Welcome to the Edge
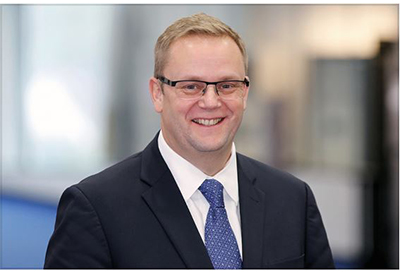
February 28, 2020
Edge computing has been around for a long time, but is now celebrating a revival in industry. Not all industrial users are convinced by the cloud. Rittal has discovered the potential of the edge and developed a corresponding product portfolio. Sales of the company’s optimization software will begin in the autumn. Rittal’s new Industrie 4.0 plant in Haiger serves as a ‘live’ laboratory.
Before the interview begins, Andreas Keiger wants to make something clear: “Edge computing has been around for a long time. At the moment, we are experiencing a new perception of this technology,” he explains. The electrical engineer is responsible for Rittal’s edge-cloud business. Most industrial users still associate Rittal with control cabinets. The owner, Professor Dr. Friedhelm Loh, likes to speak of the “Amazon of control cabinet technology”. Many industrial users often still identify Eplan’s software solutions as Rittal products. Rittal has been specializing in edge computing and private cloud solutions for more than ten years now – not always in the media spotlight, but sus-tainably. “Rittal is based on two pillars: industry and IT,” says Keiger.
Since being launched at CeBIT 2017, Rittal’s edge strategy has led to a convergence of these two areas. “Our solution focuses on industrial users who want to collect, process, analyse, train and restore data.” This topic is acquiring ever-greater importance in industry. Data processing volumes have grown to record levels. Rittal is convinced that the two zettabyte mark will be reached in 2019. According to reports at congresses and trade fairs five years ago, the cloud would be capable of handling such volumes of data. Today there is disillusionment. “I think we have communicated the cloud incorrectly for years. The large infrastructure providers are responsible for this and have to explain where the data is and what they do with it. We are experiencing considerable scepticism with regard to cloud applications.
Edge computing is gaining in importance, that’s true. And that is not all: in the recent past, big data has been hyped. Today, however, we need only a small amount of data to identify problems and improve performance. The edge is sufficient for this purpose. Many machine manufacturers are currently following the same learning curve,” explains Ralf W. Dieter, CEO of Dürr AG.
Friends of the edge
Keiger agrees with this: “Who wants to transfer sensitive production data to AWS? I know only a few.” Important data should remain on the edge, in the company’s IT systems. What’s more, many companies lack the bandwidth to quickly transfer vast quantities to the cloud. Short latency times are indispensable in many areas – such as for real-time-capable and data-sovereign industrial AI applications and video-based production assistance systems. Keiger and his colleagues are convinced: “When data first has to travel very long distances to data centres located in a cloud, the response often takes too long and puts customers at a disadvantage in terms of data-driven innovations.” In this context Keiger means Machine Learning (ML), Deep Learning (DL) and Reinforcement Learning (RL) – i.e. applications that depend on data and models.
“I am convinced that the vast majority of companies will be implementing ML on the edge in the future,” explains Peter Seeberg, who previously worked for Intel, was then responsible for ML projects at Softing and now advises industrial users (above all machine manufacturers) on ML-related issues. “The data can be trained on a standard notebook; the runtime models operate on an industrial PC in the machine. This is no different from a facial recognition model on a modern mobile phone,” Seeberg emphasizes. How did this come about? “In the past, customers often did not want a cloud solution, so we had to come up with an alternative.” But Seeberg is not a cloud opponent. “We need the cloud, but it has to be targeted. The cloud must fit in with the company’s strategy,” he says.
Siemens is likewise discovering the potential of edge computing. “The interaction between the cloud and the edge opens up entirely new possibilities. In combination with automation systems we can use edge technology to bring AI to the machine and into the manufacturing process, thus increasing productivity,” explained Siemens CEO Klaus Helmrich in a recent podcast. The company’s MindSphere World has featured an edge connector for several months now.
The next step: auto ML software
With regard to the edge, all four industry representatives can continue to rely on Moore’s Law, which says that the number of transistors in an integrated circuit doubles about every 18 months – also thanks to German EUV technology pioneered by Trumpf and Zeiss. After all, the prerequisite for an edge application – today and tomorrow – is the continued validity of this rule. Speaking to the Heise news portal, TSMC’s head of research, Philip Wong, insists that “Moore’s Law is alive and well. Contrary to all the prophecies of doom, it is not even sick! Nothing will change in the foreseeable future.” According to Wong, it will still apply in 2050 and beyond. The metric Wong uses for his statement is the packing density of the transistors.
Keiger is aware of the relevant statistics and has taken his ideas a step further. Rittal has now developed a production optimization software based on the data generated by its new plant in Haiger, which collects over 18 TB of data every day. With the aid of Bosch, Fraunhofer and IoTOS, Rittal is committed to creating an auto ML application that will make it easier for customers to streamline their production processes and operations. “If you have 100 machines and 26 robots, you know how difficult it is to obtain clean data from all of them.” Domain knowledge is essential – best of all automated domain knowledge – in order to train data models. In addition, there is a track-and-trace application that enables logistics integration. But Keiger does not want to reveal any more details. The product will be presented to the public in October. The software has already been tested at the Haiger plant. Rittal and its partners have developed algorithms that digitize employee know-how on the one hand, and perform pattern recognition on the other, as a basis for predicting malfunctions. Until a few weeks ago, this was still a standard algorithm. However, this algorithm will be adapted in order to become a service model for new customers. “Plug & Produce is our goal,” Keiger asserts confidently.
But Keiger has been working in the industry for many years and knows about the problems. “We still have language problems. I would be happy if we had a single data language. Everyone is doing their own thing.” Wasn’t OPC UA supposed to be standard? “Explain that to the colleagues at Alibaba and Baidu. The data language in China is quite different.”
And what about the edge? “It will get even smaller. Single sensors – or even single chips – will eventually become an edge. ML will take place on the edge in the future.”