Pandemic Creates New Job Roles and Fosters Automation Investment
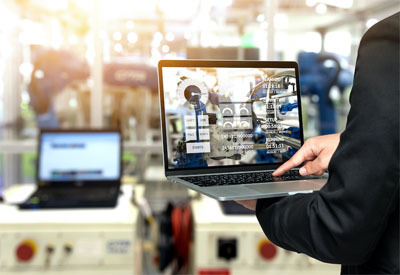
August 24, 2020
By Pat McGibbon, Chief Knowledge Officer, AMT
“Those who cannot remember the past are condemned to repeat it.” This observation was made by philosopher George Santayana in 1905, but can help manufacturers today avoid mistakes in responding to the impacts of the pandemic. History shows that there are two likely outcomes of the current crisis which relate to manufacturing. First, automation and digital manufacturing technologies will expand sooner and faster than the manufacturing technology market as a whole over the next two years. Second, this growth spurt will lead to changes in the manufacturing workforce throughout the recovery.
University studies point to a strong relationship between recessions and sudden bursts of expansion in automation and digital tech investment. Researchers at the Universities of Zurich and British Columbia found that 88 percent of job loss over the past three recessions occurred in automatable occupations.
Evidence to corroborate this research exists in the manufacturing technology market. Computer numerically controlled (CNC) machines represented about a third of U.S. production and consumption of manufacturing technology in the years just before the 1981-82 recession. CNC machines grew steadily, but slowly, as a percentage of U.S. manufacturing technology production and consumption since the early 1970s. But during the recession, CNC machines jumped from 33 percent of manufacturing technology production to 41 percent and remained at that level until the stock market crash of 1987. CNC machines’ share of production and consumption jumped 14 points in less than two years during the recovery from the 1987 crash. Most recently, the decline and rebound of orders for robots, automation, and new technology (i.e., horizontal CNC B-axis lathes) were much less dramatic than the 60 percent drop that overall manufacturing technology orders experienced during the Great Recession of 2009. As an example, two years out from the start of the recession, robot and and CNC B-axis lathe orders were up five and 13 percent, respectively, from their 2008 levels while the manufacturing technology market was still 25 percent shy of its 2008 mark.
The increased share of investment spent on automation and digital technologies has a direct impact on productivity, prices and employment levels. U.S. manufacturing employment peaked in 1979 at 19.5 million people, and the average value added per employee in 2012 dollars was $43,000. In each of the next three major recessions, employment was lower at the recession’s end, but the value added per employee climbed by 17 to 20 percent. The growth was due in large part to increased investment in new technology, but leaner operations also played a part. Research from University of Rochester found that hundreds of job roles and positions that were automatable were eliminated during the Great Recession. They were replaced in wholesale fashion with a mix of technology and higher-skilled workers as the economy improved. A Brookings Institute paper suggests that 59 percent of the manufacturing jobs that existed before this pandemic have the potential to be replaced with automation during this recession and in early stages of the recovery.
Understanding that automation will likely expand during this recession while large numbers of job roles will change offers opportunities. Help your customers not only survive but grow in this downturn through investments in automation and DONE IN ONE® technologies. This will require manufacturers to learn about the return on investment in productivity technologies like automated materials handling, Multi-Tasking and HYBRID Multi-Tasking machines, and other digital technologies. You can also help customers by developing methodical investment strategies to intelligently integrate the latest technology. Manufacturers need to take a hard look at what skills they have versus what they will need to get the most out of new technology investments. Downturns are great opportunities for restructuring your processes and training your people. When business begins to pick up, don’t hire for positions where people were laid-off. Hire or train people to expand productivity along with your investment strategy. Upskill your workforce for the production technology you will have instead of what you had and your workers will grow into that technology. Then set your sights on repeating the process in five to seven years remembering that history will repeat itself.