Lean Robotics: Making Robots Work in Your Factory
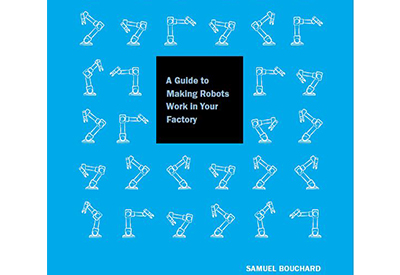
February 9, 2021
By Samuel Bouchard
WHY I WROTE THIS BOOK
It was winter 2009, and I was on a mission to sell my startup’s first product, a robotic gripper, to the automotive manufacturers of Michigan.
My cofounders and I—three friends from the robotics lab at Laval University—had a straightforward business plan for our new company,Robotiq.
At the time, every robotic gripper had custom-made fingers, so whenever manufacturers wanted to use grippers in their robotics-based assembly lines, they had to go through lots of trial and error regarding custom design and fabrication.
Our gripper, by contrast, was an off-the-shelf solution. With three articulated fingers that automatically adjusted to the object, it was able to grip practically any shape.
It also had 10 years of research and development behind it, and its robustness was proven in real-world nuclear site clean-up applications.
So if automotive manufacturers—the biggest consumers of robots—had any sense, they’d be lining up to buy it… right?
I drove to dozens of factories that winter to meet with the designers and assemblers of their robotic systems, who are called system integrators.
At each meeting, the system integrators would let me in, watch me demo the gripper, and respond with words to the effect of “thanks, but no thanks.” Then I’d be politely shown the exit.
Sometimes they’d say the gripper seemed like cool technology—it was just too complicated, too expensive, and too inapplicable to any oftheir current projects.
After six months of non-stop effort, I had made precisely zero sales. I remember leaving the last meeting feeling utterly miserable. There was freezing rain on the roads of Michigan while I drove to the airport in my compact rental car with slick summer tires, hands clenching the wheel, trying to make it safely back home.
My thoughts went in circles: “What’s wrong with our product? What did we miss? Am I just not trying hard enough?” One image came to mind: a trapped housefly butting against a windowpane, its persistence futile.
Sure, it was just after the crash of 2008. Few businesses were open to new ideas, since most of them were busy just trying to stay solvent. But was that the only reason we couldn’t sell a single gripper?
I left Detroit on a flight back to Québec City, dwelling on the same anxious thoughts. Then I started to chat with the man sitting next to me. It so happened that he worked for one of the largest robotics system integrators in Detroit.
So as soon as he asked what I did, I pulled out my phone and showed him a video of our gripper—and he said “Why don’t you come by in two weeks? That looks like it’d useful for one of my customer’s projects.”Finally, I felt our luck was beginning to turn.
When my team and I actually got to the man’s facility, however, reality hit again. Our gripper—rather than being a time-saving solution like we’d advertised—ended up requiring three engineers to work for three full days just to connect it with the robot.
It was at that point that I finally realized two things. First, automotive manufacturers were right not to buy our product, because it didn’t solve the problem of customized grippers. Second, that problem was a tiny one compared to the bigger issue: robotic system integration was way too costly and complicated!
We were working day and night on a company that was headed right into a wall. We had a product no one wanted to buy, and we were trying to solve an unimportant problem. How could we have missed these two vital pieces of information for so long?!
In my quest to answer this question, I came across a book on product development called The Four Steps to the Epiphany by Steve Blank. The book presents a method called customer development, which is a deliberate contrast to “product development.” Blank argues that companies don’t fail because they don’t have any products, but because they don’t have any customers. This was exactly the case for us. I had to keep reading.
Blank provides a step-by-step method to get the information you need from customers so you can develop products they will want to buy. At first, there are many unknowns: Who are our customers? What is their biggest problem? Who decides what to buy? How much are they willing to pay for it? Who would they buy it from? The list goes on.
Designing the right product requires a deep and complex understanding of the customers, the market, and the technology you can use to build the product. There are no perfectly defined answers. Yet, Blank managed to take a big, confusing problem and break it down in a way that even newbie entrepreneurs like me could follow.
We’ve been applying his methodology to all our subsequent products to make sure they’d have customers. Most of the time, it worked. When it failed, we’d always look back and realize there were places we did not apply the process properly. Eventually, it became second nature to follow the step-by-step process.
As for our realization that the biggest problem is “robotic system integration is too costly and complex,” we worked to address parts of it with each of our subsequent products. This book is another step towards solving it.
Robotic cell deployment, like product development, is a process you can approach from many angles.
It often starts with broad, ‘fuzzy’ questions:
Can robots help my business? Can a robot do this task? Where should we put it? How do we set it up? Which technology should we choose? And where do we start?
These are all questions you may have asked, only to hear “it depends” in response to every single one. It’s true: the answers depend on the application, on your team’s robotics skills, on your business objectives, and much more. That’s because in manufacturing, the only thing that never changes from one factory to another… is that every factory is different!
But while there may never be a “one size fits all” robotic solution that can be used in every factory, I believe every factory can use a standard process. By implementing a clear, standardized, step-by-step methodology, we can break the fuzzy large-scale problem down into a series of smaller, more manageable pieces. We can be more successful at deploying robots that will drive our businesses forward.
That’s why I wrote this book: to present the methodology my team and I have developed over the past nine years since Robotiq was founded.
The methodology is called lean robotics, and its goal is to simplify the deployment of robots in factories.
Lean robotics is based on our experience in supporting thousands ofmanufacturers worldwide, many of them first-time robot users, whilethey successfully deployed robots.
I sincerely hope you’ll find it useful.
WHO THIS BOOK IS FOR
This book is a hands-on guide for anyone who wants to deploy robots to build stuff. Read on, and you’ll learn how to design, integrate, and operate robots on your manufacturing floor as efficiently as possible.
Whether you’re in charge of running a production operation or installing and maintaining production equipment, you’ll find a step-by-step guide to making robots work in your factory.
