Three strategies for embracing and maintaining manufacturing flexibility
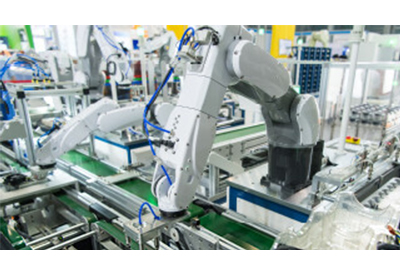
November 25, 2019
To keep up with the demands of today’s consumer-driven economy, manufacturers are increasingly adopting flexible production strategies. This can help companies be much more responsive to the whims of the market, but it creates some new challenges in its own right. Such challenges include reduced throughput, extra complexity and high installation costs.
At Omron, we’ve devoted much of our recent efforts to helping manufacturers become and remain flexible. For this reason, we’ve conducted research into the most effective methods for companies to implement a high-mix, low-volume production strategy without sacrificing quality or throughput. Let’s take a look at three ways to make flexible manufacturing effective.
1. Design for reconfigurability
Investing in new equipment every time you need to change products is extremely expensive and often unnecessary. Expenses come not just with the new equipment itself, but also with the cost of downtime while the machinery is installed. For this reason, it’s essential to use equipment that you can easily reconfigure for other purposes.
One excellent example of a highly reconfigurable technology is the collaborative robot. This innovative technology is designed to be highly adaptable to changing production requirements thanks to its intuitive hand-guiding mechanism and its ability to work side-by-side with a human operator.
2. Invest in an automated traceability system
It’s often necessary to quickly determine the status of any given finished product or work-in-progress, but this can be extra challenging due to the complexity of a flexible system. A robust, real-time traceability system can significantly improve the visibility of your operations and make it possible locate parts, products and pieces of equipment with minimal delay.
Traceability is also essential for maintaining high levels of quality on flexible lines, which can see an increase in errors if tracking is performed manually. However, if the work-in-progress traceability is fully automated, dozens of different products can be run on the same line with a negligible error rate.
3. Connect the dots with mobile robots
The constant reconfiguring of modular systems means that paths through the production “line” — which no longer resembles a line at all — are constantly changing. This presents a major challenge if the various stages of the lines are connected by conveyors, which are difficult to move and reconfigure for new line arrangements.
Fortunately, conveyors aren’t the only option. Mobile robots like Omron’s LD series provide a highly flexible means of connecting various production modules together without obstructing traffic throughout the plant. Their innovative software allows them to intelligently navigate around human workers and unplanned obstacles without requiring facility modifications.