One Smart Path to Extraordinary Machine Flexibility
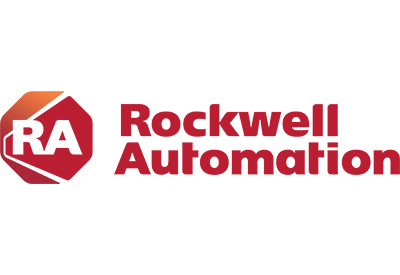
September 5, 2019
By Steve Mulder
It’s no secret. Machine builders today are under significant pressure to deliver equipment that can meet the demands of flexible manufacturing. Those who supply consumer packaged goods (CPG) companies are especially challenged to deliver future-proof designs that optimize changeover today – and ramp up rapidly for new SKUs not yet imagined.
Until recently, machine builders had little choice regarding how they delivered equipment to the factory floor. Typically, any CPG manufacturing or packaging application was comprised of a series of essentially standalone machines that were integrated to complete the line.
That legacy remains on many plant floors today. Often characterized by static mechanical parts, friction-based conveyance, and a plethora of disparate, ancillary equipment, these lines may achieve impressive throughput running uniform product based on fixed variables.
But machine flexibility is often compromised. Complex mechanical adjustments and equipment synchronization take time. And time is at a premium on any plant floor – especially when a product launch is at stake.
Changing the Equation with Advanced Technology
With advances in technology, OEMs now have a better way to meet the demands of manufacturers for more flexibility. Specifically, three key mechatronic technologies are changing the equation for OEMs and the customers they serve.
First, robotics is finding its way into more CPG applications than ever. Robots are intrinsically flexible, thanks to their ability to operate fully in three dimensions, determine appropriate paths without mechanical rerouting – and address infinitely variable product shapes and sizes.
Secondly, linear motor technology – and notably, independent cart technology (ICT) – boost machine response to a diverse product mix. Unlike conventional conveyance that advances product on a preconfigured path at fixed speed, ICT intelligently moves products as operations are completed.
And finally, automated changeover, which minimizes the need for manual intervention and facilitates machine setup for a new product or packaging configuration from the operator interface. New servo drive functionality is making this option even more cost-effective.
In addition to enabling more machine flexibility, advanced technologies also allow OEMs to do more with less equipment – and in less space. In fact, more machine builders are delivering compact solutions that combine once distinct operations, like filling and cartoning, into a unified offering.
But without careful planning, disparate control systems could still limit success.
Bringing It Together: Unified Machine Control
For OEMs, the critical question is not only which technologies are most appropriate for the application, but also how best to integrate those technologies into the machine and plant architecture.
Not so long ago, machine builders had little choice. Advanced technologies sourced from third party suppliers typically came equipped with proprietary control systems. As a result, machine coordination relied on the challenging integration of multiple disparate systems.
For the OEM, this scenario adds complexity at every stage of a machine’s lifecycle. Design efficiency is difficult to achieve and customer support is more challenging when staff must master multiple systems. Performance gains may be elusive when communication lags and synchronization stand in the way.
Today there’s a better way, thanks to advances in programmable automation controllers (PACs). Enhanced processor speeds and performance now available in the latest PACs means machine builders can take a unified approach to machine control.
Advanced technologies like robotics, ICT and automated changeover systems can now run on the standard PACs that run the rest of the machine. One controller. One design environment.
Unified machine control allows OEMs to more easily integrate, control and coordinate advanced technologies. And it also simplifies machine operation and maintenance for the end user, who must only understand and support one system.
Robust Data Integration. Meaningful Information.
But unified machine control does more. A machine built on a unified control platform also provides one unified source for information generated by that machine – and places OEMs in a much better position to deliver that information in a meaningful way.
Unified machine control provides an excellent foundation for visualization, reporting and analytics solutions to help monitor the key factors affecting performance, efficiency and quality.
Simply put, unified machine control enables OEMs to create smarter equipment that more easily integrates into a facility – and provides access to information that allows end users to better respond to changing market demands.