If you’re a manufacturing professional whose factory has already deployed robots, you’ll be able to apply the concepts in this book right away. I’ll show you methods you may not have considered, and point out ways to save time and money every time you work with robots in the future. You might be especially interested in the chapter on scaling up robotic cell deployment throughout your factory (or factories).
If you’re a technology provider or system integrator in the robotics industry, you’ll find fresh ways to look at the deployment process.These new approaches can help your collaborations with your manufacturing customers flow more smoothly.
[One assumption I make throughout this book is that you—the reader—work at a factory in the manufacturing industry. From now on, I’ll often use the words “you,” “manufacturer,”and “factory” as synonyms. (This prevents me from having to say “assuming you want to deploy robots on a manufacturing factory floor…” before every piece of advice.)]
Lean robotics, as you might have already guessed, is aligned with the lean manufacturing methodology (more on that soon). I’ve tried to avoid lean manufacturing jargon as much as possible; but just in case, you can find a glossary of lean manufacturing and lean robotics terms at the end of the book.
Most importantly, this book is designed to be self-contained. You don’t need to be an expert in lean manufacturing to use the lean robotics methodology.
HOW ROBOTICS CELLS ARE DEPLOYED TODAY
Robots come in many forms; but from now on, I’ll be using the word “robot” to refer to the robot arms—also known as industrial robots—used for manufacturing tasks.
What is a robot, anyway? If you’re a manufacturer who wants robots to work in your factory, then you can think of a robot as an “automatically controlled… manipulator” (to paraphrase the International Federation of Robotics’ definition, which is more detailed).
However, there’s not much you can do with just a robotic arm. You need other components too, which I’ll describe below. That’s why it makes more sense to talk about a robotic cell rather than just a robot.
In general, a cell is any station in the manufacturing process, such as on a production line, where a specific operation is being done. If the operation is done by a human, the station is known as a manual cell (see Fig. 1).
When factories install a robotic cell, their purpose is to automate a process. That process could be one that’s currently done at a manual cell, or it could be an entirely new function.
As you may have guessed by now, a robotic cell is simply a station that includes a robot (Fig. 1).
When you buy a robotic arm, it comes with two important things: the controller, which is the computer that drives its movement, and the teach pendant, which is the user interface that the operator uses to program the robot. These are shown in Fig. 2.
If you think of the controller as a conventional desktop tower, the teach pendant would be your monitor and keyboard.
What comes after the robot’s wrist, and what’s added around the robot, varies depending on the application. But no matter the application, your robot will always need to be equipped with other components in order to work properly (Fig. 2).
These components might include end-of-arm tools (grippers, welding torches, polishing head, etc.) and sensors (such as force-torque sensors, safety sensors, vision systems, etc.).
You’ll need to install the robot on your manufacturing floor by bolting it to a sturdy surface. Installation might also involve adding part-feeding mechanisms, safeguards like protective fencing, and more.
The robotic cell doesn’t only include hardware. The controller comes with some pre-installed software, but you will have to write the program: the list of instructions the robot will follow to perform a specific task.
Fig. 3 shows the main steps of the robotic cell deployment process: design, integrate, and operate.
- 1. The design phase includes all the tasks needed to go from the manual (or original) process to having the plan and materials for the robotic cell.
- 2. From there, the integrate phase consists of putting the pieces of the robotic cell together, programming it, and installing the cell on the production line.
- 3. The operate phase represents the end goal of deployment: having a productive robotic cell that does its job properly on an ongoing basis.
WHO PROVIDES WHAT?
When you buy a “robot” from a robotics company, you’re typically only getting the arm, controller and teach pendant. Most robot companies do offer other hardware and software add-ons, but these don’t cover every possible application.
That’s why a whole industry has sprung up around providing application-specific solutions—and it’s why the industrial robotics ecosystem is structured as shown in Fig. 4.
Different companies specialize in providing various pieces of the solution. Whoever does the cell deployment needs to put these solutions together themselves during the design and integrate phases.
The first two phases—design and integrate—can be done by an in-house team working for the manufacturer that has bought the robot, or by external contractors called system integrators. Of course, the buyer of the robot is responsible for operating it, so the third phase—operate—is done by the factory’s team.
ROBOTIC CELL DEPLOYMENT VS. ROBOTIC SYSTEM INTEGRATION
Throughout the book, we’ll be using the phrase “robotic cell deployment.” You might be more familiar with the similar-sounding term “robotic system integration.” But although these two phrases may seem similar, they actually have slightly different meanings.
ROBOTIC CELL VS. ROBOTIC SYSTEM
Lean robotics looks at a basic unit of production—a cell—that has a defined input, a process done by one operator, and an output.
A robotic system, on the other hand, can be a simple robotic cell, but it can also be much more complicated. It can include multiple robots, such as a production line station with 20 robots welding a car body simultaneously. Lean robotics is not the right tool for that kind of large, complex robotic system. It is a great fit, though, for a stand-alone cell with a single robot.
CELL DEPLOYMENT VS. SYSTEM INTEGRATION
Cell deployment includes the whole design-integrate-operate process, from defining the manual task to operating the robotic cell on the factory floor. By contrast, system integration typically covers the design and integrate phases only, and does not include the operate phase.
In lean robotics, we include the operate phase for a simple reason: the point of all of your work is to have the robot create value in the operate phase! So it’s important to include it in order to see how the other two phases contribute to this end goal.
WHAT’S WRONG WITH HOW ROBOTIC CELLS ARE DEPLOYED TODAY?
Even today, with all the powerful robotics technology available and the number of important problems it can solve, the majority of manufacturing tasks are not yet automated.
THE MAIN BARRIER TO ROBOTIC CELL DEPLOYMENT IS HIGH COST
For a typical project involving a single robot, you may have to pay US$80,000 for a standard robot and its components. Then a system integrator will add another US$170,000 for other materials and custom engineering. In total, a turnkey solution ends up costing around US$250,000.
