Energy Distribution Without A Control Cabinet
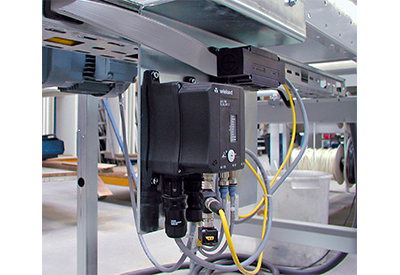
October 8, 2019
THREE QUESTIONS FOR MEINRAD BRAUN, PRODUCT MANAGER POWER BUS SYSTEMS FOR INDUSTRY AT WIELAND ELECTRIC
Mr. Braun, the major trends in machine building are digitization, modularization, and decentralization. What role does installation without a control cabinet play in this?
Installation without a control cabinet makes sense anywhere where equipment or drives have to be supplied with energy, or signals have to be transmitted and processed, over long distances. It is particularly suited to large machines and systems and can be used anywhere where cabling from the central control cabinet to the field can sensibly be replaced with power bus solutions and fieldbus communication. But this is not about turning one cabinet into many small cabinets with the same functions; instead the idea is to create greater benefit by adding more functions to the components. A good example here is on-site diagnostics. If a decentralized motor starter has an operating status indicator, it is possible to identify immediately on-site what is or is not happening in this branch if a fault occurs. Consequently, there is no longer any running back and forth between the control cabinet and the location of the fault. Instead the fault can be rectified quickly and the system is back up and running in no time.
Where specifically can decentralized installation be used, and what are the benefits?
One field of application would be logistics, where plants transport goods over hundreds of meters or even kilometers. Here the individual drives also have to be supplied with electrical energy. If this is realized with a central control cabinet, then not only unimaginable quantities of cables but also huge cable trays are required, increasingly turning the electrical installation into an intolerable mess of materials. The same applies to factory automation, especially supplies to production cells. Here too a large number of appliances have to be connected over large distances. On the basis of a power bus system, the work involved at central control cabinets can be reduced to the main distribution. This saves on costs and makes the planning for the plant more flexible because fewer control cabinets need to be considered. Secondly, the flat cable system offers the advantage that the taps for the drives can be positioned flexibly. Incidentally, the same also applies to the feed-in point in order to balance out the load on the power bus. As a result, the power load on the cable can be utilized fully while preventing any overload. Compared with traditional point-to-point cabling with terminal boxes, this type of installation is less prone to errors and much easier and faster to install. Its strengths are also evident when it comes to modifications. No cabling is required as the power bus is already there. In addition, the connection is established without baring and stripping but with insulation-piercing contacts. The whole process couldn’t be faster.
What solutions does Wieland provide for energy distribution without a control cabinet, and how does the cost work out compared with conventional installations?
We are very clearly laying the foundations here with our podis® power bus system. Alongside the components for decentralized 400 V structures, we are drawing attention again to 24 V distribution this year. To this end, we have included a powerful, decentralized power supply unit and branches with overcurrent protection in the portfolio. These components enable us to offer our customers the advantages of decentralized energy distribution for extra-low-voltage networks as well. The same applications are the reason for this endeavor too, namely machines and plants that span large distances, such as those found in logistics centers and factory automation. While it may be true that the material costs of the decentralized system are slightly higher than those of standard components, the pay-back occurs as early as the installation process. For one thing, this takes just a fraction of the time. As we show in this video comparison, it takes just a tenth to a third of the time to realize the same installation with the podis® system and with no mixed-up cables, open contact points, or cut insulation. Added to that, it is the modular design and decentralized structure that make it possible to adapt plants to new requirements time and again over their operating lifecycle, to keep the plant’s availability high, and thereby to improve productivity. It is not so much the procurement price that is important; the decision on an investment comes down to productivity.
Find out more at www.wieland-electric.com.