Industry Insights with Owen and Richard Krawczyk of Pepperl+Fuchs, Talking Factory Automation
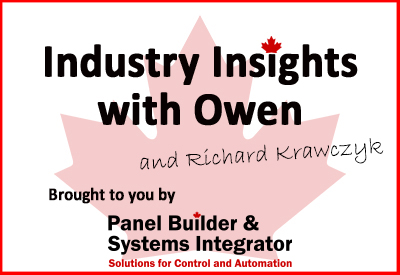
August 13, 2019
By Owen Hurst
In this issue of Industry Insights with Owen we discuss factory automation solutions and concerns with Richard Krawczyk, Account Manager of Factory Automation in Canada for Pepperl+Fuchs. Earlier this summer I met with Richard in Southern Ontario to tour the Pepperl+Fuchs mobile exhibit(read the article on the mobile exhibit HERE), and after some interesting discussion we wanted to be sure we shared some of the interesting points of conversation and the depth of knowledge Richard has acquired with our readers. Richard has been with Pepperl+Fuchs for over 20 years and is certainly a product expert in the area of factory automation and its implementation within Canada.
With over 20 years experience working for Pepperl+Fuchs what has been the biggest shift you have seen in terms of manufacturing automation within Canada?
The biggest shift I’ve seen in the last 20 years is the integration of vision technology in manufacturing. The first vision system I saw was 19 years ago. It had limited functionality, a steep learning curve and high cost. By comparison, the vision systems of today have significantly more capabilities, are less complex to set up, are less expensive than their original counterparts and have become an integral part of many error proofing solutions. That being said, there are still many challenges with vision technology. Lighting and varying object colours and contrasts continue to pose problems for this technology. Pepperl+Fuchs has recently addressed these issues with the introduction of our SmartRunner series of vision based laser line profiling sensors. These sensors are highly immune to the effects of external lighting and offer reliable contour matching capabilities independent of variations in object colour and contrast. With simple push-button teach and free software for fine tuning the application set-up, these sensors offer highly reliable and easily integrated vision based object profile matching capabilities for a fraction of the cost of traditional vision based solutions.
In your opinion how has the progression of automation into manufacturing in Canada compared with other countries/regions?
My initial response to this question is to channel Meryl Streep’s character from The Devil Wears Prada: “By all means, move at a glacial pace”. The reality is, Canadian manufacturers are moving at a dismally slow pace when it comes to adopting new technology. 20 years ago, our skilled labor force and level of automation were far superior to many developing countries who were competitive due to low cost, unskilled labor. That is no longer the case. Here in Canada, the adoption rate of new technology has stagnated while countries like China have surpassed our level of automation in many sectors. It used to be, when we brought out new technology products, they were adopted first in Europe and the US, with Canadians adopting much later. Today, countries like China and Brazil are among the early adopters while Canadians continue to sit on the fence, waiting to ensure the risk of adoption is low and ROI guaranteed.
How has the perception of machine safety in the workplace changed over the last 20 years?
20 years ago safety was an after-thought in machine design. Once the design was complete, safety audits were done to determine what guarding was needed and it was added as the final piece of the build. Physical guarding was used extensively to isolate the people from the machines/robots. With the increasing use of cooperative robotics, AGV’s, etc., where humans interact directly with the automated machinery, safety needs to be a fundamental part of the initial design. Physical guarding can no longer be utilized as the primary protection method, so the equipment design must utilize safety feedback and monitoring sensors to ensure the position of the machinery and personnel are known at all times and everything functions in a safe, friendly manner.
With more and more motion technology being implemented what is the biggest challenge for sensor and safety technology?
With cooperative robotics, there is no longer a specific, rigidly defined safe zone. The workers interact directly with the moving machinery. You can no longer just mount a light curtain and have the machinery stop when the beam is interrupted. Many of the safety sensors of the past are no longer relevant in these new designs. Safety sensors need to be able to monitor an entire area and provide feedback on the rate of safe motion that can currently occur in each direction of movement. This is creating the need for further development of 3D safety sensors.
Integrated and connected sensors offer enhanced machine and operator safety but concern still exists regarding the cybersecurity of connected devices. How has Pepperl+Fuchs addressed this concern?
IIoT and Cybersecurity are top priorities for Pepperl+Fuchs, and we have been taking a leadership role in IIoT developments for many years now. Pepperl+Fuchs was the first IO-Link member company and Pepperl+Fuchs Comtrol is currently North America’s designated IO-Link Competency Center. Additionally, our Neoception Cloud Services business unit has completed numerous projects integrating our products/technologies into fully deployed turn-key Cloud applications. With a long history of developing and deploying these solutions, Pepperl+Fuchs has acquired the knowledge and expertise to develop products and implement secure IIoT applications. One example of this is our Pepperl+Fuchs Comtrol IO-Link Master blocks. They are the world’s FIRST true IIoT IO-Link blocks in that they DO NOT require a PLC/Host Controller connection. With MultiLink capability supporting up to 5 independent OPC UA connections, these blocks, and their associated IO-link IO products, can be installed on equipment and linked to a Cloud service, ERP system, etc., for real-time monitoring while maintaining 100% isolation from the equipment’s existing controller and control systems. This is a first-of-its-kind product that will allow manufacturers to deploy fully isolated IIoT equipment upgrades in a secure method without interfering with their legacy control systems. In my opinion, this is a true game changer that can help many companies that have been hesitant to implement IIoT upgrades due to very real and existent cybersecurity