At that price, the predicted return on investment (ROI) might not be high enough to justify the cost of automating a manual task.
The reason it’s so expensive is the complexity of robotic cell design and integration. Because of this complexity, a lot of costly project management, custom engineering, and specialized programming must be done. This is where the majority of the cost lies.
HERE ARE FOUR REASONS WHY ROBOTIC CELL DEPLOYMENT IS SO COMPLEX:
1. ROBOTS EVOLVED TO SUIT HIGH VOLUME, LOW-MIX APPLICATIONS
The first reason is historical. Industrial robots were originally developed to serve automotive body manufacturers. Cars are produced in high volume, and because the products are so similar (low-mix) the same robot program can be used for several years. This means car manufacturers can amortize the cost of their custom system integration over the high number of cars made.
Moreover, in this context, reliability, speed and precision are more important than ease of use and simplicity of programming. Many robots on the market today were optimized with these constraints in mind.
But the constraints faced by the car makers of the past are not the same as those in many modern-day industries, where the time and money it takes to set up (or adapt) a robot can be much more important variables in the ROI calculation.
2. THERE IS A LACK OF STANDARDS IN THE ROBOTICS INDUSTRY
The second reason for complexity is the lack of standards across the highly fragmented robotics industry. Robotics standards are like toothbrushes: everyone agrees we should use them, but nobody wants to use someone else’s.
As a result, each robot maker has its own unique controller and operating system. And they each support different communication protocols, which in many cases you must pay to use. No single vendor is dominant in the industry. So third-party developers who invest in one type of robot can only tap into a small fragment of the total market.
This is very different from an industry like smartphones, for example. If you build an application on a smartphone, you can use the display, microphone, camera, and GPS that are included with the operating system. Moreover, just two operating systems, iOS and Android, have captured the vast majority of the market. This has enabled a rich and diverse offering of applications from third-party developers.
In robotics, it’s as if developers have to wire subsystems (equivalent to a phone’s display, microphone, camera, etc.) together and get them to communicate using various communication protocols, before they can even start developing the app.
Thus, there is a lot of non-value-added work involved in robotics deployment. There’s the technical challenge of integrating technologies that were never meant to work together, and the human-dynamics challenge of coordinating different vendors and project stakeholders, each of which may have various non-overlapping areas of expertise. And finally, all of this hard work results in products that can only be sold to a tiny fraction of the total robotics market.
[What about ROS, the open-source robotic operating system platform developed by Willow Garage Inc.? In the book Rise of the Robots: Technology and the Threat of a Jobless Future (Basic Books, 2015), Martin Ford writes that “ROS is similar to operating systems like Microsoft Windows, Macintosh OS, or Google’s Android, but is geared specifically toward making robots easy to program and control. Because ROS is free and also open source—meaning that software developers can easily modify and enhance it—it is rapidly becoming the standard software platform for robotics development” (from chapter 1, “The coming explosion in robotics,” iBooks).
From this description, you might think ROS will soon provide a universal robotics standard. However, in reality it’s far from being widely adopted in a broad variety of industrial applications. Instead, ROS is mostly used in research labs, because it was mainly designed to help developers build robots that work in unstructured environments. As such, ROS simplifies the work of PhDs who build outstanding adaptive machines, but it does not simplify the work of factory engineers who are automating semi-structured tasks.
Moreover, industrial robot manufacturers tend to stick to their own platforms for both commercial and technical reasons. Most importantly, their own platforms are far more robust than ROS. And on the commercial side of things, having their own platforms serves as a barrier to switching suppliers. System integrators typically invest a lot in training, so for integrators there’s a high cost to switching to other robot vendors. These costs also mean that their customers at factories have an incentive to stick with the system they know.]
3. ROBOTS DEAL WITH THE PHYSICAL WORLD
Unlike computers, which deal with digital information, robots must deal with the physical world as well. The information world is clean. It’s made of bits, zeros and ones. The material world is messy. So even if robots had standardized hardware, communication protocols, and software, the fact is that the world around them can never be standardized.
Today’s robots are good at following clear, repetitive and logical instructions. They’re not as good at dealing with unstructured environments or improvising new methods.
The physics of the processes that the robot performs can also bring important deployment challenges. A typical example is welding. Reaching the right mix of part positioning, welding parameters and robot movement often means long hours of fine-tuning the robot’s programming.
So long as robot programs must be customized to handle real-word objects, robot deployment will remain complex.
4. MANUFACTURERS LACK EMPLOYEES WHO ARE SKILLED IN ROBOTICS
One of the most common reasons why manufacturers don’t use robots is that they lack employees with the robotics skills to manage them.
At many small and medium-sized enterprises (SMEs), there are no in-house robotics experts. A lack of internal skills doesn’t just limit a company’s capacity to take on a big robotics project; it can limit its ability to get started with just one robot.
Even if you think you have “in-house expertise,” you might find you don’t have as much of it as you would like. Factories might hire a few automation engineers with the idea that “robots” will be their responsibility, but those employees are often spread too thin, with too many other tasks to focus on robotic cell deployment.
Some multinationals have the same problem but at a different scale. When we work with large electronics contract manufacturers, for instance, they usually have robotics experts who can design sophisticated robotics solutions at the business’s headquarters. The challenge arises when they have to install and operate the robots locally (on the factory floor).
With contract manufacturers, it’s even harder to work around the lack of internal skills because production requirements can change quickly when a customer’s product is far more or far less successful than predicted.
THE TRADEOFF BETWEEN COST AND DIFFICULTY
Manufacturers looking to deploy robotic cells today have two choices. They can delegate the project to an external system integrator or they can decide to do it themselves. Both are viable options, but they involve tradeoffs between cost and difficulty.
If you want to do it on your own, you can end up paying less, but you’ll be dealing with complex aspects of deployment yourself. You might save time at first because unlike an external contractor, you’re already thoroughly familiar with your current manufacturing processes.
