Taking Panel Design to the Next Level in an Automated World
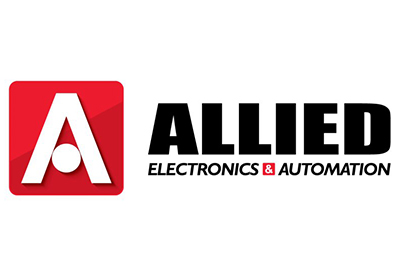
On February 15th, 2020, the Roberson Car Wash in Salem, Oregon went up in flames. The cause: a control cabinet with components that gathered excess corrosion from intrusive moisture. The panel components overheated, began arcing, and eventually melted pails of hydraulic oil, igniting dry uniforms hanging nearby.
Electrical control panels can, without proper design and components, be dangerous. A panel’s design, along with carefully selected internal components, is crucial to both safety and complying with regulations and standards.
Design for Efficiency and Safety
There are numerous considerations and challenges in control panel design.
First, most industrial control panels comply with Underwriter’s Lab, UL 508A, the Standard for Industrial Control Panels (now in its third edition) . The 508A Standard is the guiding standard for design and construction of industrial control panels to comply with the National Electrical Code.
Panels should allow for flexibility to accommodate design changes over time and add new components as system needs and demands change. Components should be compact to save space, yet possess excellent performance characteristics to meet specifications, for an optimal and efficient design. Incorporating such efficiency will decrease overall cabinet size, require fewer parts, and facilitate installation and maintenance.
With an optimal design, spacing and airflow will improve, as will cleanliness (dust, moisture, and other accumulated debris can start fires).
Designing efficient panels also means allowing for easy access and inspection, before testing and replacing any components to ensure operability and prevent fires. In addition, designs should incorporate sufficient over-current protection to accommodate unexpected amperage draw. Wiring and wire routing should be optimized to ensure that power to the panel is safe safety and as space utilized efficiently.
Choose Components Wisely
But designing a control cabinet begins, not just with what is on the schematic, and not just with what is on the outside – but what’s actually on the inside. What components do you have to work with, and how do they help to design, build, and operate a better control cabinet?
At the outset of panel design, it is crucial to consider continuity of power to control components and circuit protection. Lack of power supply is a common single point of failure. Be sure the overall design’s power supply has adequate step-down voltage, with over-current protection, and uninterrupted power.
After these conditions are met, choosing the right components is the next order of business. With reliable components that are durable, high-performing, and safe, cost is reduced, and performance and safety assured.
New components should be configured with features such as flexible wire management, approved and compliant wiring and cabling, adequate insulation, and come from reliable sources with disciplined quality control measures, all while helping the panel designer create an efficient footprint. For example:
- Contactors ideally will be climate-proof and suited to the specific environment where they will be used. They should also be adequately tested to all applicable standards within the industry they operate. They should also be selected for sufficient switching cycles specific to their application and depending on how the control cabinet is employed, suited to a wide range of applications.
- AC Drives should be selected with properties flexible enough to mount within the challenging configurations of a panel’s footprint. Airflow should be adequate to maintain specified design ambient air temperatures and may require additional climate control to regulate humidity and maintain the desired ambient temperature. Power supplied to the drive is often separate from control wiring and should also be incorporated into the design. AC drives should be versatile enough to use in different applications with a wide range of ambient temperatures and climate conditions.
- Motor starters and thermal overload relays should be compact, easy to use, and allow for simple wiring, yet provide all specified performance characteristics and meet all applicable industry standards. Thermal overload relays should operate with low and high voltage as required, have sufficient margins of protection for the anticipated applications, and be compatible with other components to enable versatility for a panel’s configuration.
While this is just a sampling of some of the key components specified in control panel design, it exemplifies the thought process to explore when looking for the right components for a specific panel, application, and environment.
Integration for Compliance and Safety
Component integration for compliance and safety is an engineering best practice for panel design. Designs must be compliant with NEC, NFPA (NFPA 79 is key,) and UL standards, and consider OSHA requirements as well as any known safety hazards. The components themselves should also be checked for compliance with any specific standards for the industry in which they operate and be compliant with prevailing standards such as NEMA, Canadian Electrical Code, and any other international standards.
“Reliability is a huge factor, and knowing the product is going to work the way that they need it to,” says Mitch McClain, an OEM sales engineer within the Eaton Corporation based in Dallas, Texas. “Footprint has become a topic growing in popularity to reduce the overall size of the panel. It is becoming important to customers to have more compact panels, with fewer components, and can do the work of the larger version of the same panel of the past. Also, versatility is becoming quite important. Being able to mount new or different components as applications and usage of the panel changes is becoming more common as technology and automation evolves. ‘Plug and play’ capable components are also advantageous when old components become obsolete or when better ones become available. Plus, when panels are checked for hot spots, loose connections, and degradation or corrosion, ease of replacement is desired.”
Summarily, control cabinets continue to become more important as system automation advances require reliable, versatile components that are accessible, easy and maintain, and most importantly, safe. Designing control cabinets and selecting components with these considerations in mind from the outset allows for greater flexibility and efficiency in construction, maintenance, and future upgrades.
As for the Roberson Car Wash, after being out of business for four months amidst a world pandemic and a complete rebuild, they reopened in June 2020, with fully upgraded panels, and a greater appreciation for what goes inside of them.