Gripping systems are designed for collaborative, intelligent and intuitive operation
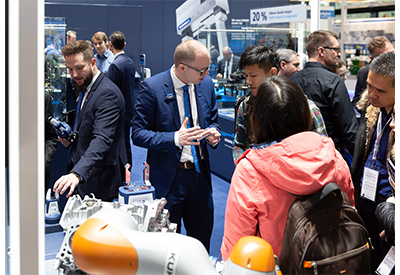
January 6, 2020
“We are experiencing a fundamental change in industrial production towards smart, intelligent processes – from initial planning and configuration, including commissioning and as ongoing operation and maintenance,” Henrik A. Schunk, Managing Partner and CEO of gripping system and clamping technology specialist SCHUNK stressed at the end of the SPS 2019.
“Subsequently, the component landscape will also undergo elementary changes. For the gripping systems this means: flexibility, intelligence and a radical simplification of layout, commissioning and programming are moving more and more into the focus of the users.”
Empowering Machines & Operators
The trend is furthermore reflected in the highlights that SCHUNK presented in Nuremberg under the motto “Empowering Machines & Operators” in Nuremberg. In the same way, SCHUNK ERT is currently celebrating its global premiere as the flattest rotary unit with absolute-value transducer currently available on the market. Designed for universal applications, its compact design with freely definable angle of rotation and high torques cannot fail to win customers over. Certified long-stroke gripper Co-act EGL-C, certified small components gripper Co-act EGP-C and the SCHUNK EGH for flexible use enabling a particularly simple entry into the world of cobots, represented milestones in the area of collaborative robotics.
Digital product lifecycle
In the SCHUNK EGI, the innovative family-owned company also presented an intelligent small components gripper with certified PROFINET-IRT-interface, which enables an individually programmable stroke of up to 57.5 mm per jaw and flexibly dosed gripping forces of up to 100 N. SCHUNK illustrated at the EGI as an example how the complete product lifecycle of SCHUNK components can be digitally mapped, from the calculation and design tool via the digital twin, commissioning via a web server to smart data evaluation and processing during ongoing operation via the PROFINET interface.
Plug & Work portfolios for lightweight robots
In the view of SCHUNK, lightweight robotics in particular will gain significantly in momentum over the years to come. Ready coordinated Plug & Work portfolios, among others for Universal Robots, are designed to make entry easier for users. For this the range of components includes certified Co-act grippers as well as proven pneumatic and electric gripping modules, sensors, quick-change systems and plug-ins.
One highlight in this segment was the long-stroke gripper EGL, which is setting a new benchmark for flexibility, power and functionality in clean to rough environments for robot arms by UR. In force-fit gripping, it can be used for process-reliable and gentle handling of the widest variety of alternating parts of up to 3 kg.