However, you have to be realistic about your team’s abilities. Even though your manufacturing and automation engineers are probably perfectly capable of learning how to use robots, consider how much they’re capable of learning while carrying out the robotic cell deployment at the same time—in addition to taking care of all their other responsibilities within the factory.
A system integrator, on the other hand, will provide a turnkey solution at a fixed cost. You will benefit from the expertise they’ve accumulated from past projects. But this benefit must outweigh the inefficiencies introduced by their need to manage the project from outside your company and learn your manufacturing processes.
Every integration project has a certain amount of overhead costs, so system integrators might be reluctant to take on smaller projects. And if you have an integrator do the deployment for you, you’ll remain somewhat dependent on the system integrator even after the robotic cell is installed (for maintenance, troubleshooting, etc.). All things considered, small projects might be both easier and more cost-effective for you to do by yourself.
To successfully deploy a robotic cell, you need team members with robotics skills, project management skills, and a deep knowledge of your manufacturing process (see Fig. 5).
The good news is you already have the most critical piece of the puzzle: knowing what your factory does that adds value for your customers.
The project management aspect is made easier when you use the lean robotics methodology. It clarifies the cell deployment steps and defines a common vocabulary, which will help you coordinate the project with different stakeholders.
Lean robotics will also help you pinpoint the technical robotics skills that your team needs to acquire for your specific business context.
Whether you choose to deploy the robotic cell on your own or with a system integrator, lean robotics will provide you with tools to make the process more efficient. A more efficient cell deployment project will be more cost-effective and provide a higher ROI.
By reducing some of the complexity of deployment, we’re in turn removing part of the cost barrier, enabling you to automate more applications on your factory floor. This—as shown in Fig. 6—is the chain reaction that we want to create with lean robotics.
A BETTER WAY: LEAN ROBOTICS
WHAT IS LEAN ROBOTICS?
Lean robotics is a method for efficiently deploying robotic cells in factories. The end goal—as with everything you do in your company—is to create value for your customers and drive business results.
Lean robotics isn’t about technology per se, even though the methodology is applied via the technology of industrial robotics.
It consists of:
- • Four core principles
- • Three phases covering the robotic cell deployment process
These principles and phases are shown in Fig. 7.
In the remainder of this book, I’ll explain the principles and present a comprehensive guide to the deployment process. Along the way, you’ll find in-depth examples, practical tools, and a section on business best practices that will help you succeed with lean robotics.
HOW LEAN ROBOTICS IS ALIGNED WITH LEAN MANUFACTURING
The lack of standards in robotics—of hardware, software, and technology in general—is hindering everyone’s robotic cell deployment efforts. So the last thing I’d want to do is add yet another set of tools that might be incompatible with your existing ones! Lean robotics avoids this issue because it’s well-aligned with lean manufacturing, a methodology that’s common wisdom in the manufacturing industry.
As a manufacturing expert, chances are you’re already familiar with many lean manufacturing concepts. Rather than start from scratch, I’ll show you how to build on these concepts as you carry out your lean robotics projects.
Lean manufacturing is about:
- 1. Customer value—Defining value from the customer’s point of view.
- 2. Value creation chain—Mapping the chain of activities that produce this value.
- 3. Waste elimination—Conserving resources and reducing waste along the chain.
- 4. Continuous improvement—Taking small yet steady steps towards perfection.
How do we apply all this to robotic cell deployment?
Robotic cells should not be treated any differently from the rest of the activities on your manufacturing floor. They are a means to an end: creating value for your customers. And as with lean manufacturing and agile programming, lean robotics is an iterative, bottom-up methodology.
With that in mind, we start by defining the customers and what they value:
- 1. Customer value—In a robotic cell, the “customer” is whatever step (or station) comes next on the production line. For this next station, “value” usually means receiving the right part, in the right way, at the right time, so the station can proceed with its operation.
- 2. Value creation chain—This can be different depending on what phase of the cell deployment you’re in. In the operate phase, you want to look at the value-added transformation that the robotic cell executes on the parts it receives. In the design and integrate phases, the activities form a chain that will ultimately only generate value once the robotic cell is used for production.
- 3. Waste elimination—To maximize the return on your robotic cell investment, you must minimize waste. And you should do it throughout the entire robotic cell deployment cycle—that means at the design and integrate phases, not just during operation.
- 4. Continuous improvement—Lean robotics favors a robot-as-a-tool, bottom-up robotic cell deployment approach. It also encourages you to build your internal robotics and project management skills so you can keep continuously improving your robotic cell just like the rest of your production line.
By comparing Fig. 8 with Fig. 9, you can see how the lean robotics approach is aligned with that of lean manufacturing.
Waste reduction is another important way in which the two approaches are aligned. Even though a big chunk of this book focuses on how to deploy a single robotic cell (with the design, integrate, and operate phases), the “lean” waste reduction aspect really comes into play when you’re scaling up your efforts and deploying multiple cells.
Everyone knows it’s important for newly-installed robots to be productive once they’re up and running. But what many robotics users often don’t realize is that productivity is just as important during the design and integrate phases.
Today, these first two phases involve a tremendous amount of waste. You have to spend time communicating what the project’s about to your team members, waiting for equipment to arrive, debugging your programs, re-engineering things that someone has certainly done before…
We tend not to question whether all this is necessary because it seems like creative, problem-solving engineering work. But that’s where we’re wrong! All this waste leads to a hugely negative impact for your company, because these two phases have a tremendous leverage effect in both the short and long terms. Each step of the design and integrate phases should be about creating value for the customer while reducing as much waste as possible.
When you have a robotic deployment project done on time, and done correctly the first time, as opposed to one that’s completed three months behind schedule, you have an additional three months’ worth of automated production. Plus, when you structure your work so that components of your first project can be reused in your next one, you can reduce your deployment time and increase the ROI. In practice, I’ve seen manufacturers obtain a 50% shorter deployment time and 50% higher ROI in their second cell deployment project, simply by following lean robotics practices with the first cell deployment.
