Rittal: Busbar Is the Easy Choice to Replace Traditional Wiring
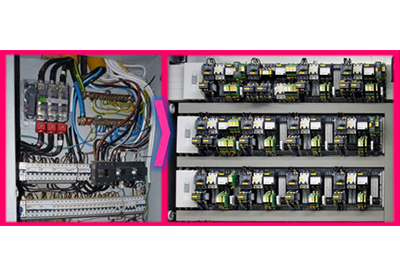
March 30, 2020
The need to power enclosures through traditional wiring is over. More and more panel builders are, at the request of their customers, turning to busbar to help them organize their power distribution controls and drives.
Traditional wiring in enclosures has been the choice for years since it can be less expensive, and in many cases, is spec’d in to the customer’s design. However, savvy customers familiar with the efficiency and cost benefits of busbar are starting to require it as the default solution on new enclosures. Global companies, already required by European compliance to have busbar in most of their enclosures, are spec’ing it in on new equipment purchases.
Wiring out a new enclosure is complicated and takes hours. The power distribution block is bulky and space-consuming. Bending and crimping thick wire bundles fill even more space in the enclosure along with the conduits. For repairs, the maintenance technician weaves though the clutter to get to switchgear. This increases downtime and takes hours for any repairs. All that enclosure space is used for traditional wiring, leaving less room for components, which necessitates larger enclosures, or more of them.
Raising the Bar on Power Distribution
Compared to traditional enclosure wiring, Rittal Busbar systems provide reliable, space-saving efficiency. By switching to a busbar system, components are so well organized that swapping out controls or drives takes minutes, not hours. Safety is wrapped around each busbar, both to prevent shocks and accidental arcing. And the compact design of the busbar system frees up space within the enclosure: for more components, easier access and sleek aesthetics.
Flexible power is built in to every Rittal Busbar design. It began with the concept to provide a continuous, reliable connection. The highest quality materials were selected for every component. In design, the innovators at Rittal focused on ease of use in installation and customizable operational layouts.
Getting to Know Rittal Busbar
Easy Assembly: All Rittal busbar systems install in just three steps, with no drilling required. Simply position the TS punched section within mounting flange in the enclosure, secure the busbar assembly and clip the cover in place. The entire assembly is light weight and simple to handle. Rittal busbar support may be top-mounted with components using the pitch pattern of the cover system.
Reliability: Rittal reliably meets power demands, and all are UL and ETL listed. Rittal is the world’s first manufacturer to offer an approved busbar system with standard components, optimized for both AC and DC applications for international use.
Flexibility: Flexibility comes with customizable plug-ins. Component adapters allow safe use of standard compact air-circuit breakers from a variety of manufacturers. Connector kits and adapters and transformers make contact without drilling. NH Slimline fuse-switch disconnectors range from sizes 00 to 3, fitting single pole and 3-pole switchable variants. And all components are modular for complete customized configuration.
Safety: In addition to flexibility, safety is paramount. Rittal busbar cover sections are critical to the protection of the people working in and around control panels. Safety is a major priority for the electrical engineer when looking at the design or maintenance of power distribution panels. Whether it be motor control panels, drive applications or any power distribution application, exposed busbars are a hazard to personnel and require insulating or protecting from inadvertent or accidental contact.
Rittal’s busbar solutions offer complete cover sections for flat copper busbar. The cover section and base tray provide reliable contact hazard protection up to IP 2XB (safe from finger contact). Integral to the busbar cover is shielding to prevent accidental arcing. Made from thermally modified hard PVC its protection corresponds to UL 94-V0. Moreover, components can be securely mounted on the top section, for easy retrofitting without removing the cover. The base tray provides rear contact hazard protection. The base tray, side covers, plus cover section provides all around contact hazard protection.
Forecasts for international markets are expected to standardize busbar as the required power distribution method. For the entire value chain, from designers to panel builders to plant engineers, turning to busbar for new or retrofitted enclosures will deliver greater safety, lower operational costs and meet future compliance standards.
See How Rittal is Engineered Better
Download the Busbar Whitepaper to learn more.
For more information, visit www.rittal.ca/powerdistribution or contact marketing@rittal.ca.