greater percentage of overall vehicle production, and yet the factory floor still features the harsh environment that can hamper efforts to implement traceability.
With a global presence and an expertise in integrating traceability functionality into overall solutions, Omron is well-positioned to help automakers deal with these challenges. Omron has a full automation and robotics offering for comprehensive manufacturing solutions, and it participates actively in AIAG and other important industry associations. Its intelligent and integrated traceability solutions, including laser markers, high- performance barcode readers, barcode verifiers and productivity-enhancing controllers, are designed to address the need for capturing and analyzing more comprehensive data without slowing down production.
https://automation.omron.com/en/ca/
References
- Gao, Paul et al. (2016). Disruptive trends that will transform the auto industry. Retrieved June 11, 2018 from https://www.mckinsey. com/industries/automotive-and-assembly/our-insights/disruptive-trends-that-will-transform-the-auto-industry
- Sedgwick, David in Automotive News. (2014). Carmakers bet in big global platforms to cut costs. Retrieved June 30, 2018 from http://www.autonews.com/article/20140804/OEM10/308049988/carmakers-bet-on-big-global-platforms-to-cut-costs
- Williams, Marcus in Automotive Logistics. (2013). Counterfeit parts are costing the industry billions. Retrieved June 11, 2018 from https://automotivelogistics.media/intelligence/16979
- Microscan. (2018). Direct Part Marking: The Basis for Cradle-to-Grave Traceability. Retrieved June 30, 2018 from https://info. microscan.com/whitepaper-dmp-marking.