Looking at how Innovative Automation is Helping with the Increased Demand for Healthcare PPE
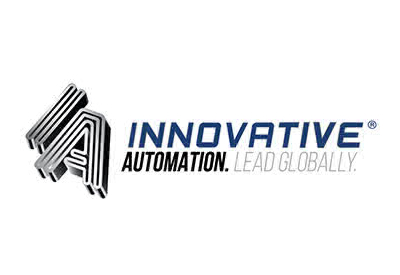
May 1, 2020
By Blake Marchand
Innovative Automation is an automation solutions provider for the manufacturing, food and beverage and pharmaceutical industries located in Barrie, Ontario.
As everyone knows well, the COVID-19 pandemic has created an increased demand for PPE, ventilators and other healthcare related products. In response, companies like Innovative Automation have answered the call from government to support that increased demand in a number of different capacities.
Within one-week, Innovative Automation went from being approached about developing face shields to beginning production on an order for 200,000 units.
“By Friday night we knew we had a process that would work and by Tuesday of the next week we had sample materials and by late Tuesday (that day) we actually had samples at RVH and Orillia Soldiers Memorial,” said Steve Loftus, President & Co-Owner of Innovative Automation.
“They both were pleased with the samples… and within a week of someone asking us about it, we had orders for approximately 200,000 face shields.”
“The first week we produced 10,000,” Loftus said, speaking on April 14th, “last week we had shifts as high as 8,000 units in one shift. We’re running a full production and we’re still automating.”
Once they sourced all the materials, determined the specifications and developed a couple prototypes, Loftus said, “we had a group of machine builders start building the line – all manual stations to start with and we built it in a modular fashion so we could sub-out the manual stations for more automatic ones as we built them. That’s how we’ve been able to ramp our production up.”
Compared to how they normally operate, Loftus said, “nothing is different up until the point where we’re running manufacturing. Because that’s what we do: typically, we have a customer that comes to us with a product and say, ‘here’s a face shield, how do I build this and what equipment do I need?’”
With the current situation, they worked on more of a parallel, building prototypes while establishing the supply chain and figuring out the logistics of everything, boxing, packaging etc., the things they wouldn’t be a part of on a regular project.
They have had to pivot slightly to take orders and handle processing, packaging and shipping. Which included implementing an ERP System. They were in the process of developing a new system, at the time, “one of the things in our new ERP system was to handle standardized processes,” said Loftus, because they were about to launch a new product involving standardized processes, they could test the system as part of its development process.
“They worked right through the weekend to set up our ERP system to handle everything – there’s all the product tracking, the label printing, all of that stuff is handled through the ERP system.”
Innovative Automation is still building machinery for regular clients, although noted some projects have been postponed due to the pandemic. This project allowed them to redirect and add staff as the production increased.
They are also working on a tidal pump project for automatic ambu bag pump, which is a face mask ventilator. So far producing three prototypes and two demo versions. The unit was ready last Wednesday – Steve said they had started looking for orders so they can start manufacturing. They are also working on a project with manufacturer that wants to make N95 masks, “they’re asking for some assistance with automation equipment to do that.”
How has COVID-19 changed how you operate?
Loftus noted the company developed a policy to handle SARS and swine flu, so they began sanitizing common surfaces and educating their employees early on. “The policy they had already developed made it easy to implement safety protocols.”
They currently have 90 people working form home. The people on the manufacturing line, because some of them are within the physical distancing space, are separated with dividers and are wearing PPE like the face shields they’re manufacturing.
“The other thing we do as a management team is a Teams Meeting.” They had actually started using Microsoft Teams for meetings before the pandemic made it a necessity, he noted.
“Everyday we deal with what’s happening. Because early on there was such a change day-to-day there were complete changes in processes, and if you weren’t meeting everyday as a company, developing strategy and communicating it, it was a problem.”
Loftus said they also started using an internal alert system, sending updates directly to employee’s phones.
“Everyday there’s a communication to them about what has changed that day. And early on they were long, there was 10-12 items that was changing per-day.”