What You Need to Know to Work with a Collaborative Robot System
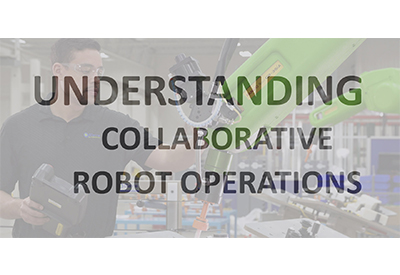
July 31, 2019
Collaborative robots, or cobots, have been creating a buzz in the automation world in recent years. Many believe there’s just one solution for a collaborative robot system – that being a specialized non-industrial robot. The good news is there’s actually a variety of options to achieve a collaborative system. In fact, most traditional robots can become “collaborative” with extra safety devices and proper integration. Let’s examine options for collaborative robot operations.
Cobots are able to operate in multiple ways. According to the ISO 10218-1 safety standard released in 2012, there are four different types of collaborative robot operation:
- Safety rated monitored stop
- Hand guiding
- Speed and separation monitoring
- Power and force limiting by inherent design.
The “safety rated monitored stop” collaborative robot operation does not allow robot motion when an operator is within the “collaborative workspace,” but the drives of the robot can maintain power. The collaborative workspace is the shared workspace where both the robot and operator can perform tasks. For this type of operation, a standard industrial robot can operate at high speeds while the collaborative workspace is clear of operators, allowing for faster cycle time. The robot is able to start back up automatically without direct input from an operator once the collaborative workspace is clear.
A common use of the safety rated monitored stop operation is a manual loading station. In this scenario, an operator can manually load a part to the robot’s tool, or a manual inspection station. This allows the operator to inspect parts periodically as the robot unloads them from a machine. To achieve these types of applications, light curtains and a safety pressure mat could replace a panel of fencing.
Here’s how it works: The robot presents the part to the operator. As the operator breaks the light curtain or steps on the mat, the robot holds at a zero speed. This allows the operator to perform the task safely. As soon as the operator walks away and clears the area, the robot automatically continues the process.
The “hand guiding” robot operation allows robot motion through the direct input of an operator from a hand-operated device. As an operator enters the collaborative workspace, the robot will stay in a safety rated monitored stop until the operator actuates the hand-guiding device through an enabling switch. Many times, these devices are used on robots as an intelligent lift assist device since they can be easier to maneuver than average lift assists, but can also operate autonomously when no operators are around. Hand guiding creates an easier way to jog a robot or teach a process.
The “speed and separation monitoring”, also commonly referred to as a “fenceless” robot system, is where both the robot and operator can move concurrently in the collaborative workspace as long as the operator maintains the pre-determined protective separation distance from the robot.
A safety rated laser area scanner typically monitors this type of collaborative application. If the operator breaches the separation distance, the robot will stop until the person moves away from the robot – once clear the robot can autonomously continue the process. The separation distance is determined through a calculation based off the speed of the robot, speed of the operator, and the response time of the system (both robot and safety devices). The faster the robot is moving, the larger the separation distance will need to be. The more frequently operators breach the separation distance, the more often the robot will be held at a zero speed.
The “power and force limiting by inherent design or control” collaborative operation requires a special robot designed to have power or force feedback built in, allowing it to detect contact with a person. This is the most popular type of robot collaboration, and is ideal for applications that require an operator to frequently be in the same workspace as the robot. It requires the most extensive risk assessment since the robot is able to continue with its task as an operator stays within reach of the robot. The maximum speed of the robot will also be less than a traditional robot.
Each of the four types of collaborative robot operation permit varying amounts of interaction between people and robots. Based on the risk assessment, each type will also allow you to remove a portion or all of the safety fencing. Determining the collaborative application that’s right for you requires evaluating the following:
- What amount of interaction will be required between your operator and the robot?
- If no direct interaction, how close will your operators need to be to the robot operation?
- How much floor space is available?
- Is the application hazardous?
- What is your cycle time requirement?
It’s likely that more than one type of collaborative robot operation can be used in a system, even in combination with traditional safety fencing. No matter what type of operation is used – think safety first and you’ll be on your way to a successful collaborative robot application!