Under a Watchful AI: Discover Production Problems Early with Embedded Analytics
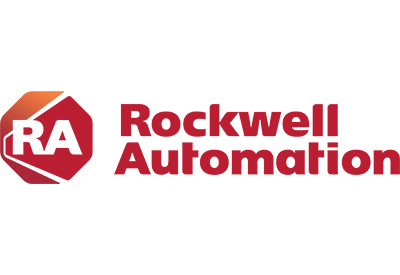
August 27, 2019
By Jonathan Wise
What if your control system could do the job of a data scientist?
It might help your HR department breathe easier, given the demand for the data science skill set. It could also give you faster access to information needed to make production improvements. Today, data scientists spend much of their time cleaning and organizing data – work that technology can automate in some cases.
Most importantly, it could help your workers more proactively solve the problems that disrupt your processes, cause downtime and affect product quality.
Our newest embedded analytics technology that plugs right into your control chassis makes this possible. With it, you can start creating models and getting predicted values related to production without needing a data scientist.
Making Analytics More Accessible
A predictive analytics module won’t give you instant predictive analytics. But it dramatically reduces the work and skill set you need to create them.
Today, many analytics technologies require that you have deep expertise in both data science and your industrial process. Embedded predictive analytics uses automated machine learning to do data science.
Here’s how it works. First, a controls engineer or another application expert configures the module to identify what aspect of your process you want to predict and what data is needed to do so. Then, the module starts collecting controller data and building predictive models related to your application.
After an initial training period, the module can start monitoring your application. Based upon the predictions, human-machine interface (HMI) dashboard alarming can be leveraged for further notification.
Use Cases
You can use embedded predictive analytics in two key ways to enhance your operations:
1. Anomaly Detection: When we surveyed industrial companies around the world about their digital initiatives, their top goal, by far, was to increase operational efficiency. One way you can do this is by using predictive analytics to find issues early, before they impact your operations.
Embedded predictive analytics can detect operational anomalies and notify workers so they can investigate or intervene before the anomaly leads to process or quality problems.
For instance, workers could get an advance heads-up that quality on a production line is starting to move out of tolerance. They could learn that a boiler temperature is dropping because of an abnormality that needs to be addressed. Or they could see that a mixer is starting to deviate from its temperature set point and could soon impact product quality. The possibilities are endless.
2. Virtual Sensor: When you use embedded analytics as a virtual or “soft” sensor, you’re using data from other points in your process to estimate another value. This can help you get virtual measurements that may otherwise require expensive instruments or manual readings to determine.
For example, if you’re producing breakfast bars in your plant, it might be unfeasible to take a reading of a packaged product’s humidity. Or, it might be too wasteful from a scrap and labor standpoint to have workers manually pull and open products to check their humidity.
Used as a virtual sensor, embedded analytics can use other variables – like oven and sprayer data – to virtually estimate a finished product’s humidity.
Another Tool in Your Toolbox
Embedded predictive analytics are the latest addition to the larger portfolio of scalable analytics solutions that you can deploy in your operations.