Breaking the Digital Transformation Log Jam in Manufacturing
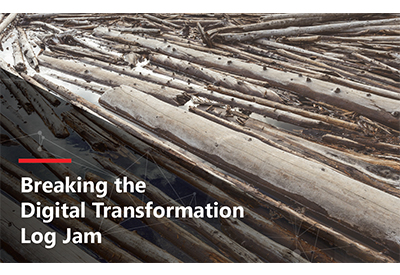
August 19, 2019
By John Southcott
Digital transformation is top of mind for business leaders, solutions providers and consultants these days. The multi-trillion-dollar predictions on everything from IOT to AI/Machine Learning are indeed staggering to think about. That said, when it comes to manufacturing systems our recent experience suggests that organizations are still cautious when it comes to investment and taking their first steps into the digital world. In many cases, the business value is being questioned. Yet in other industries, or indeed in other functions of the manufacturing business, it appears its full steam ahead.
At Brock Solutions we have done numerous “get started on the digital journey” consulting engagements for manufacturing companies with the following attributes:
- Their existing Manufacturing Execution System is a combination of excel, Access databases, tribal knowledge and custom systems
- Real-time operational systems and visibility into manufacturing operations is required to take advantage of significant market opportunity
- Serious risk of business interruption if systems fail or key people leave/retire
Yet after completing the engagement, we have experienced some organizations putting their digital journey in manufacturing systems on hold even though the project was well received, and the client feedback was that the process was valuable.
Why is that? When we ask our clients to reflect on that question, a few common themes emerge:
- Competing Initiatives. ERP, SCM, CRM, PLM projects that are underway and already funded often consume the resources required to transform manufacturing operations
- Competition for Capital. New facilities, new lines, new equipment that have more visible payback often take priority
- Elusive Business Case. Often it is difficult to pin down an aligned business case and cost certainty. Technology in and of itself does not drive value. It is the combination of people, process and technology that drive measurable benefits. So, the true business value of going digital in manufacturing is difficult to derive. Also, many of our clients are wary of large-scale transformation programs based on their experience with other technology deployments
- Lack of Buy in from Operations. The very people that this is supposed to benefit often resist change even though there is agreement that the status quo is not sustainable
I find the last point intriguing. So, I reached out to a colleague who is the VP Operations for a large consumer products company who has had success going digital with his organization. I asked him to share the secret sauce, and his answer was quite insightful and in fact had nothing to do with technology.
He told me that there were two things I needed to recognize about the manufacturing world:
- People are trained not to fail, versus trained to win. It’s how they are wired!
- An incremental approach to change is preferred over step function
Yet there is unanimous agreement that it isn’t “if” but “how” and when to get started on the digital journey.
Based on the voice of our customers and our own experience, we have some thoughts to share about how to break the log jam.
Education, Knowledge and Alignment
The manufacturing digital journey will go nowhere fast if the various constituents responsible don’t know what the technology is capable of, where it has been deployed successfully and what the organization’s priorities are. Unlike ERP systems which generally speaking have a common definition, manufacturing systems do not. For example, MES (manufacturing execution systems) is defined differently depending on the industry and in some cases differently by company. We recommend that our clients:
- Spend time getting themselves educated on what these systems are capable of. Solution provider conferences, organizations like MESA and industry analysts such as Gartner are good sources
- Reach out to organizations who are on the digital journey. Do a site visit if possible. Learning from their experiences, both good and bad, are invaluable lessons
- Establish a governance process to oversee the program and execute projects. An executive steering committee providing broad based direction and timely decision making along with an empowered core team of representatives across key functions responsible for day-to-day project execution is best practice in our experience
Roadmap with Measurable Gains
We think it is important to have a long-term vision that guides the organization through the digital transformation process. That said, we also know that it is unacceptable to have long, drawn out implementation projects that take too long to deliver value. In our experience best practice is to establish an aligned, flexible strategy made up of a series of initiatives that move the organization forward with measurable gains that fit together. We purposely avoid the term “Pilot” because there is a risk of implementing solution(s) in isolation without considering the bigger picture.
Adopt a Continuous Improvement Culture
The VP operations referred to earlier was emphatic that culture change is table stakes for successful digitization of the manufacturing function. Unless there is a concerted effort to change the culture from “run to fail” to continuous improvement, value capture will likely not meet expectations. It starts at the top – a strong executive sponsor willing to drive change and remove barriers is critical for breaking the digital log jam in manufacturing.