The Benefits of Remote Support for Manufacturers
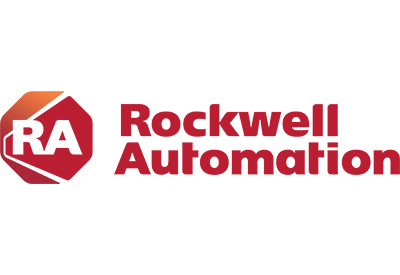
October 22, 2019
By Jessica Wiant
Plant managers and technicians have their hands full – not only are they responsible for ensuring day-to-day operations are status quo, they are also tasked with helping to increase production and revenue. So when problems come up, as they inevitably do, there’s nothing like knowing you’ve got back-up at the ready, 24-7.
From red RDS server icons and wire-framing data to HMI project disappearances and trouble getting online with your PLC, there are plenty of problems that need to be dealt with in a timely manner to avoid downtime and production delays. Even if they aren’t considered “critical,” the sooner any nuisance can be resolved, the better for everyone.
Plant managers can’t be everywhere, all of the time. But in many ways, they need to be. Today’s manufacturing plants are more productive than ever, often running continuously. That means someone needs to be watching, all the time – when they are at their kid’s evening soccer game, when they’re visiting friends on the weekend, and even when they are sleeping.
Because of the industrial skills gap, it’s become difficult for many manufacturers to hire staff in the numbers and skill sets they need. Some plant managers simply don’t have skilled experts to consult within their organizations.
Fortunately, there’s help for plant managers that provides valuable expertise, backup and support – whenever they need it.
Remote Support: A Perfect Solution
A manufacturing plant is full of complex systems and challenges. While Google and other search engines are valuable tools for finding recipes, checking if the pet store is still open, and shoe shopping, they aren’t necessarily dependable sources of highly technical information about how unique plants function. So when something goes wrong in your plant, consulting the multitudes of opinions on the Internet could lead you down a very wrong path.
Why wait to call your distributor or system integrator? Why leave it up to chance when you could secure the services of expert technicians and engineers, as if they were on retainer? Remote support provides just that: reliable help for quickly identifying problems and troubleshooting solutions in real time. Remote support options include:
- Email – for less timely issues
- Immediate phone support – walking through troubleshooting questions and answers
- Troubleshooting articles and videos – like Google, but better. Search a library of common industrial automation problems in an online support center and find the answers yourself
- Remote monitoring and application support – this is an additional layer of remote support that allows remote engineers to access your applications and resolve the issues themselves from off-site
Remote access to experts is advantageous for a number of reasons. You don’t have to pay a full-time salary to employees on different shifts, there’s one number to call – by anyone at any time, you can learn all about troubleshooting from online resources and the engineers themselves, and above all, it provides peace of mind.
The benefits of having that supplementary assistance at your beck and call include greater plant productivity, greater resolution efficiency, and greater trust in a plant manager’s ability to oversee operations. Remote support services can help you optimize control system performance, improve Overall Equipment Effectiveness (OEE) and reduce maintenance costs.
Consider TechConnect Support
Programs like Rockwell Automation TechConnect℠ can make any plant manager look like a hero for solving problems quickly and successfully.
Have a new employee on the night shift who isn’t completely qualified to troubleshoot? Give them one number to call for any number of questions or concerns – they’ll be on the phone with an engineer in about a minute and a half.
Don’t want to spend time after hours learning a new troubleshooting skill set? Enjoy the peace of mind of having a team of experts in your back pocket, ready to provide support around the clock.
And if you want to encourage your employees to train and learn on the job, our Training Advisor program is included to help supplement the growth opportunities you’re offering.