Add Emulation to your Speed to Market Toolbox
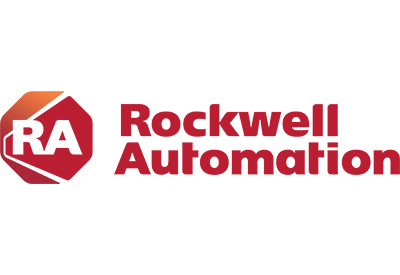
November 11, 2019
By Ian McGregor
I like to think of making products, as making promises. To shareholders. To distributors. To consumers. From the moment a new product is triggered, it is a race against time to deliver on that promise. And, as consumers demand new products and marketing responds with more variety, consumer packaged goods (CPG) manufacturers are having to make more promises than ever.
So, how can you attain this speed to market, without compromising current production?
It comes down to meticulous up front planning – before metal is cut, or existing lines disturbed. One thing is certain. Learning of problems with controls integration, line sequencing or bottlenecks after machines are built or lines reconfigured is not the best time. Too often I’ve seen this turn into installation delays, and worse, broken promises.
A virtual environment gets you ahead of the game
Traditional methods of machine and production line design, commissioning and startup can be costly and impede speed to market. CPG producers are turning to emulation as a tool to research, test and validate their process in a virtual space. Before making physical changes to plant layout and workflow.
Employing a virtual system that uses real operational logic and connects to PLCs can help minimize the resources it takes to bring a line from design to production. With an emulation model, you’re doing two things:
- Gaining the ability to fully test controls, reducing the amount of variability and risk in your project. Here you can test the coming together of the mechanical CAD and logical operation.
- Conducting tests off a project’s critical path, in parallel to the system build and as soon as design is agreed upon.
We’ve had clients report a reduction in on-site controls commissioning times from three weeks to four days on a bottling line. This scale of reduction is typical, and is a big factor in driving adoption.
Benefits beyond initial launch
Wonder what would happen if you increased throughput by 10 percent? How would the control system respond if you changed the mix of products?
With factory floor virtualization, you can experiment and troubleshoot post-launch to your heart’s content. An emulation model can easily be built for your existing lines, allowing for ongoing testing of new configurations and product types. Essentially, you can push the system to its breaking point, without any consequence, damage or interruption to the real thing.
It is also a great diagnostic tool for troubleshooting. Let’s say you’re experiencing synchronization problems or errors. You can apply an emulation model to the line, plug into the real control system, and dig in to find the malfunction. Often, this uncovers root causes to problems that presented as something entirely different.
No drawings, no problem
Having all the necessary 3D CAD drawings on hand is one of the biggest hurdles to adopting virtualization. The industry has come a long way in transitioning to full 3D representations of machines and equipment over the years. Still, there are always holes to fill.
To recreate a full plant without spending weeks tracking down drawings, you need a comprehensive library of factory equipment to supplement your own. For instance, Emulate3D maintains a library of generic industrial equipment to help make a digital twin of your factory a reality. It’s packed with every conveyor you can dream of, robots, operators, pushers, pullers, stretchers, you get the point. I like to think of it as building an industrial train set. And newer technology is helping make it that easy to build as well.
Why now?
The idea of virtualization is not new. But the possibilities it holds for impacting speed to market for CPG companies is becoming more accepted. Here are just a few of the reasons I believe that now is the time to make a move.
- Emulation technology is more attainable. Not only are more 3D drawings available, but creating your own model can be easy using drag-and-drop software.
- Your workforce is ready. Industrial engineers are coming out of school trained on this technology. They’re even helping build business cases for leadership given their understanding of the potential virtualization holds.
- Plug and play expectations are growing. As automation becomes more reliable, there’s an expectation to create production lines that work from the start, without months of ramp.
- Seeing is believing. The ability to see a virtual operation in context, using augmented reality and today’s realistic visuals, makes your vision more believable, to more stakeholders.