Pivot Production With Flexible Manufacturing
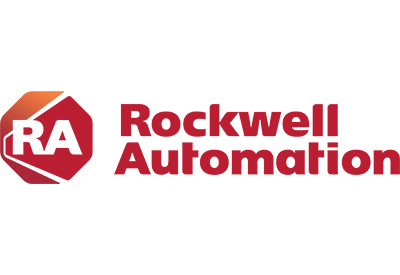
June 3, 2020
Crisis creates change – often permanent. Consumers behave differently. Industry innovates. Machine builds come with new expectations.
In the midst of the COVID-19 crisis, the only surgical mask manufacturer in Australia, Med-Con, was asked to significantly step up production – from two million to 80 million masks a year. Foodmach stepped up to help increase manufacturing capacity by building seven additional machines. But this was no ordinary order. The challenge: recreate machines that were designed and manufactured 40 years ago.
These builds normally take several months and include drawings and bills of materials. Foodmach had just 60 days and only a model to work with, a model based on 40-year-old parts.
Recreating this machine on today’s standards has been a nail-biting journey with the daily ups and downs detailed in its Project Med-Con Blog. But we’re excited to share it was a resounding success.
Pivot With Flexible Manufacturing
While this was an extraordinary challenge, at its heart it is a pretty common scenario: new expectations of old equipment. This equipment worked just fine for regular day-to-day operations but in many cases can’t handle the speed needed with surging demands.
Speed requires flexibility – from both machines and people. That’s because flexibility is as much a mindset as it is a tangible means for coordinating production. Rigid has no place in the face of new circumstances and market conditions. It’s about creating a seamless flow from need to delivery, decision to implementation and challenge to solution.
Foodmach wasn’t about to say no to an opportunity to help people around the world. And we were ready to do whatever it took to expedite our products and share our expertise to support Foodmach’s work.
We looked at the first-generation machines – lots of facilities have them, one motor driving a single shaft that ties into the other processes. For every revolution of the shaft, a part comes out the other end. But the shaft can turn only so fast, dramatically limiting the ability to increase speed and vary production.
We helped Foodmach pivot production, eliminating the shaft altogether in favor of new mechanics that independently control every part of the operation and run asynchronously to optimize performance and throughput.
It wasn’t a move that took days or weeks. Within hours after the call from Foodmach, our crisis response team was in action.
Prepare for Next Normal
The flexibility of your manufacturing will help you react to supply chain and market fluctuations right now and also prepare for the ‘next’ normal. The beauty of Foodmach’s work is the ability to create a modular and scalable system using a common set of programming tools – on an older platform. The key: we did not overcomplicate the process.
Part of that was a result of the time frame – when you only have weeks to deliver, there’s just no opportunity to overthink. The deadline drove fast iterations and innovation. In looking at the old mechanical design, it was immensely complex. When we jumped generations, we eliminated 80% of the mechanical parts. By reducing the number of mechanical parts, you reduce the chance for failure.
This was a rapid response. Technology was on our side. This is also a great example of focusing with a new lens. From infinite speed control to integrated servo controllers and motors – flexibility and speed are made possible by simplifying the complex.
The aging machinery was working well for what needed to get done – before the pandemic. Maybe your set-up is just fine for what you’re doing right now. But are you ready if you need to pivot?
Flexible manufacturing gives you the freedom to meet changing market demands.