How to Avoid a Shocking End: Protecting Workers From Injury
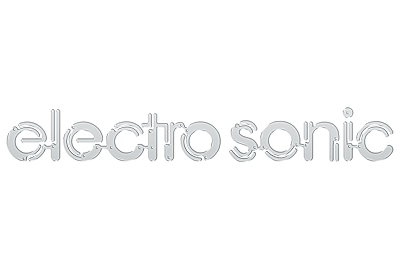
August 27, 2019
Do you know the first question you should ask before opening an electrical enclosure? Plant managers, building maintenance staff and electrical repair personnel repeat the question “Is it safe?” so often that it’s practically a mantra. And rightfully so. The people in these professions are constantly at risk of experiencing a life-threatening current while on the job. They regularly take precautions such as removing their wedding bands and must be vigilant in checking and rechecking for telltale signs such as alerting lights and sounds—all in the hope of returning home safe and sound at the end of their shifts.
The rates of accidental injury or fatality related to the risks of voltage testing in industry. (Image courtesy of Panduit.)
According to Panduit, 18.3 percent of facilities surveyed reported that personal injuries occurred when a worker was using a handheld voltage test instrument. The risk associated with voltage testing should not be ignored, especially when the rate of “near misses” is 36.7 percent.
Companies and agencies have developed processes to help ensure worker safety around live wires. Most commonly these processes include protocols such as the lockout-tagout (LOTO) method. In fact, some jurisdictions in the United States and Canada require the implementation of the LOTO method whenever workers are dealing with heavy, hazardous machinery during repair or maintenance. While LOTO works to represent that voltage testing has taken place and that machinery is safe to work with, there are cases where the LOTO protocol failed (sometimes due to criminal negligence).
The network infrastructure and electrical wiring company Panduit, based in the United States, claims to have simplified matters by creating a device that can be installed in the enclosure and, with a simple red or green indicator light, shows if it is safe for workers to proceed.
Voltage Indicators
A voltage indicator is a tool used by workers to check to see if it is safe to touch or be near electrical equipment. These tools can indicate the hazardous presence of voltage and alert workers if there is. However, these tools cannot verify if the equipment has been de-energized. To have the ability to confirm that the equipment has been de-energized, such a tool or device would need to be able to be grounded. If equipment cannot be de-energized—or it cannot be verified that it has been grounded—then there is a risk for workers on such equipment.
Voltage Testers
The reason that indicators are necessary is that the devices known as voltage testers aren’t able to warn of the presence of hazardous voltages unless a test has been run. This means that if a worker runs such a test and there is a hazardous voltage, the worker will be exposed to injury in the time before they can run the test. It would be helpful if there were a device on the machine that could alert workers to the presence of hazardous voltages.
Moreover, voltage testers are often portable. This means that they too are not often grounded while they are being used and so are also unable to verify if a process of de-energizing has taken place on electrical equipment. Just because electrical machinery has been turned off, that doesn’t mean that DC voltages aren’t lingering in some way; a possibly harmful static charge could even have been built up in the machinery without a ground. Developing a sensor that would be able confirm to workers if the ground is working properly and is properly de-energizing the machinery could make strides toward worker safety. This could decrease the rate of worker injuries as well as decrease the occurrences of delays in workshops or manufacturing floors.
How AVT Works as a Tester and an Indicator
So why not combine voltage testers, voltage indicators and grounding, and develop a simple method of alerting workers to the safety of their surroundings that is integrated directly into machinery or electrical equipment? This is precisely what Panduit has done with its VeriSafe Absence of Voltage Tester (AVT).
The way the device works is simple. The interface for the AVT—the indicator module—has a button to interact with, and an array of LEDs using red, yellow and green to represent how safe the equipment is. Red for not safe. Yellow for a test that cannot confirm the safety of equipment or that should be retested. Green for confirmed an unhazardous presence of voltage and that the equipment has been de-energized. The indicator module is usually installed into the door of a panel that accesses the electrical equipment.
Tests can be run by simply clicking the button on the front of the device. The absence of any LED light being alit doesn’t necessarily mean that the equipment has been de-energized and suggests that a test should be run. If a hazardous voltage is present, the red LED will be alit without the need for a worker to run a test: this would alert them that the equipment or panel is not safe to work with and should be turned off and de-energized in some capacity.
The way that the indicator module knows which LED to activate is where the tests take place: in the isolation module. The isolation module has four leading wires running from it. Two are integrated into the electrical equipment itself at two distinct junctions with the main power lead. This will test for any presence of hazardous voltages, including those that residually remain even after equipment has been turned off. The other two leads act as grounds, allowing for proper de-energization.
Between the indicator and isolation module, the AVT runs as a voltage indicator (by showing a red light whenever there is hazardous voltage), a tester (through the sensor leads that test for residual voltages), and a ground (through the ground leads). Not only does this simplify the process of checking for hazardous voltages, but it also makes it safer and is reliable. The AVT brings together the necessary features of indicators, testers and grounds.
What’s in the Box and the Installation Process
Installation is relatively easy. As mentioned, both the sensor feeds and the ground feeds must be separated from one another. Otherwise, the indicator can become confused and will continue to ask to be tested—never being able to indicate if the equipment is safe or not. Attach the sensor feeds to where a worker would usually test for voltage. The isolation module can be installed onto a rack within the panel. The indicator module can be installed into the door, so that it is accessible from the outside.
Saving Lives
One of the main advantages of installed detectors versus portable ones is that they decrease the opportunity for hazardous voltages to injure workers. Even after going through a LOTO process, there is still a risk that lingering voltages can remain in equipment and can harm workers. The AVT works to ensure that workers know more about their surroundings to protect their health.