Delicious Data: How Predictive Analytics Improves Efficiency
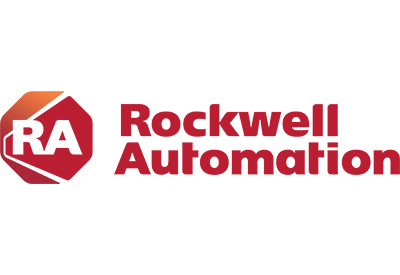
September 23, 2019
By Cory Garlick
It’s never been a better time to be a consumer, especially when it comes to food and beverage options. Do you want organic, locally sourced, craft made, single serving, gluten free? The choices are endless, making you a happy consumer, and at the same time, a frustrated producer.
Today, food and beverage companies are faced with many challenges. Profitability is impacted as raw material costs rise and the cost of maintaining aging infrastructure increases. At the same time, they are experiencing inefficiencies as changeovers increase to keep up with the constant change in consumer demand.
So what’s the best way to address these competing challenges? Here’s how data harnessed by machine learning and predictive analytics can help you make informed decisions to increase efficiency.
Use Your Machine Data – Wisely
The great news is the data already exists. While new equipment can be designed “smart” to deliver data, there are ways to get data from older equipment too. It’s available through technology implemented over the past decades including sensors, components, PLCs, drives, historians, databases, HMIs, etc.
But here’s the reality. Most facilities are more than 20 years old, made up of individual cells or lines acquired over time. While under the same roof, the lack of connectivity between disparate islands of technology makes it nearly impossible to assess the overall productivity story. Instead of machine learning, operators rely on personal experience to make decisions, an increasingly dangerous formula as more and more workers retire.
Having the data isn’t enough, of course. Accessing it takes the right infrastructure, and using it to drive improvement takes advanced technology like predictive analytics. Of the companies accessing data, only 25 percent are using it for proactive purposes. This is equivalent to driving a car based on what you see in the rearview mirror.
Moving from where you are today to an integrated, data-driven operation will not happen overnight. Many companies have teams exploring Industry 4.0, smart manufacturing and other factory of the future concepts, looking for ways to apply technology for greater productivity.
Transform Your Infrastructure
Successful food and beverage producers are identifying use cases, conducting pilots, implementing technology on a single cell, process or line to prove out the ROI, and then determining how to scale across the operation and enterprise. And they’re seeing significant results.
For instance, Agropur Dairy Cooperative started with one of its milk processing plants, looking to create new access to disparate data, so facility operators could make informed decisions. With advanced technology, they not only eliminated 2,500 hours of manual data collection each year, but quickly saw a 30 percent reduction in lube consumption and a 25 percent efficiency gain.
Similarly, Kraft Heinz started small to prove out the concept on a line at its Ore-Ida plant. This decades old potato processing line had aging controls and relied on the knowledge of operators to optimize settings and troubleshoot. Through the use of technology upgrades that included predictive analytics, they realized a 10 percent capacity increase on the pilot line and an ROI in under 12 months.
More importantly, the data to make this improvement was always there, it was just inaccessible nor being leveraged without the right machine learning infrastructure.
Finally, we worked with Jim Beam to increase bourbon production at one of its distilleries by one liter per minute. Again, the opportunity was always there, hidden in the data. The use of analytics allowed them to understand where they could drive production capacity in the proofing stage. They were able to drive a 60 percent reduction in variability that lead to this significant increase in capacity.
Turn Data to Insights
Avoid analysis paralysis and getting swamped by all of the data. Chances are, you have a sense of where your inefficiencies lie. Look at what part of the process has the highest input cost, greatest impact on profitability or most recurring issues.
That’s where you should start. If you can improve yield from the highest cost components into your finished products, that’s pure profitability. What needs to happen within an identified part of the process is where predictive analytics can help you focus, and where technology can drive real-time productivity.
It’s not as difficult or costly as it may sound. Projects can be easy and cost-effective to implement with a partner that intimately understands the IT and OT environments.
Pilot projects can be done with minimal disruption to operations. This approach typically leads to a rapid and positive ROI, creating the use case you need to scale throughout your food and beverage operations, and to begin to realize the productivity improvements lying just beneath the surface.