Rockwell Automation: Beyond Data Integrity
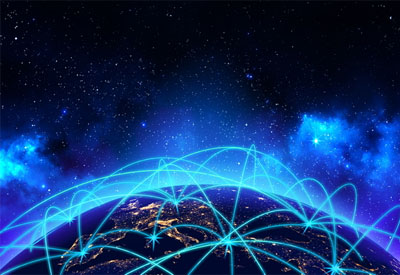
July 10, 2019
By Brian Vogel, Rockwell Automation
We all know that technology is advancing at an incredible rate. Particularly within the past two years, the rapid evolution of the Industrial Internet of Things (IIoT) has enabled manufacturers to take significant steps toward digitalizing their operations.
Of course, the success of any digital journey is based on the underlying integrity of system data. And here, life sciences companies have an advantage. Maintaining complete, consistent and accurate data has long been foundational to Good Manufacturing Practice (GMP) – and validation and compliance.
What has changed is how the latest technologies can enhance and extend the value of that process data to impact all areas of manufacturing.
What Can New Analytics Frameworks Do?
Legacy life sciences systems were built to achieve a specific outcome in a stringent, regulated way – and they do that very well. The data generated is typically maintained in electronic batch records (EBR) for compliance purposes and may be used retrospectively by data scientists to analyze or improve processes.
Emerging analytics frameworks change that equation by providing tools that not only access more data more easily – but also expose hidden relationships between data sources in real time.
For instance, we know digital tools can capture data individually generated by an operator, a material or a machine. But that only tells part of the story. Now data can be combined and presented in the context of what is happening around it.
Data contextualization enhances the overall integrity of the batch record – and improves real-time business outcomes.
How It Works
Contemporary platforms include data discovery and storage tools that simplify data collection across multiple devices and systems. And incorporate analytics tools that intelligently fuse related data to create a more comprehensive, digitally integrated record of the process.
What’s more, these analytics engines can connect data in new ways – and deliver customized, real-time dashboards and reports to uncover new insights at every level of the organization.
For example, analytics platforms can now access, integrate and contextualize data from sources that were not traditionally associated with a batch record – such as building temperature and humidity or material hang-time. And then pinpoint better ways to thwart exceptions in real time. No data scientist required.
But that’s just one way evolving technologies are making an impact across the industry. Ultimately, contextualized data provides the basis for dynamic machine learning models that can drive processes to optimal outcomes prescriptively.
Imagine a system that oversees operations and alerts personnel regarding abnormal situations. Or observes product quality and specifies issue causes – without waiting for lab results. Machine learning makes these scenarios a reality.
Where to Begin
While the latest breakthroughs hold great promise for the life sciences industry, taking the first steps toward implementation can be challenging. But you can ease the process. Here’s how:
- Establish a long-term strategy around data integrity and digitalization. Remember, because technology is changing so quickly, your strategy must be flexible enough to bend and not break when confronted with new developments. Establish a vision, but know that vision will evolve.
- Secure executive buy-in. Engaging executives early and establishing how return on investment (ROI) will be measured is critical. Keep in mind, a traditional weighted approach to ROI may not be 100% applicable.
- Embrace a “sprint” mentality to new technology deployments. Focus on efficient 6- to 10-week test-runs that enable quick learning curves – and establish proof points with minimal investment in time and money.
- Select a scalable, flexible foundation. Choose a partner who takes a flexible and holistic approach to leveraging digital technology. Be sure your partner can deliver solutions that operationalize data in a consistent way – and scale to fit the desirable outcomes across your network.
- Do the homework. Before engaging with any technology supplier, document your existing infrastructure, process flow map, and current business challenges and gaps. Preparing for that first meeting is a good foundational exercise that can also decrease the total time of an engagement by one third or more.
Take the next step and learn more about digital transformation in the life sciences industry.