Four Major Safety-Related Benefits of Robots
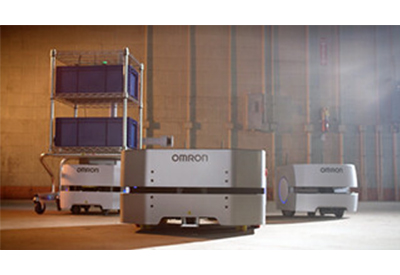
April 2, 2020
Manufacturing facilities employ a variety of hazardous machines, and safeguarding is paramount. While traditional safety strategies are designed to mitigate risk in hazardous situations, it’s possible to eliminate this risk altogether by letting robots cover the dangerous tasks. Let’s take a look at a few ways that robots make manufacturing safer overall.
1. They minimize workers’ exposure to hazardous motion.
The most obvious and commonly cited safety benefit of robots in the workplace is the opportunity to reduce workers’ exposure to mechanical hazards that pose a significant risk of injury or death. For example, instead of having workers expose their limbs to the hazards of moving sheet metal in and out of a 300-ton stamping press, a robot can assume that risk.
The usual method of dealing with these risks is to install functional safety components, such as light curtains, safety controllers, and the like. By changing the operation to a “no touch” environment, you can dramatically improve your workers’ safety by reducing their exposure to dangerous equipment.
2. They keep workers safe from general environmental hazards.
Beyond these more obvious and dramatic situations where there’s a point-specific risk, robots can improve safety when dealing with the more general environmental risk factors in a facility. For example, loud and excessive noise, high levels of dust, extreme temperatures, chemical exposure all represent insidious and persistent risks to workers.
Most of these risks can be moderated by the proper use of PPE and administrative controls. However, as any safety manager can tell you, these methods aren’t very effective, and they also require constant monitoring. Replacing operators in these environments allows companies to reduce or maybe even eliminate workers’ long-term exposure.
There’s also the added benefit of allowing safety managers to focus on other value-added activities rather than spending their days checking to see if workers have their earplugs and safety glasses on.
3. They reduce the risk of repetitive motion injuries.
Related to the general environmental risks, there’s an increased awareness of the risks posed to workers from ergonomic issues, especially those involving repetitive motion. Simple, repetitive tasks common to pick-and-place operations or minor assembly applications, such as installing screws, are the breeding ground for carpal tunnel or other repetitive motion injuries.
Companies often try to manage these risks via production quota limitations, task rotation or required worker exercises (such as stretching). Fortunately, robots are ideally suited for these types of tasks, and typically a basic SCARA robot can take over the pick-and-place or assembly operations with the greatest ergonomic risks.
4. They contribute to a greater awareness of safety in a facility.
Finally, there’s a renewed focus of creating a higher level of safety culture in the facility. A key element in having an effective safety culture in any plant is the general situational awareness of its employees. Unfortunately, many workers are engaged in repetitive tasks that breed compliancy and inattentiveness.
Workers’ minds can wander if their task is installing the same four bolts on an assembly line for an entire shift. If they become disengaged with their surroundings and then the unexpected happens, they’ll be less likely to notice impending hazards and slower to react to them. That general inattention may be the difference between a near miss and an injury.
Having a robot install those same four bolts for eight hours lets workers perform less monotonous and more engaging activities, which in turn increases their situational awareness and the general safety culture of the plant.