The four most common problems we find when conducting machine safety risk assessments
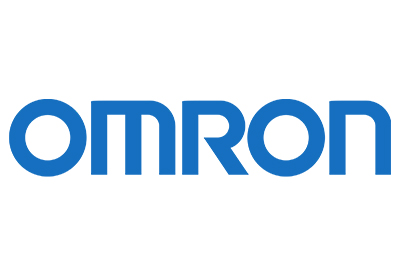
October 18, 2019
As a company that regularly conducts thorough machine safety risk assessments, we’re passionate about making sure our customers are fully aware of the regulations and best practices that are essential for keeping their teams safe. That’s why we decided to create a post around the most common safety violations we find during our assessments.
1. Incorrect machine guarding at pinch points, or no machine guarding at all.
We frequently run into scenarios where hazardous machinery contains little to no guarding. This is usually due to poorly designed safeguarding equipment that significantly interferes with the task of operating the machine. When the safeguarding structures become an impediment to doing the job, operators sometimes disable them or remove them altogether.
An example would be a hinged guard that needs to be opened every time an operator needs to take a part out of a machine. If the operator needs to do this every few minutes and the machine needs to be restarted after the guard door is shut, the safety feature becomes a major hassle and the operator may look for a way to bypass it.
In these scenarios, it’s essential to determine the reasons behind the disabling of safety features and look for a way to design new safety features that don’t interfere with the task at hand. We also recommend using a Gotcha Stick to check if hard guarding is compliant by measuring its distance from the danger area relative to the diameter of its opening.
2. Safety systems that aren’t control reliable.
In order to get compliance for a high-risk machine, the safety system must be control reliable. This means that their need be multiple contacts that are continuously monitored, and that the contacts fail to the OFF condition – i.e., they “fail to safe.”
The degree of redundancy and monitoring for the controls must be appropriate for the level of risk being assessed. A safety interlock switch, for example, must be wired back to a safety relay or safety PLC that will in turn tell the system whether the machine is in a safe condition or not. If one of the contacts fails, the safety PLC will tell the machine not to run.
A common issue we find with high-risk machines is that the light curtains and interlock switches are connected to a regular PLC or relay, rather than a PLC or relay that’s part of the safety system. Standards mandate connections to safety-specific equipment that monitors the overall application and feeds back into machine control.
3. Non-compliant E-Stop buttons.
E-Stop buttons are an essential component of a safety system, as they provide a quick, surefire way to shut down a hazardous machine in an emergency. Due to their great importance, these buttons are required to meet strict guidelines that ensure standard functionality in addition to a recognizable look and feel.
According to standards, an E-Stop button must be colored red and mounted above a yellow background in an easily accessible location. It must be a pushbutton, and it can’t be flush with the background material. Basically, it needs to be easy to see, easy to get to, and easy to push. There also needs to be no automatic reset, meaning that it can only be reset manually.
Unfortunately, Omron sees noncompliant E-Stops quite frequently. There are two main reasons for this: 1) a general lack of knowledge of the requirements for these buttons, and 2) a desire to prevent the E-Stop from being pushed too frequently in non-emergency situations. Although having everything shut down unnecessarily is frustrating, accessible E-Stops are still a safety necessity.
In addition, we sometimes find E-Stops that are being used for routine machine shutdowns, which is also a standards violation. The reason to avoid using E-Stops for anything besides emergencies is that repeated use can wear out the button’s contacts. Since it’s such a critical device, it’s important to extend its life as long as possible.
4. No way to lock out hazardous energy sources while doing machine maintenance.
Machine maintenance can be dangerous if there’s a possibility of the machine turning on while you’re working on it. Imagine that you’re about to put your hand into a garbage disposal to grab a valuable item that just fell in. If you knew that an accidental flip of a switch could turn the thing on, would you do it? You’d at least think twice.
Same thing with industrial machinery – maintenance workers need to be sure that any sources of electrical, pneumatic or hydraulic power are completely locked out while they complete their job. Grisly accidents could happen if someone elsewhere in the facility accidentally turned on the power source.
We sometimes see facilities that fail to have the proper means of locking these energy sources out. The appropriate retrofit device depends on the type of power. For pneumatics, there’s an energy isolation valve with a bleeder to dissipate the energy and let the air out. For electrical energy, there’s usually a panel with a big switch or a breaker. Both must only be lockable in the OFF position.