Lockout/Tagout Procedures: How Much Information is Too Much?
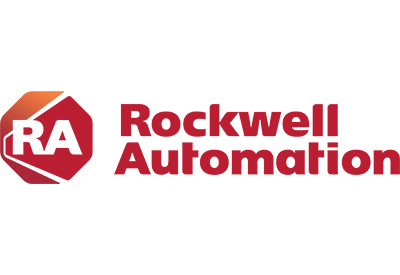
July 22, 2019
Lockout/tagout (LOTO) procedures are designed with the safety of maintenance professionals in mind – but they also consider the workers who are typically around and/or operating the machines. Because multiple audiences need to read procedures, it is important to be intentional about the information that is provided within each LOTO procedure, and how they are presented.
According to Occupational Safety and Health Administration (OSHA) regulation 1910.147, LOTO procedures “shall clearly and specifically outline the scope, purpose, authorization, rules, and techniques to be utilized for the control of hazardous energy, and the means to enforce compliance.” This means that each procedure should be clear and concise about the following things:
- Which piece of equipment the procedure pertains to
- Who is qualified and allowed to perform the lockout/tagout
- The steps to be taken to properly perform lockout/tagout
- What consequences there will be if someone does not follow the lockout/tagout procedure
These steps should include information about the type of energy, methods for controlling the energy, and methods for verifying the lockout.
Additions: Helpful or Unnecessary?
What else could be added to procedures to make them more helpful? Often, there may be an opportunity to add more information to the procedure than is required by OSHA 1910.147.
Sometimes these additions are helpful, making de-energization of a machine easier. But additions can also clutter the document, hindering clear understanding of the procedure. It is important to keep in mind who is going to be utilizing the procedures when deciding what information is necessary.
Examples of helpful additions:
- Steps that instruct the authorized user to confirm that a certain valve be opened or closed to release pressure from a system.
- Notes about associated equipment that must be shut off for the safety of the employee or system.
- Warnings about backup units that must be kept on, such as a backup pump, to ensure no interruption to normal plant operations.
- Other important warnings to ensure that nothing goes awry when lockout/tagout is being performed.
There are many different industries in which these additions can come into play. This could be a plastic forming facility in which there is a whole line of equipment that is interconnected. For example, if someone wanted to work on an extruder, then there might be a note on the procedure document to shut down the former that it is feeding as well as the blending unit that is supplying the extruder with plastic pellets. Another example would be in a dairy facility, where work may need to be done on a clean-in-place (CIP) pump. If this were the case, then there may be instructions to ensure that CIP system is rerouted to another CIP pump so that the process isn’t interrupted and everything can continue on smoothly.
Examples of unnecessary additions:
- Information not relevant for de-energizing a machine
- Information on how to service the equipment, which is better documented separately in a preventative maintenance work instruction
- To elaborate on instructions or explanations that can obscure critical information
- Putting every piece of information that may ever be desired on a LOTO procedure, “just in case,” instead of leveraging employee trainings or other methods
Lots of companies try to add extra information to their lockout/tagout procedures because they see it as being helpful and necessary, but this isn’t always the case. There have been instances when companies have attempted to include an Alternative De-energization Procedure (ADP) in their LOTO procedures.
If someone looked at this and attempted to follow the section detailing how to lockout a piece of equipment, they may get confused and follow the ADP instead. If this were to happen, then they could possibly be putting themselves in harm’s way as they have not fully locked out the equipment.
As you can see, some additions can start to cause clutter and make it harder for the authorized user to proceed through the proper steps to complete lockout/tagout. When too much information is included, it starts to become more of a hindrance than a help and can lead to an improper lockout or to users ignoring lockout/tagout procedures entirely. Even though there may be the best intentions by adding details, it can instead make lockout/tagout much more difficult, and potentially more dangerous, than it needs to be.
Procedure Documentation Types Should Vary
There isn’t one exact set standard for procedures, as they can vary depending on company and industry. OSHA allows freedom in the implementation of the procedure format as long as the regulation’s intent and minimum requirements are met. You may need to add small details that can make a LOTO procedure more specific and helpful. There are lots of different documentation formats that can be used for a LOTO procedure.
The way a procedure is documented can make a big difference to the person trying to carry it out correctly. The different types of procedure documentation will vary depending upon each company’s size and needs. When authorized employees are locking out equipment, especially complex pieces, it is generally recommended to utilize a graphical format. Graphical procedures tend to provide the clearest, most easily accessible and visually appealing guidance for employees, so as to not confuse or distract them from performing the lockout safely.
Are your lockout/tagout procedures as clear and effective as they can be? Do your procedures meet all the standards of OSHA 1910.147? Could you use some assistance with your lockout/tagout program? Learn more about the ways Safety Services from Rockwell Automation can help you with all things lockout/tagout.
Find out more HERE.