Eight questions to ask yourself when deciding between RFID and barcode reading for traceability
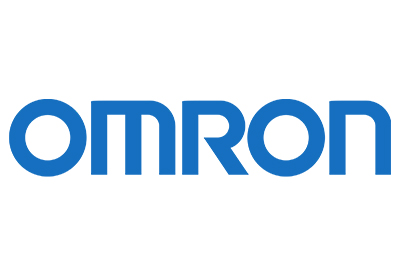
September 23, 2019
Both radio-frequency identification (RFID) and barcode reading are excellent options for traceability, and it can be difficult to choose between the two if you’re not fully aware of their relative advantages. To help you make an educated decision, we decided to put together a quick questionnaire on the topic.
1. Do you need to update information during processes?
Unlike the direct part marks (DPMs) and printed labels that provide a substrate for barcodes, RFID tags allow you to write information as well as read it. If you need to update part-specific information on a data carrier during production as part of your traceability system, you might want to consider RFID.
For example, an RFID reader/writer can be extremely helpful in gathering data for process optimization. You can record the starting and finishing timestamps of each production step into the RFID tag attached to each work-in-progress (WIP) and send this information to a production database to map out where the bottlenecks are.
Similarly, if you have several different tools that perform the same function and you’d like to see which one performs best, you can record which particular tool was used for a given production step into the RFID tag along with production test results. This allows you to visualize quality trends for thousands of parts for a given tool or step in the production process.
2. Would it help to have a data capture method that doesn’t require line of sight?
When reading barcodes – either in DPM form or on a label – you can’t have anything standing between the symbol and the reader. RFID systems give you much more freedom. As long as the obstructing object isn’t made of metal and doesn’t have a high level of water content, RFID can read right through it.
For example, during a machining step, it might be necessary (or at least expedient) to position the tracked object in such a way that another object comes in front of the reader. You’d either need to shift the part’s (or blocking object’s) position, provide a fixture to assist with barcode readability, use multiple readers, or alternatively use RFID to boost your operational flexibility.
3. Do you need an extremely long read range?
Although barcode imager read ranges have been steadily rising (in part thanks to advancements in Omron’s MicroHAWK ID family), they still hover around a meter or so at the maximum. Many UHF-style RFID readers, on the other hand, can successfully gather data from tags that are positioned up to six meters away, depending on RFID and antenna tag performance.
4. Do you need to include very large amounts of data per item?
If you need to store large amounts of data for each WIP, then it might be worthwhile to invest in RFID. It’s common for RFID tags to accommodate up to eight kilobytes of data. If you won’t be needing more than 1.6 kilobytes per item, then you might be better off using DataMatrix codes and barcode readers.
5. Do you need to read data from multiple items at once?
If capturing data from multiple WIPs simultaneously is a deciding factor, then RFID might be for you. RFID reader/writers can read dozens – or sometimes even hundreds – of tags in a single swoop. Barcode imagers, on the other hand, are limited by the camera’s field of view, meaning that only a few barcodes can generally be read by a single device.
6. Is contamination with oil and/or dirt likely to occur in your facility?
One of the most significant advantages of RFID is that it continues working even when there’s a coating of oil and/or dirt on the tag. This makes it excellent for the harsh environments typical of automotive applications.
When barcodes are covered in grease and grime, they can be exceedingly difficult or even impossible to read depending on how much of the symbol has been obstructed. That said, the combination of redundancy built into the symbols and powerful decoding algorithms like Omron’s X-Mode can go a long way in reconstructing damaged codes.
7. Do you have budgetary constraints, and if so, could your process reuse RFID tags?
One major downside of RFID is that the tags can be relatively expensive compared to barcodes printed on labels. They can run anywhere from $1-$30 per tag, whereas the cost of a printed label is negligible. DPM costs are also quite low, although a laser marker investment is significant.
RFID costs can be mitigated by putting the tags onto reusable containers, and this strategy can lower the cost of using the tag to just fractions of a cent each time. The durability of RFID tags makes them particularly apt for reuse, and Omron’s tags can be used thousands of times for several years – or even a thousand times per day.
8. Do you need to visually inspect each part?
If you want to take care of traceability and inspection tasks in one fell swoop, then you’ll want to invest in a smart camera – such as Omron’s MicroHAWK MV Series or FHV7 – that can analyze images to read barcodes, perform pattern recognition, verify that colors are correct, and do anything else necessary for a comprehensive quality inspection. These things can’t be done with an RFID system.