Global Beverage Giant Selects PlantPAx Modern DCS to Improve Throughput
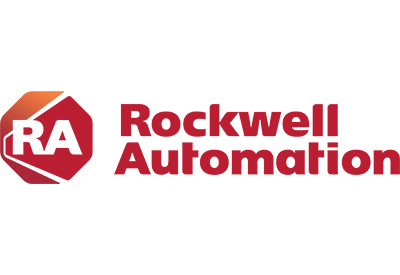
April 20, 2020
By Kevin McEnery, CEO, McEnery Automation
When you commit to improving processes, some of the benefits are obvious – and some are not. It’s those “hidden” benefits that can’t be overlooked when assessing the total value of a new system. In a recent project with a global beverage producer, it’s those benefits that are producing some added bonuses.
The project originated because sales have increased for this global beverage company’s fizzy drinks, challenging one syrup manufacturing facility’s ability to keep up with demand. The plant needed to expand throughput, and to gain more flexibility.
To meet these challenges, they partnered with Rockwell Automation and McEnery Automation to incorporate a PlantPAx modern DCS.
The system delivered as promised: it has improved repeatability and recipe consistency, and it has dramatically increased throughput and eliminated bottlenecks. The solution is making it easier for employees to move product and do things right the first time.
Bottlenecks: Thing Of The Past
Every production area that I’ve ever encountered has some inherent potential for limitations and bottlenecks. There is nothing more frustrating for an operator or manager than having to live day-in and day-out with those bottlenecks and limitations.
In this particular case, production bottlenecks were caused by several factors which our new system was able to eliminate. For example, because recipe management has been automated and process intervention has been dramatically reduced, operators no longer have to manually enter recipes – removing the potential for error. Additionally, the layout of the new system brought the ingredients closer to the mixer, making transport safer and more convenient.
Those changes resulted in:
- – Higher throughput
- – Higher quality batches
- – Greater consistency among batches
- – Reduced potential to damage ingredients in transport
- – Reduced potential for employee injury while transporting ingredients
While we fully anticipated the throughput, quality, and consistency to improve, it’s those last two benefits that stand out to me as the added hidden value of the project. The less an ingredient is handled, the better it is for the end product and the employee.
More of What We Want, Less of What We Don’t
Over time, it’s very common for employees to adapt their processes to parameters of their systems – meaning they’ll get things done even if it means walking 20 steps farther than necessary because that’s how the machine layout worked in the plant.
Those steps, those heavy lifts, they add up. Better layout, better process design, better technology, all contribute to reducing all of the things we don’t want to happen: product variability, process misalignment, even the potential for employee injury.
With less time spent on recipe management, process intervention, and ingredient transport, those operators are free to concentrate on other, value-add work. Essentially: More quality product is made with less equipment and operator involvement. And that means the plant is better able to keep up with global demand.