Top five myths about robotics
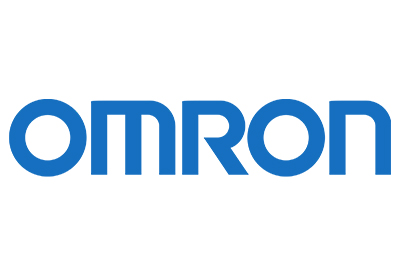
July 16, 2019
Widely represented throughout science fiction, robots (both real and fictional) have been capturing people’s imagination for decades. As robotic solutions gain popularity among manufacturers as a means of increasing productivity, several myths have arisen regarding their place in factories and in society as a whole.
As a provider of state-of-the-art robotic solutions, we’d like to shed some light on five of the most common robot-related misconceptions that we encounter.
1. They’re difficult to use.
Although it can be a challenge to program a robot from scratch, many OEMs – including Omron – have focused on simplifying robot programming with user-friendly software. Omron’s Automated Control Environment (ACE) is a PC-based software featuring an intuitive wizard-based interface, superior data visualization and fast emulation for quick proof of concept of applications ranging from simple pick-and-place to multi-robot belt-tracking lines.
For flexible manufacturing systems, a fairly new technology known as the collaborative robot is gaining traction. Commonly shortened to “cobot,” this type of robot – of which Omron’s TM Series is an example – incorporates intuitive hand-guided mechanisms for teaching new tasks and eliminates the need to explicitly program the movements of the robotic arm.
2. They’re prohibitively expensive.
Robots are actually becoming more affordable by the year. In fact, the average cost of a robot has gone down by a half (in real terms) in the past 30 years. In addition, software solutions that make robot programming more accessible are helping manufacturers reduce engineering time and avoid paying high fees for the services of a specialized robot programmer.
It’s also important to note that, if implemented intelligently, a robotic solution pays for itself by dramatically increasing production efficiency and keeping quality consistent. Robots can perform repetitive tasks at extremely high speeds without needing to take breaks, and this poses major benefits for a company’s throughput and responsiveness to market demand.
3. They’re dangerous.
Some robots, particularly high-speed articulated, SCARA and Delta robots, are not intended to work in proximity to humans. Nonetheless, they are actually designed to boost the safety of an application by taking over tasks that would be hazardous for human workers to perform manually. If humans were to perform these tasks, the risks of an accident would be much higher.
Collaborative robots, on the other hand, are designed to work with a human operator. These robots have a lightweight design with rounded edges and minimal pinch points, and their safety devices can detect when a person has entered into their vicinity (allowing them to operate at higher speeds when humans are absent). When sharing tasks with human operators, cobots uses sensors to detect possible collisions and immediately slow down or alter their path.
4. They’re only used for building cars.
Robots can significantly improve the efficiency of nearly any pick-and-place application in any industry, not just automotive. Packaging lines are a major beneficiary of high-speed robotic solutions that can handle up to 2,000 items per minute. When fully automated, a pick-and-place application reduces manual labor costs, boosts productivity and improves quality.
People tend to imagine robots primarily as fixtures of automotive production because it includes many tasks that are difficult or even downright dangerous for humans. However, many other industries have their own hazards – like chemical washdowns in food and beverage processing – that make robots a welcome solution.
5. They’re responsible for job losses.
Technological advancements have taken over large categories of jobs throughout much of recent history, but the ultimate result has always been the creation of new job categories in a new economy rejuvenated by newfound productivity. Today’s advancements in robotics are likely to have the same stimulating effect.
For one thing, the tasks that robots are currently well-suited for are the repetitive and often hazardous activities that workers find dull and frustrating. When robots can free up human workers from tasks like industrial welding, cleaning up nuclear waste and inspecting oil pipelines, job seekers no longer need to consider opportunities that would put them in harm’s way.
Omron’s philosophy is to contribute to a better society by giving machines the tedious jobs while allowing humans to focus on creative work that puts our intellectual capabilities to good use. Our technologies are designed to work in harmony with humans – solving problems, teaching new skills, making workplaces safer and supporting business growth. We believe in the power of technology to enhance and extend human capability and to unleash human potential.
Find out more HERE.