HOW ROBOTS CAN AFFECT YOUR LEAN MANUFACTURING EFFORTS
In the attempt to make factories more “lean,” robots can be both ahelp and a hindrance.
Sometimes robots can introduce new sources of waste that mightactually work against your lean manufacturing efforts, such as in thefollowing cases:
- • A robotic cell that requires new non-value-added tasks to be done.
- – For example, if parts arrive at the robotic cell inunstructured packaging that the robot cannothandle, a human operator might have to manuallyplace the parts in a mechanical fixture so the robotcan pick them. The creation of the fixture and theoperator’s work are both non-value-added activitiesthat were not part of the process before therobot was introduced.
- • A robotic cell monument (see glossary) that reduces yourfactory’s flexibility.
- – A typical example of a monument is the massiverobotic cell in a car factory that pairs the chassiswith the car’s body. In order to work, theseso-called “marriage cells” require two separateproduction lines (one for the chassis, one for thebody) to converge at a specific point in space andtime. All other materials must flow in alignmentwith this cell, so it’s difficult to change the factory’slayout when improvements need to be made.
However, these costs are often outweighed by the many benefits robots can bring to your lean manufacturing efforts, such as:
- • Improvement of product quality.
- – Because robots are excellent at doing the exact same operation again and again, they have the potential to improve your production line’s consistency and reduce the number of defective products.
- • Elimination of human ergonomic constraints on the production line.
- – Sometimes the production line’s capacity is constrained by human limitations, such as when manual operators simply cannot go any faster. If that’s what’s slowing down production, robots can increase your output.
- • Time savings.
- – Even if robots don’t reduce production time directly, it’s better to have a robot standing idle than a human employee or a multimillion-dollar machine.
- • Prevention of human health and safety issues.
- – For example, one factory was able to eliminate workers’ carpal tunnel problems by having a robot take over the tasks that were causing them.
- • Renewed focus on waste reduction practices.
- – When you use robots, you’re forced to sort through the work process and standardize tasks and parts. You also have to ensure the parts are delivered to the robot in a consistent manner, and that they’re ready for the robot to work on. In doing so, you’ll automatically apply lean manufacturing waste reduction practices by eliminating some non-value-added tasks (such as part preparation, cleaning, etc. by manual operators).
- • Automatic error-proofing (see glossary).
- – For example, let’s say you have two parts of different sizes being presented to the robot. The robot gripper needs to be able to recognize when it’s presented with the wrong part, so you could add a mechanical or software solution for doing so.
- – Similarly, the robot can signal when something’s gone wrong at the station (making use of the lean concept andon, see glossary). The robot can go into a specific visible position or cause a light to flash, letting human operators know they need to take action.
- • Avoidance of wasted human potential.
- – Humans can create much more value in your factory when they’re working creatively rather than repeating the exact same motions day after day. Robots can take care of this necessary yet low-value-added work instead; and workers can take on higher-impact tasks.
Clearly, the amount of waste that may be added or removed is just one aspect of lean manufacturing. So you might not care about additional waste induced by robots if they can help your factory achieve other goals, such as increasing output, improving quality, or shipping products on time.
That’s why it’s up to you to evaluate the pros and cons of robots with respect to your factory’s unique context—in terms of both your lean manufacturing efforts and your business’s overall goals.
PRINCIPLES OF LEAN ROBOTICS
The four principles presented in this section will help you make sound decisions throughout the entire deployment sequence.
1. PEOPLE BEFORE ROBOTS
Isaac Asimov, a brilliant science fiction writer and professor of biochemistry, famously came up with the “Three Laws of Robotics”:
- 1. A robot may not injure a human being or, through inaction, allow a human being to come to harm.
- 2. A robot must obey the orders given it by human beings except where such orders would conflict with the First Law.
- 3. A robot must protect its own existence as long as such protection does not conflict with the First or Second Laws.
Modern artificial intelligence is not as advanced as in Asimov’s stories. Until it is, these rules must be administered and followed by those of us who deploy and program robots, rather than by the robots themselves.
With that in mind, a simple way to summarize the Three Laws is with the principle of people before robots.
This principle has two components:
- A. Robotic cells must be safe for humans.
- B. Robots must be tools usable by all.
These are the guidelines that we, and all members of the robotics community, must abide by if we are to make robots work for us.
A. ROBOTIC CELLS MUST BE SAFE FOR HUMANS
Worker safety is a core aspect of our society’s values and legal regulations (or at least it’s intended to be), and we must strive to uphold it. Like everything else in your factory, robots should not harm humans.
So, how do you make sure your new machine will be safe for everyone around it? The process usually follows these steps:
- 1. Evaluate the risk.
- 2. Mitigate the sources of risk until they reach an acceptably low level (in terms of the combined likelihood of occurrence and expected severity).
This process is called a risk assessment. Just as you would when adding any new machine, a risk assessment should be performed while planning the deployment of a robotic cell.
Your risk assessment must be done in accordance with the following:
- • Corporate safety rules and guidelines.
- • Local regulations on workers’ safety.
- • Guidelines published by the ISO (International Standard for Organization) and/or a country-specific equivalent.
The ISO publishes several standards regarding the safety of robotic systems and collaborative robots. While these standards are only guidelines, they’re often used as the basis for the law, so it’s worth becoming familiar with them.
Need help with safety issues? Here are some resources:
- • External robotic system integrators
- • Robotics industry associations, many of which offer training in robotic safety
- • Machinery safety experts who are proficient in robotic risk assessment
The bottom line is that robots must serve humans; obviously, the last thing they should do is hurt them!
Keep in mind that robots can also improve workers’ safety. For example, one company, a furniture manufacturer, now uses a robot to feed sheet metal into a punch press. Before introducing the robot, a human operator was exposed to the dangers of sharp parts and the punch press.
