Planning a New Automation Project? Make Sure You Budget for Training and Development
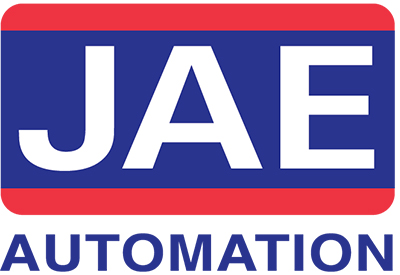
December 7, 2020
By Eric Martin, C.E.T., JAE Automation
Conversations about automation technology and design often focus on one thing – the technology itself. We think of the high-tech robots, the automated conveyors, or the precision welding machines that make it possible for factories to operate more efficiently, productively, and safely.
However, any discussions around automation technology need to include the most important element – the people.
In any facility, people are operating the machines, conducting maintenance and repairs, handling setup and changeovers, or identifying new opportunities for improvement. What they bring to your facility impacts the entire organization.
That’s why any automation design project should include a plan, and, crucially, a budget, for training and development. Building a consistent, repeatable, and continuously evolving training program empowers employees to find new ways to make things better.
Plan for training during the design process
Training shouldn’t be an afterthought. It’s not enough to put some basic training together once the equipment has been designed, built, and installed in the factory. Instead, training and development programs should be considered from the beginning, with schedules, budgets, and topics prepared as part of the design process.
Rather than viewing it as an expense or necessary evil, training should be thought of as an investment. It’s an investment in your people, their skills, and your business. Good training means good processes, and good processes mean better performance. Well designed training programs deliver value over the entire life of equipment or tenure of an employee, naturally providing a positive return on your investment.
With the help of an automation design partner, you can take time early on in the process to understand how you will set up your training, the level of depth you will go into, who will take part, and how the training is delivered. Some of this will depend on how your organization is structured while some of it will depend on the equipment, the level of complexity of the new solution, and the role it will play in your facility.
Failure to develop and implement well-designed training programs can have a very real impact on performance. Imagine, for example, that the night shift is outperforming the day shift in terms of productivity, throughput, and quality. After investigating, you find that the day shift has completely different processes and is doing things that you thought had been phased out in favour of better methods.
This may be a sign that training is not being conducted the same way for everyone. Through consistent, repeatable, and evolving training programs, you can reduce this risk and keep everyone working together toward a common approach.
Make training consistent, repeatable, and evolving
Too often companies have training programs that are static, one-time exercises. Sure, it’s necessary to train new employees when they are hired or train staff on new equipment, but that’s not enough to drive the types of improvements you should be looking to make.
First, training should be conducted consistently and at regular intervals. It is ongoing, with new information and ways of doing things incorporated into the program so that everyone benefits from organizational learning. This not only acts as a refresher for employees, but also creates opportunities to go deeper into topics that would otherwise not be covered in high-level introductory sessions.
Second, it’s crucial that training is repeatable. It’s no good to have 20 different people doing things 20 different ways, but that’s exactly what can happen if training isn’t conducted regularly and with a repeatable process.
Finally, training programs should evolve to include new and improved ways of doing things. As people become more familiar with the technology, equipment, and processes, they find new ways of doing things that become part of their workflow.
These enhancements must be captured in training documentation and incorporated into the training that all employees receive. New ways of doing things should be communicated with the rest of the team, allowing the entire company to benefit. Training isn’t static. It’s a living, evolving process that should be based on continuous improvement.
Empower your employees to make things better
Good training goes beyond teaching people how to use the machine. Instead, well designed training empowers people. It creates a culture that recognizes the role people play in your facility and the impact they have on your performance and business success. A consistent, repeatable, and evolving training program enriches employees by investing in the skills, knowledge, and abilities they need to be successful in their jobs.
In short, better training means more people who know how to make things better. And when your entire business is tied to the performance of manufacturing, that’s an investment that’s worth making.