Industry 4.0: The Challenges and Risks
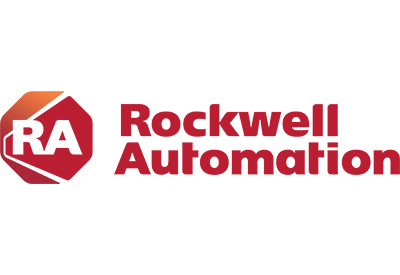
July 16, 2019
The fourth Industrial Revolution (also known as Industry 4.0) is a trending topic today. The entire concept represents full industry digitalization and is closely related to the Internet of things (IoT) infiltrating all industrial areas, resulting in the creation of an industrial internet of things, or IIoT for short.
Industry 4.0 and IIoT are exciting concepts that require a company’s infrastructure to be fully interconnected. The traditional approach was based on separate operational technology (OT) and company information (IT) systems. Over time and thanks to technological advances, these areas grew closer until they finally fused together.
If configured correctly, the interconnection of that infrastructure brings companies advantages in terms of time and money saved.
It is possible to provide monitoring, planning and maintenance, basically, in real time because the data is immediately available. This type of easy data accessibility, and mutual dependency and interconnection of systems, however, also has certain risks. One of the main challenges of digitalization is cybersecurity. I will discuss this and other key challenges of Industry 4.0 in detail below.
Main Challenges
- Security: The interconnection of systems is a key feature in industrial digitalization, which also, however, represents a security challenge in terms of data protection. This data must be secured against direct, external hacking attacks but also against unintentional data leaks, for example, as a result of employee error or lack of competence. The question of cybersecurity is especially important for managing infrastructures that are critical for a functional state (production and distribution of electricity and gas), as well as infrastructures with a risk of environmental and health hazard accidents (chemical plants, nuclear power plants etc.).
- Testability: Each new system or a change in a system must be tested in an industry setting prior to deployment so that its security and reliable response in various situations can be verified. Testing has always been a critical phase of the change implementation process even in the era of separate OT and IT systems. Once a company is fully integrated and digitalized, testing becomes a challenge more complex than ever before.
- Using elements of artificial intelligence: A topic that is much discussed in relation to Industry 4.0 is the use of artificial intelligence for autonomous control, as well as for purposes of intelligent and predictive maintenance, control optimization and decision-making processes and, finally, for increasing security (e.g. face or speech recognition). To function correctly, most artificial intelligence algorithms require a “learning” or “training” phase using a representative data sample. Obtaining such data, however, is another important challenge. Not only it is necessary to obtain an adequate amount of relevant data for learning, but it must also be proven that this data adequately covers all critical system states so that the entire system can be tested successfully.
- Legislation and standardization: The industrial automation sector faces stricter and stricter legal regulations relating to the protection of human health and the environment. Moreover, it is necessary to realize that Industry 4.0 is not one standard but rather represents an entire group of standards, which are mostly still evolving. Reacting to current trends and requirements, Rockwell Automation, therefore, continues to evolve its Industry 4.0 concept called The Connected Enterprise. We offer our customers the latest connectivity options available to meet the most stringent reliability and security criteria.
Industry 4.0 brings many new fantastic opportunities, which would not be possible prior to full digitalization and the interconnection of company systems. On the other hand, it also brings new challenges, which need to be answered.