Don’t Work Your Data. Make Your Data Work for You.
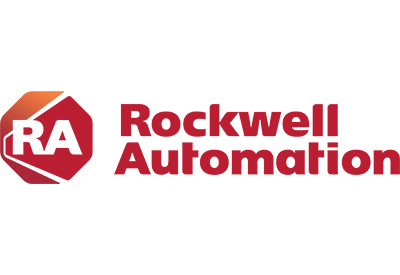
June 23, 2020
By Steve Mulder, Regional Industry Manager, Rockwell Automation
Digital transformation. Smart manufacturing. Industrial Internet of Things (IoT). A connected enterprise. Industry 4.0.
Whatever you call it, data drives it. Digitalization is a fundamental element of a food and beverage producer’s success. Getting it right from the start can be the difference between unlocking millions in operational savings, or losing the same in inefficiencies and wasted time.
Don’t fall into the “big data” trap
In the late 1990s, the term “big data” came on to the scene. Since then, we’ve gathered more data, trained scientists to slice and dice and make sense of it all, and tried to automate the arduous task of extracting business value.
While big data makes sense for some analytic and consumer applications, it is not a good fit for industrial applications on the plant floor. Instead, producers need contextualized, structured data to gain actionable information on KPIs like energy consumption, OEE, batch efficiencies and quality.
So, how do we transform and apply the plant floor data that is so critical to realizing value and productivity? By leveraging tools that take a smart approach to data right from the start – organized and contextualized to allow simplified data flow that leads to faster insights.
An automation system built with information in mind
Smart objects have emerged as a new, simplified way to organize data so it can be easily collected from the controller, then moved to and consumed by IoT systems. The standardized framework fully exposes data sets to pre-configured context for the developer, greatly shortening programming time.
Said differently, IoT and automation systems have different rules, and smart objects create the common language for them to speak. At its core, smart objects bring automatic discovery, standardization, synchronization and integrity to your data.
In a conventional setup, the automation system interfaces with the IoT platform via a gateway. This gateway typically requires configuration and effort to stage the data. And it is typically at this point where contextualization work becomes critical, especially when disparate systems are involved. Because the IoT system is not “aware” of the automation structures, you may have to build a new model for every application, and further inefficiencies result as the IoT system bombards automation controllers for data. For instance, an IoT system would get information in pieces, such as: action X is about to happen, action X is happening, action X is complete. These three data points need to then be manipulated to connect as one related, continuous action.
In a system built with smart objects, data can be automatically organized, modeled and consumed by IoT systems and applications with little to no effort from a programmer. PLC tags can now have consistent definitions of rates, states, status, etc., and they’re delivered into information databases with context such as line number, machine name and location. These elements are all critical in enabling IoT solutions that ultimately drive more insights, better analytics and a deeper understanding of your process and potential risks. In the example above, the three data points for action X are automatically recognized as one continuous action for greater context.
Smart developments for developers
So why does this all matter? Ask any developer who’s worked in the IoT world. Nuanced, inconsistent data creates traps that result in frustration, troubleshooting and lost productivity. According to Forbes.com, data scientists report spending 80% of their time preparing data rather than mining for insights.
Consider a simple beverage line with five machines (see “beverage plant” animation). It may have over 1 million associated data values. Most companies don’t have the available resources to manage all this information, nor is it where they should be spending their time. Smart objects streamline data preparation, i.e. one model feeds many applications. One customer estimated it would have taken a developer one month to do what smart objects enabled in only 6 hours – a 96% improvement.
In addition, this more direct method results in better data integrity and determinism. We can compare what the same product does at different stages with unheard of accuracy and integrity. And, with the ability to assign attributes to the data such as OEE, energy or mass flow, we get information that is automatically aggregated and categorized. From there, it’s reported on in a way that is meaningful for both human and machine decision making and optimization.
In the end, smart objects don’t change the data. But it greatly simplifies how you capture, view and present it, and over time, how you optimize operations as a result of it.