B. ROBOTS MUST BE TOOLS USABLE BY ALL
This means we should aim to make robotic cells that are accessible and understandable by everyone. From a lean manufacturing standpoint, there are two main benefits.
First, if robots can be used and adapted by all your workers, it will create great synergy in your business: humans can identify areas for improvements, and robots can follow their instructions.
When workers gain robotics expertise, they’ll start looking for more opportunities to use robots to improve productivity, ergonomics, output quality, etc. In this way, you’ll be implementing the “continuous improvement” aspect of lean manufacturing on the factory floor. So even if workers can’t deploy the robots themselves on day one, they’ll soon be able to contribute by identifying problems robots can solve.
It’s of great strategic importance that you start building that expertise today. If you do, then over time your team’s skill level will increase while robotic technologies become easier to use. By narrowing the skills gap from both of these angles, you’ll have more people ready to deploy robots as quickly as possible—ideally much sooner than your competitors.
Second, implementing this principle is also a way to avoid the risk of having too few people who understand how to use the robot(s).
For example, I once met an owner of a small metal job shop who had trouble hiring enough welders to fill his orders, so he decided to invest in his first robotic cell. He programmed the robot himself and operated it to great success. But when other aspects of his business began demanding more of his attention, he no longer had time to run the robot.
He wasn’t able to find a robot programmer he could hire to replace him, and he couldn’t program new additions to the robot himself. Eventually he was forced to transition his shop back to manual welding, because even though it was hard to find welders, they were still easier to find than robot programmers.
Imagine if the robot was simple enough to become another one of the welder’s tools—if instead of needing one programmer (who knows nothing about welding) to teach the robot, the shop owner could have had one welder teaching 10 robots? Then the welder’s value-creating knowledge could be leveraged across multiple robotic cells.
WHAT DOES IT TAKE TO HAVE ROBOTS BECOME TOOLS AVAILABLE TO ALL WORKERS?
Your priority is to choose robot technologies that can do the jobs they’re intended for, while being operable by as many people as possible in your factory. That could mean choosing robots that are controlled by the most user-friendly interfaces or the simplest programming commands, so you can train more workers to use them.
As new technologies become available, it will become easier for more people to use them, since user-interfaces are constantly being updated. However, in the meantime your organization will still have to work to ensure its employees can use them.
Even if you can’t achieve “robots as tools for all” from day one, you’ll find it worthwhile to at least have several people able to operate, maintain, and improve your robotic cells. That way, your robotic workforce will be more adaptable to your business needs, and your key engineers will be able to focus on high-impact robotic projects rather than lower-level maintenance work.
A NOTE ON “PEOPLE BEFORE ROBOTS”AND THE FUTURE OF JOBS
“People before robots” might seem like an idealistic notion that can’t (or won’t) be applied in reality, especially if you listen to what mainstream media outlets have to say on the topic.
It seems not a day goes by without a new article popping up on my Twitter feed, blaring something along the lines of “Robots are stealing your jobs.” So I can see why some might question how people can be more important than robots, if robots will end up taking over people’s jobs.
In response to these concerns, the robotics industry often likes to get out their PR team and launch a counter-attack, attempting to explain why in fact robots are creating a net increase in jobs.
But I think both parties are missing the point.
The robotics industry’s usual argument is that companies and countries that use robots create more jobs. However, the most innovative companies also use more robots—and obviously, more innovative companies are likely to do better financially, and hence create more jobs.
Since innovative companies are more successful, and the use of robots can indicate innovation in manufacturing, that could be where this trend is coming from. Perhaps robots are not necessarily causing the job creation; they might simply be correlated with it.
On the other hand, it seems the media have got it backwards. Rather than worrying about robots stealing our jobs in 20 years, we should be worrying about the number of jobs going undone right now because manufacturers can’t find people to do them!
For the most part, manufacturers aren’t bringing in robots to replace people—they’re bringing in robots because they don’t have enough people.
This phenomenon—of being unable to find enough human workers to fill job openings—is known as the skills gap, and it’s affecting manufacturers worldwide. Although the extent of the skills gap in other sectors of the economy is widely debated, a gap certainly exists in the manufacturing industries of countries such as the United States, Canada, and China.
As Cait Murphy explains in an article for Inc., “It is not so much that the U.S. has a skills gap [overall], but that there are specific issues in specific places.”
I’ve seen this first-hand here in Canada, where one of Robotiq’s customers is a machinery maker. The business cannot find enough workers to serve all its customers. Any employee they can bring onboard has a direct impact on their revenue, because every additional employee means they can fulfill many more orders.
Another factory in the small town of Bromont, Québec, sends a shuttle to bring in workers from Montreal every day—a 185 km or 115 mile journey, round-trip—because too few of them are willing to move to Bromont permanently.
And as Murphy goes on to say in the same article:
One of the areas in which there is undoubtedly a skills shortage now (and a bigger one looming) is welding; the average age of a welder is 55, and the country could be short as many as 291,000 of them by 2020, according to the American Welding Society.
Moreover, deploying robots in factories doesn’t mean getting rid of all workers, since humans will still be needed for creative work, strategic-thinking tasks, and operation of robots.
Some may agree that humans will still be needed in the short term, but object that in the long-run, machines are destined to become more intelligent than humans—and if that happens, even marketing teams and managers will likely find themselves replaced by robots.
However, if machines become more intelligent than humans, lots of things will change. We don’t know what will happen, exactly… and neither does anyone else. The best we can do is focus on what’s within our control right now (see Fig. 10).
The fact is that robots will inevitably be put to work in greater and greater numbers. There’s no point arguing whether or not this is a good thing. Instead, we should focus on solutions and how we can make sure the shift towards robots in factories is done right.
At this point you might be wondering: if greater automation is inevitable, why should you bother reading this book? Well, just because something will happen eventually, doesn’t mean you should sit idly by while the world changes around you. Whether you’re a CEO, manager, factory worker, or student, you can start benefitting from robots today—and the rest of this book will show you how.
