Smart Devices for Smart Steel Production
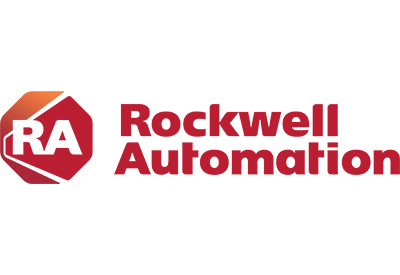
Making Smart Decisions Today
Smart manufacturing is the gateway to digital transformation. Connected smart devices open new windows of visibility into processes. Data and analytics enable better and faster decision-making. Seamless connectivity spurs new collaboration.
Companies that recognize these benefits are positioning themselves to be successful in the long term. By making smart investments in The Connected Enterprise today, companies are converging plant-level and enterprise networks, securely connecting people, processes and technologies.
One of those companies is a metals manufacturer. Comprised of multiple divisions, this producer is both a supplier of raw materials as well as a manufacturer of finished parts for a variety of consumer and industrial applications. They melt, roll and process steel but, at the core, this customer is a service business committed to investing in the people and technologies that add value to their customers’ products.
While the individual divisions all serve the metals industry, each division has unique operating requirements and customer demands. This producer understood the importance of keeping up with modern technology and the opportunities associated with data driven operations. Digital transformation was a departure from traditional methods being used across the divisions within their operations, but the potential opportunity cost was too much to forego. The challenge would be to identify solutions that could be shared across the unique divisions yet deliver distinct results.
Laying the Groundwork
The metals manufacturer selected Rockwell Automation as their vendor of choice to pursue their digital transformation objectives. While the benefits of investments to digital transformation can be tremendous, the potential risks associated cause many manufacturing companies to tread lightly. As many as 85% of big data projects fail due to a number of factors. The top three being license to operate, the uncertain future of the current workforce and lack of buy-in companywide. Anticipating these challenges and more, the metals manufacturer selected Rockwell Automation because of their reputation in the industry and expert approach to digital transformation.
Careful to deliver an implementable solution, it was important to develop a plan that provided the customer with a singular strategy that allowed for strategic differences within the different divisions. Operational assessments were conducted with core stakeholder teams to develop a strategic roadmap. The C-suite, finance, operations, engineering and IT teams were consulted to deliver a solution that offered transparent similarities and differences across the divisions and aligned with corporate and individual needs. It was also important that these key stakeholders realized the benefits of digital transformation and were fully on board to achieve long-term success.
The Approach
By leveraging Rockwell Automation’s established Connected Enterprise framework, assessments were taken across the enterprise to develop recommendations, form a business case and establish a roadmap. To accomplish this, several steps were taken:
- – Evaluation: Existing strategies and infrastructure of the organization were examined. A deep dive was taken to analyze IT/OT, information and networks as they currently stood. Each division of the company was found to be in a different stage of their own digital investments.
- – Assessment: Multiple division visits and workshops with diverse client stakeholders took place to assess potential gaps and roadblocks that could prohibit a successful digital transformation. On a divisional basis, an understanding of where each division was on their own journey and what they required to be successful were measured.
- – Identification: Opportunities for business benefits and improved device connectivity across divisions were quantified and a plan was put in place to address these target areas with digital transformation. These targets were set to meet goals corporation-wide while taking into account where each entity stood separately.
A clear plan, developed around the organization’s goals, was laid out. Each identified piece of digital transformation was chosen because of its ability to solve an identified business challenge – it had a clear business case supporting it. They were also prioritized by the capability to scale up organization-wide. While each division had its own unique requirements and objectives, the solutions identified had to fit with the greater goals of the metals manufacturer.
Identified Solutions
The results of the assessment across the individual divisions identified a set of tangible savings through digital transformation. Labor productivity improvements of 8%, tooling cost reductions by 10% while cutting down on scrap by 13%. Additional downtime reductions of 12%, saving time and money where it’s most frequently lost.
Digital solutions included the modernization of current automation pieces in the plant to allow for data access and connectivity across machinery. Edge analytics software was proposed to fulfill the need for monitoring and analyzing streaming process data for real-time anomaly detection. In addition, a variety of process improvements were identified. These included augmented reality to access mobile data and for operator performance improvement, device analytics to alert to abnormalities and offer real-time device status, and model predictive control to optimize the melt process and energy usage. From a corporate perspective, a center of excellence was proposed that would allow the divisions to share their digital results with each other and provide a backbone for continued adaptation and success.
Several of the divisions have proceeded to implement the core of these new solutions with Rockwell Automation and its partners. With these updates, the metals manufacturer is positioning itself for long-term success and is prepared for the next phases of implementation and digital updates. Working together with Rockwell Automation, the customer has already seen significant improvements leading to optimized production, reduced downtime and money saved.