How JAE Automation helps manufacturers use data
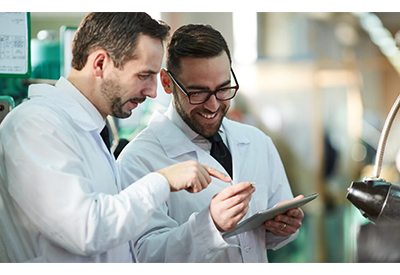
February 6, 2020
Take a look at your production facility. Each step in the process has the potential to produce valuable data that can be captured, analyzed, and used to make stronger and more effective decisions. Leading manufacturers are leveraging this data to identify trends, mitigate the impact of downtime and maintenance, increase output, and reduce costs. By taking a strategic approach to data and understanding its role in the organization, companies have created a competitive advantage that positions them for future success and growth.
Unfortunately, many manufacturers struggle to cope with the vast amounts of data that is available. Some may have seen limited benefits from previous implementations due to a lack of strategic focus or effective implementation, while others are simply unsure where to begin when faced with so many possibilities.
JAE Automation helps manufacturers take control of their data, understand what is needed to incorporate it into decision making, and implement the hardware, software, and network infrastructure required to make data available to those who need it.
What’s needed for a successful data initiative?
The fastest way to fail at data is to simply try and collect everything without knowing how you will use it. Because of this, the first step of any data project is to think strategically, ask the right questions, and determine the desired outcomes that you want to achieve using data.
This means taking a big picture view of your current manufacturing facility and understanding each step in the process, the data of data that can be produced at each stage, and what that data can be used for.
Based on this, you then need to ask a specific question that can be solved with the available data. For example, you may want to reduce repair costs by using equipment performance data to predict when a machine is close to breaking down and maintenance is required. You may decide to optimize the production process to reduce idle times and improve overall equipment effectiveness (OEE). Or you may want to improve product quality by tracking conditions such as temperature variance or speed through a specific process.
Depending on the question you ask and the outcome you want to achieve, the data, models, tools, and sensors will look different. By starting with the desired outcomes, you can work backwards to ensure you have what you need.
Next, you need to determine the metrics and key performance indicators you will use to track data and evaluate the effectiveness of the initiative. Common metrics may include OEE, throughput, downtime, changeover time, reject/defect rates, material waste, or the number of finished units over time. Again, the metrics you choose will depend on the question you are trying to answer.
Finally, data and insights must be made available to the people who need it, when they need it. This means you must determine the software and tools you will use and understand who will benefit from having access to information. Data should be stored in a centralized location and legacy silos should be torn down to facilitate the flow of information across departments, functional areas, and facilities.
How JAE Automation helps manufacturers make sense of data
JAE Automation assists manufacturers at all stages of their data and analytics initiatives by helping them take a strategic approach. Through a strong mix of technical and business expertise, JAE Automation helps companies recognize the data that is potentially available to them, capture and analyze this data to produce actionable insights, and incorporate these insights into the production environment to achieve a positive business outcome.
JAE Automation helps manufacturers:
- – Understand and map their current production environment
- – Identify the types of data that can be captured at each stage of the process
- – Ask the right questions and determine which outcomes will have the most impact on their business
- – Design the architecture and network infrastructure needed to capture, analyze, and deploy this data
- – Integrate sensors, devices, machines, equipment, and software to facilitate the flow of information across the organization
- – Determine how and where to store data for future trend analysis
- – Select and integrate analytics software, dashboards, or reporting systems
- – Align existing data systems with new projects to create a single, unified data environment
The Results – A better understanding of the manufacturing facility
Data and analytics are powerful tools that help manufacturers gain a better understanding of their facilities, identify opportunities for improvements, and detect and resolve issues before they occur. When implemented effectively and with a strategic approach, manufacturers can provide more information to supervisors, workers on the floor, and executive leadership, allowing them to make stronger data-driven decisions that lead to better business results.
JAE Automation works closely with companies at all levels of data maturity to help them take control of their data and harness the opportunities it provides. To discuss how data can be used in your facility, or to get started on a new data initiative, contact us today.