2. FOCUS ON THE ROBOTIC CELL’S OUTPUT
Your job as a manufacturer is to profit from making products that consumers are willing to pay for. This is why lean manufacturing is popular with so many companies: it helps the manufacturer focus on creating value for the consumer while eliminating waste along the way.
In lean manufacturing, the overall goal is to better serve whatever company or person is giving money to your business—the external customer. It’s easy to define “value” from the external customer’s perspective, since it’s the reason why the consumer is willing to exchange cash or another form of payment for your product (or service).
To achieve the end goal of lean manufacturing, you sometimes have to focus on serving the internal customer first. The internal customer is the process, station, department, etc., that will receive a given output within the factory.
In lean robotics, the main focus is always on serving the internal customer, and it’s defined as whatever station comes after the robotic cell in the production sequence. This “customer” obviously doesn’t pay for things with currency—instead, it defines value as receiving the right parts, with the right presentation, at the right time, so it can in turn create value.
Keep in mind that in both lean manufacturing and lean robotics, an activity is considered value-added if it meets the following three criteria:
- 1. It must transform the product or service.
- 2. The customer must be willing to “pay” for it.
- 3. It must be done correctly the first time.
Accordingly, in the design and integrate phases you’re adding value by creating a robotic cell that’s ready to operate—the robotic cell itself is your “product.” Anything that doesn’t directly contribute to having a working robotic cell is non-value-added.
In the operate phase, the product is whatever the cell is delivering to the next station in the manufacturing process. And what’s valuable for that next process is to receive the right parts, the right way, at the right time to be able to do its job.
Now, “non-value-added” doesn’t mean “useless.” Many non-value-added tasks, such as packaging, are still inherently necessary.
With packaging, for instance, the external customer is paying for the product, not the packaging, yet the product must be packaged in order to be shipped.
Since non-value-added tasks can still be necessary, it’s possible for a robotic cell to provide value to its customer by doing a non-value-added task.
For example, your robotic cell could be a quality control station that checks whether the previous station output non-defective parts. The robotic cell’s customer might be the shipping department, which values receiving non-defective parts. So this robotic cell provides value to its customer by identifying defective parts, even though this is not actually a “value-added” process.
A simple rule of thumb for robotic cells in the operate phase is that process-oriented tasks, such as welding, polishing, painting, and assembly, are typically value-added. By contrast, material handling tasks are typically non-value-added. These include machine loading/unloading, packaging, palletizing, inspection, and quality assurance.
To summarize, the principle of focusing on the robotic cell’s output means the following:
- • The robotic cell must create value for its customer.
- a. The robotic cell customer is the next station in the production sequence—the one that receives the robotic cell’s output as an input.
- b. This customer defines value as receiving the right parts, with the right presentation, at the right time, so it can in turn create value.
In the design phase of deploying the robotic cell, you should start by answering this question: what is the value that the robot should be creating for the next station on the factory floor? If you fail to sort out how your robotic cell will create value for the next station, everything you do in the design and integration phases will be worthless. This puts the emphasis on delivering a reliable, working robotic cell the first time.
Another aspect of starting with the end in mind is targeting the simplest possible cell that will do the job. The lean robotics approach for the deployment of any robotic cell is to first target the minimum viable robotic cell.
Product development teams use the concept of minimum viable product. The MVP is defined as a product with just enough features (and no more) to satisfy early customers, who will provide feedback for future development. This approach brings advantages in a highly dynamic environment, where information is gathered while the product is still evolving. The goal is to create, within the constraints of minimum cost and time, a product that the consumer is actually willing to pay for.
The minimum viable robotic cell (MVRC) is the robotic cell with just enough features (and no more) that can reliably create value for its customer.
Here’s why the MVRC approach is the right way to go:
- • The work done at the design and integration stages can only create value if the cell ends up working reliably in the operation stage. Adding complexity could diminish the value that can be created by the robotic cell, because it may delay the launch date and reduce reliability.
- • Robotic cell design and integration almost always takes longer than expected. It’s sometimes tempting to add features along the way, but you should stick with what you need and avoid the “nice to have’s.”
- • The context in which your cell operates will probably change along the way. You can’t possibly know all the relevant information at the beginning of the design stage—first because all the stakeholders will be learning throughout the deployment process (about robot possibilities, limitations, effects on other factors, etc.), and second because the company’s environment—both physically and in the business sphere—might be changing rapidly. The more time it takes to deploy the robotic cell, the more likely it is that the context will have changed by the time it’s operating. That’s why the cell design should be kept flexible enough to remain open to future improvements.
- • Your robotic cell will need to evolve to keep up with future developments, so you should view the robotic cell deployment project not as a final destination, but as another step in your lean manufacturing journey.
- • One last important aspect related to this principle is that you should measure how much value the robotic cell is producing for its customer (the next station). This will be the basis for your evaluation of whether the robotic cell is doing its job the way you had planned. It will also be a key metric to track while you aim for continuous improvement of the cell. I’ll talk about this more later, but for now just keep in mind that you should start by focusing on customer value, which involves coming up with the minimum viable cell, and thinking about how you’ll measure the value it creates.
3. MINIMIZE WASTE
Every time energy is transferred, some waste is inevitable. There is no known process in which 100% of the input is transformed directly into the desired output. Car motors can’t convert all their fuel into movement, solar panels can’t convert 100% of the solar energy they receive into electricity, and you don’t obtain nutrients from 100% of the food you eat.
It’s the same in a business. The various processes are never 100% efficient.
In lean manufacturing, waste is defined as energy and money that is spent but not converted into value for the customer. So for a business, waste is the difference between the energy and money we put into something, and the actual result that we get.
Lean manufacturing defines three broad categories of waste:
- 1. Mura—Waste due to variation.
- 2. Muri—Waste due to overstressing or overburdening people or equipment.
- 3. Muda—An activity that consumes resources without creating value for the customer.
Muda is typically broken down into seven specific types of waste:
- 1. Transportation—Non-value-added movement of parts, materials, or information—both within the factory, and between it and its partner institutions (other plants, suppliers, warehouses, etc.).
- 2. Waiting—When people, parts, systems, or facilities stand idly by while they wait for a work cycle to be completed.
- 3. Overproduction—Producing outputs more quickly, or in greater quantities, than customers demand.
- 4. Defects—Producing outputs so flawed that customers would deem them unacceptable.
- 5. Inventory—Accumulating leftover raw materials, works-in-progress (WIPs), or finished goods that will not contribute to value creation.
- 6. Movement—Unnecessary movement of workers, materials, or equipment during a single processing step or within a single station.
- 7. Extra Processing—Performing additional work, even though it is not required to meet the customer’s standards.
There is an eighth type of muda—one that’s not always defined in lean manufacturing, but is perhaps the most important type in lean robotics:
- 8. Underutilizing Human Potential—When employees are capable of making greater contributions, yet prevented from doing so because of the other tasks they need to perform.
We’ll discuss at various points in the book how lean robotics can impact the different types of waste and what to do about it. It’s important to reduce waste throughout the entire cell deployment cycle.
When deploying the robotic cell, we tend to focus on reducing waste at the operate stage, because that’s the easiest place to do so. You know exactly what your inputs and outputs are, so it’s easy to track them. But lean robotics is about optimizing the design and integration stages as well.
As a manufacturer, the production floor isn’t the only area that should be concerned with productivity. It should also—and perhaps even moreso—be at the forefront of your engineering teams’ minds. Everyone knows waste must be eliminated on the factory floor, and it’s easier to assign numbers to activities performed on the production line (like seconds, dollars, etc.), but remember: you should be paying just as much attention to the robotic deployment tasks performed by engineers and technicians, because they have an important leverage effect.
Let’s say you deploy robots with an internal team and start a timer the day you receive the equipment. If the robotic cells can’t start production until two months after they were supposed to, the point where you’ll break even on your investment will be at least two months delayed, and possibly even more considering the extra costs incurred by those delays. If the challenge you want to solve with the robot is to increase capacity, then the cost is even higher: it’s the lost chance to make use of the extra capacity that would have been provided by the robots over the two months, had they been working on schedule. Depending on what you’re producing, the negative financial impact of delays can be significant.
Fig. 12 depicts two timelines: one showing the impact of non-value-added activities in a typical robotic cell deployment project like thisone, and one showing the ideal scenario, where non-value-added activities have been eliminated.
This image illustrates the positive impact of reducing waste throughout the cell deployment cycle.
We can categorize waste in robotic cell deployment phases according to the eight types of lean manufacturing waste.
If you’re a manufacturing engineer, the idea that you should avoid these types of waste in the operate phase is probably already clear to you. However, you should be paying just as much attention to waste in the design and integrate phases as well.
In the section on scaling up your robotic cell deployment, we’ll cover several tools that will help you identify and reduce waste across robotic cell deployment projects.
4. LEVERAGE YOUR SKILLS
At this point you might be asking “Who cares about building ‘internal’ robotics skills? All I want to do with my robotic cell is set it and forget it. Can’t I just subcontract it out to an external system integrator?”
Those “set and forget” robotic applications might sound compelling, but unfortunately they often won’t align with the reality of your factory’s needs. A factory floor is a dynamic place: new products are developed, existing ones are improved, capacity is adjusted up and down, new regulations are introduced, customer requests are handled… The set and forget applications, by contrast, are designed for a single purpose, so implementing them will limit the potential positive impact of robots in your factory. So you can see why deploying the robotic cell with your own team, using the bottom-up lean robotics approach, is a much more flexible option than outsourcing.
Imagine the benefits of leveraging your skills over time. If your factory could potentially make use of 10 robotic cells, and you’re able to install each one quicker and less expensively than before, how much would this increase your return on investment? Some of our customers have deployed hundreds of robotic cells by themselves. As they progressed, their robotic cell deployments became easier, more reliable, more cost-effective, and quicker to generate value. The keys to this leverage effect are reusing the human skills (learning) and robot skills (technological building blocks) that are developed in early projects.
Of course, there’s only so much you can improve. In manufacturing, the path towards perfection is asymptotic: you can gradually get better, but you’ll never quite reach perfection. Plus, “perfection” is a moving target because the context is changing all the time. In lean robotics, there’s no point trying to be completely perfect today: it’s impossible and you’ll only end up over-engineering your robotic cell.
What you should do is take small steps in the direction of perfection. So what does perfection mean here? What would be the perfect lean robotics implementation for your factory? To answer that question, you should take a holistic view of your enterprise:
- • Evaluate the long-term potential of lean robotics for all your operations.
- • Find the right balance of deployment costs vs. benefits, for the short-term vs. the long-term.
If you have a small shop with only one application that could use a robotic cell, your perspective on long-term lean robotics will be limited to this single application. In your situation, focus on first deploying the minimum viable robotic cell (MVRC). Once your MVRC has started generating value, evaluate how you can improve it to support your lean manufacturing efforts. But don’t try to do it all at once. Keep in mind that you will learn important lessons and that your environment and technology will keep evolving. So delivering one working cell and then improving it will be smoother and more rewarding than trying to do everything simultaneously.
However, if you’re like most of the manufacturers I’ve encountered in the last decade, your first robotic cell will not be your last. It may seem daunting at the start, but once you’ve overcome the challenge of installing your first cell, you’ll already be looking for the next one. And you’ll be well on your way to leveraging your skills.
Keeping the four core principles in mind, now let’s see how to put them into practice in the lean robotics cell deployment cycle. Continued in Part 2.
Get the complete eBook HERE.
Samuel is CEO and co-founder of Robotiq. His mission is to free human hands from repetitive tasks. He is also the author of Lean Robotics: A Guide to Making Robots Work in Your Factory. He lives in Québec City with his wife and four children.